The steel products manufacturing industry is highly regulated, and many companies find it challenging to adhere to complex and constantly changing regulations. In the international market, steel products, especially those used in heavy industries, are subject to careful scrutiny and quality control processes. To meet these requirements, a steel manufacturer must follow proper protocol and have efficient procedures in place to maintain consistent quality standards.
In this case study, we dive into the compliance success story of an Australian-based steel products manufacturer. This company was able to achieve ISO 9001:2005 compliance and ISO certification with the help of Effivity's specialized Quality Management System Software and custom solutions.
Let's learn more about the company, the challenges it faced, and the solutions offered by Effivity.
About the Company
Since 1998, an Australian company has provided reliable solutions to clients in heavy industries. Renowned as a trusted supply chain partner, they ensure the quality of every product through local stocks and international orders of certified goods. Their team, known for deep technical expertise, drives their success by delivering products backed by industry-specific knowledge.
Over two decades, they've built strong relationships with global steel manufacturers and fabricators. To serve customers efficiently, they strategically hold stock in key regions, reinforcing their commitment to quality and timely delivery.
Challenges Faced
Here are five challenges the Australian-based company faced before adopting Effivity QMS Software:
- Difficulty in maintaining consistent compliance with ISO standards. This resulted in inefficiencies in their quality management processes.
- Challenges in managing and tracking non-conformances hindered the ability to conduct thorough root-cause analyses.
- Limited visibility and management of customer complaints, affecting customer satisfaction and quality improvement efforts.
- Inefficient processes in identifying and mitigating workplace hazards, posing risks to employee safety and operational continuity.
- Struggles in accessing and communicating key performance indicators and organizational processes, resulting in less informed decision-making.
Solutions Offered by Effivity
Effivity provided the Australian-based steel manufacturing company with a suite of modules and features designed to improve and enhance its Quality Management System (QMS). The solutions implemented addressed various aspects of their operations, compliance, efficiency, and process management.
1. Compliance Management Module
The Compliance Management Module helped the company maintain ISO 9001:2015 certification. This module enabled a systematic approach to managing regulatory requirements, ensuring all processes adhered to the necessary standards. By minimizing redundancies and optimizing resources, the company improved its overall compliance efficiency and reduced the risk of non-compliance.
2. Document Management Module
Effivity's Document Management Module played a vital role in organizing and maintaining documentation. The company benefited from a centralized system where all QMS-related documents were stored, tracked, and updated in real time. This module ensured that the latest versions of documents were easily accessible, reducing the risk of outdated information affecting operations.
3. Non-Conformance Module
Addressing non-conformances became more efficient with the Non-Conformance Module. This feature allowed the company to capture and analyze non-conformances promptly. By conducting thorough root cause analyses, the company could implement corrective actions effectively, preventing recurrence and enhancing product quality. This module contributed significantly to improving operational consistency.
4. Risk Management Module
The Risk Management Module empowered the company to manage potential risks proactively. It facilitated the identification, assessment, and ranking of risks, helping the company develop appropriate mitigation strategies. This approach to risk management enhanced workplace safety and ensured that operations were more resilient to unexpected challenges.
5. Comprehensive Dashboard
Effivity provided the company with a Comprehensive Dashboard, offering a detailed view of its QMS performance. This feature enabled the company to monitor key performance indicators (KPIs) in real time, supporting data-driven decision-making. The dashboard's global accessibility ensured that stakeholders could access critical information from any location, enhancing collaboration and transparency.
Benefits of Using Effivity
Here are the benefits experienced by the Australian company after adopting Effivity:
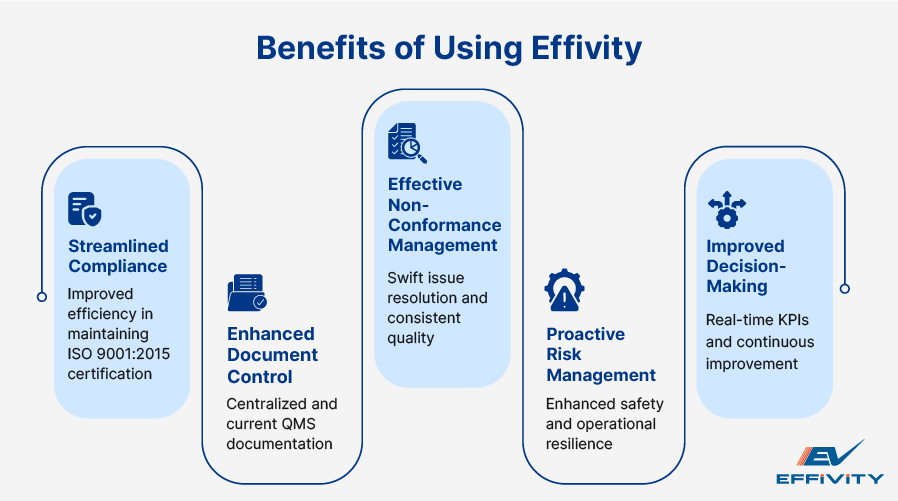
- Streamlined Compliance Processes: The company saw improved efficiency in maintaining ISO 9001:2015 certification, with reduced time and resources spent on compliance activities.
- Enhanced Document Control: Effivity's Document Management Module centralized and simplified document handling, ensuring that all QMS documents were current and accessible, reducing the likelihood of errors.
- Effective Non-Conformance Management: The Non-Conformance Module allowed the company to swiftly capture, analyze, and address non-conformances, leading to more consistent product quality and efficient operations.
- Proactive Risk Management: The Risk Management Module enabled the company to identify, assess, and mitigate risks effectively, contributing to improved workplace safety and operational resilience.
- Improved Decision-Making: The Comprehensive Dashboard provided real-time access to key performance indicators (KPIs), supporting data-driven decisions and facilitating continuous improvement across operations.
In Conclusion
The Australian-based steel manufacturing company experienced significant improvements after adopting Effivity's QMS software. Compliance processes became more efficient, reducing the time and resources required to maintain ISO 9001:2015 certification.
Wish to experience similar success in your organization? Contact the Effivity team today and set up a consultation!
Frequently Asked Questions
What are the major requirements of ISO 9001:2015 for the steel manufacturing industry?
ISO 9001:2015 requires you to establish a Quality Management System (QMS) that includes leadership commitment, risk management, and customer focus. You must ensure consistent product quality and documentation processes and monitor performance. Employee competence is also necessary to maintain compliance and achieve high standards in your steel manufacturing operations.
What documentation is required for ISO 9001:2015 compliance in steel manufacturing?
For ISO 9001:2015 compliance, you need to document a Quality Manual, quality policies, and detailed process descriptions. Maintain records of risk assessments, internal audits, training, and corrective actions. Document control procedures and performance monitoring records are also necessary to demonstrate compliance in your manufacturing processes.
How often should steel manufacturing companies undergo audits for ISO 9001:2015 certification?
You should undergo internal audits at least annually to ensure your QMS remains effective. Certification bodies typically conduct external surveillance audits every year, with a full recertification audit every three years. Regular audits help you identify areas that need improvement and ensure compliance with ISO 9001 standard requirements in manufacturing operations.
What common challenges do steel manufacturers face in maintaining ISO 9001:2015 compliance?
You may face challenges such as keeping documentation up to date, managing non-conformances, and ensuring consistent employee training. Adapting to changing industry standards and maintaining continuous improvement efforts can also be difficult. Balancing these requirements while maintaining efficient operations is essential to sustaining ISO compliance in your steel manufacturing processes.