A company specializing in slitting and roll-finishing techniques recently overhauled its quality management system with the help of Effivity. This industry demands precision, consistency, and compliance with international standards like ISO 9001:2015.
In this case study, we look at how the company transitioned to ISO 9001:2015 and maintained compliance using Effivity's specialized QMS software.
About the Organization
The organization is a prominent high-tech converting firm in the US, recognized for its expertise in slitting, roll-finishing, and advanced material handling techniques. This high-touch firm had previously held ISO 9001:2008 certification and sought to transition to the updated ISO 9001:2015 standard.
During this transition, the business and its stakeholders focused on improving quality management practices and enhancing operational efficiency. There was a consistent effort to align their processes with the new standard's requirements.
The organization prioritized ensuring that all aspects of its operations met the rigorous demands of ISO 9001:2015. This alignment aimed to maintain high product quality and customer satisfaction while streamlining internal workflows.
Challenges Faced
Achieving QMS certification required the organization to overcome several significant challenges. Transitioning from ISO 9001:2008 to ISO 9001:2015 was not just a matter of updating documents but involved a comprehensive overhaul of their quality management system. The firm had to ensure that all processes, documentation, and training were up to the new standard's requirements, which presented multiple hurdles.
1. Understanding New Requirements
The transition to ISO 9001:2015 introduced several new requirements that the organization needed to understand and implement. The updated standard placed a greater emphasis on risk-based thinking, leadership involvement, and context of the organization. This required the company to thoroughly analyze and interpret the new clauses to ensure full compliance, which was both time-consuming and complex.
2. Documentation Overhaul
With the new standard came the necessity to update and overhaul all existing documentation. The previous documents needed revision to meet the revised requirements of ISO 9001:2015. This involved a detailed review and modification of quality manuals, procedures, and records.
Creating new documents to fill any gaps identified during the transition was also necessary, making the documentation process extensive and meticulous.
3. Employee Training
To maintain QMS certification, it was essential that all employees were trained and well-versed in the new requirements of ISO 9001:2015. The company faced the challenge of designing and implementing a comprehensive training program that covered all aspects of the updated standard.
4. Resource Allocation
The company had to balance its daily operations with the demands of achieving quality management system certification. This required careful planning and allocation of time, personnel, and financial resources. Ensuring that the transition did not disrupt normal business activities while still meeting all ISO 9001:2015 requirements was a delicate balancing act.
5. Maintaining Certification
Once the transition to ISO 9001:2015 was complete, the organization faced the ongoing challenge of maintaining their QMS certification. This required continuous monitoring and evaluation of their quality management system to ensure ongoing compliance. Regular internal audits, management reviews, and corrective actions were necessary to keep the system aligned with ISO standards and to prevent any lapses in compliance.
Effivity's Solution
Effivity is a leading cloud-based QMS software designed to help organizations achieve and maintain ISO certifications. Its user-friendly interface, comprehensive modules, and support make it a great choice for businesses looking to streamline their quality management processes.
Effivity's integrated approach ensures that all aspects of quality management are covered, providing a one-stop solution for companies transitioning to ISO 9001:2015.
Key Modules of Effivity's Solution
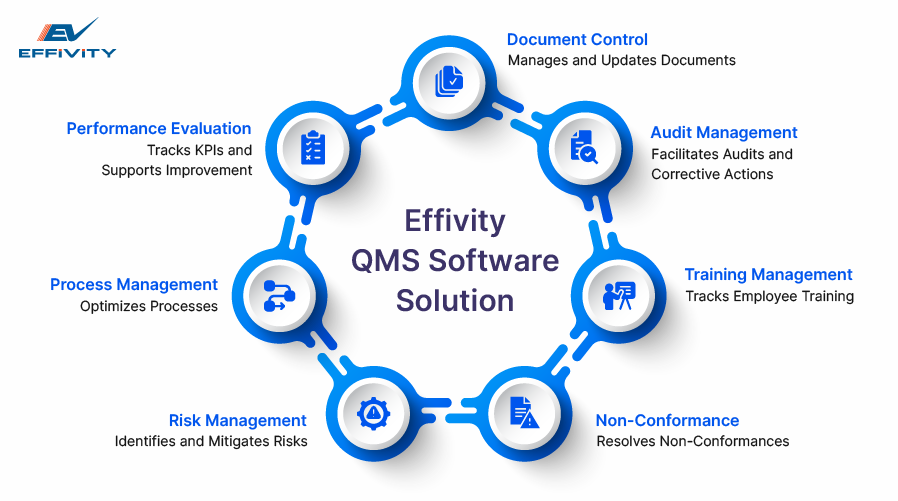
1. Document Control Module
The Document Control Module helps manage the creation, review, approval, and distribution of documents. It ensures that all documents are up-to-date and accessible to authorized personnel. For the firm, this module streamlined document management, reducing the risk of outdated information being used and ensuring compliance with ISO 9001:2015 documentation requirements.
2. Audit Management Module
The Audit Management Module facilitates the planning, execution, and documentation of internal audits. It helps track audit findings and ensures that corrective actions are implemented effectively. This module enabled the firm to conduct thorough internal audits, identify areas of improvement, and maintain compliance with ISO 9001:2015 audit requirements efficiently.
3. Training Management Module
The Training Management Module manages employee training programs, tracks progress, and ensures that all staff are knowledgeable about QMS processes. For the company, this module provided a structured approach to training, ensuring that every employee understood their role in the quality management system and helped maintain high standards of compliance.
4. Non-Conformance Management Module
The Non-Conformance Management Module tracks and resolves non-conformances efficiently. It identifies root causes and implements corrective actions to prevent recurrence. This module helped the firm address non-conformances promptly, ensuring that any deviations from quality standards were corrected swiftly, thus maintaining the integrity of their QMS.
5. Risk Management Module
The Risk Management Module implements risk-based thinking by identifying, assessing, and mitigating risks. It facilitates potential issues to be addressed before they become problems. For the company, this module provided a proactive approach to risk management, enhancing its ability to anticipate and mitigate risks in line with ISO 9001:2015 standards.
6. Process Management Module
The Process Management Module integrates and optimizes existing processes, ensuring they align with ISO 9001:2015 requirements. It provides a clear overview of process performance and areas for improvement. This module helped the firm streamline its processes, reduce inefficiencies, and maintain a high level of operational efficiency.
7. Performance Evaluation Module
The Performance Evaluation Module tracks key performance indicators (KPIs) and monitors progress towards quality objectives. It provides detailed reports and analytics to support continuous improvement. For the organization, this module enabled better performance monitoring, helping them make data-driven decisions to enhance their quality management system continuously.
The Bottom Line
The firm successfully transitioned to ISO 9001:2015, significantly improving its quality management processes and operational efficiency with Effivity's QMS software. They now enjoy enhanced document control, better risk management, and streamlined processes.
Want the same success? Contact the Effivity team today and schedule a consultation call.
Frequently Asked Questions
1. What are the key changes in ISO 9001:2015 compared to ISO 9001:2008?
ISO 9001:2015 introduces a greater emphasis on risk-based thinking, leadership involvement, and the context of the organization. It also has a more flexible structure, aligning better with other ISO standards. The updated standard focuses on performance and continuous improvement, making it more adaptable to various business environments.
2. Why is document control important in QMS certification?
Document control ensures that all documents are current, accurate, and accessible to authorized personnel. It prevents the use of outdated or incorrect information, which is crucial for maintaining compliance with ISO standards. Effective document control supports consistent operations and helps demonstrate adherence to quality management requirements during audits.
3. Can ISO 9001 compliance be achieved manually?
You can achieve ISO 9001 compliance manually, but it is challenging and time-consuming. Manual processes may result in errors, inconsistencies, and inefficiencies. Using QMS software like Effivity streamlines compliance by automating documentation, audits, training, and performance tracking, making the process more efficient and reliable.