Quality management is like a guiding light for businesses across the industries and regions. While specific requirements related to quality may vary across industries, standardized and generic requirements are covered under the ISO 9001 standard.
ISO 9001 framework gives organizations a structural approach to managing their quality and efficiency. This framework includes detailed documentation and organizational planning, which can be time-consuming.
Understanding the ISO 9001 quality management principles can simplify the process. This article explains the principles underpinning ISO 9001 requirements and how you can incorporate them into your organization using a QMS software.
Guiding Principles of the ISO 9001 Framework
ISO 9001 principles provide a foundation for effective quality management. These principles help organizations maintain high standards and continually improve. Let's look at what each of these principles entails.
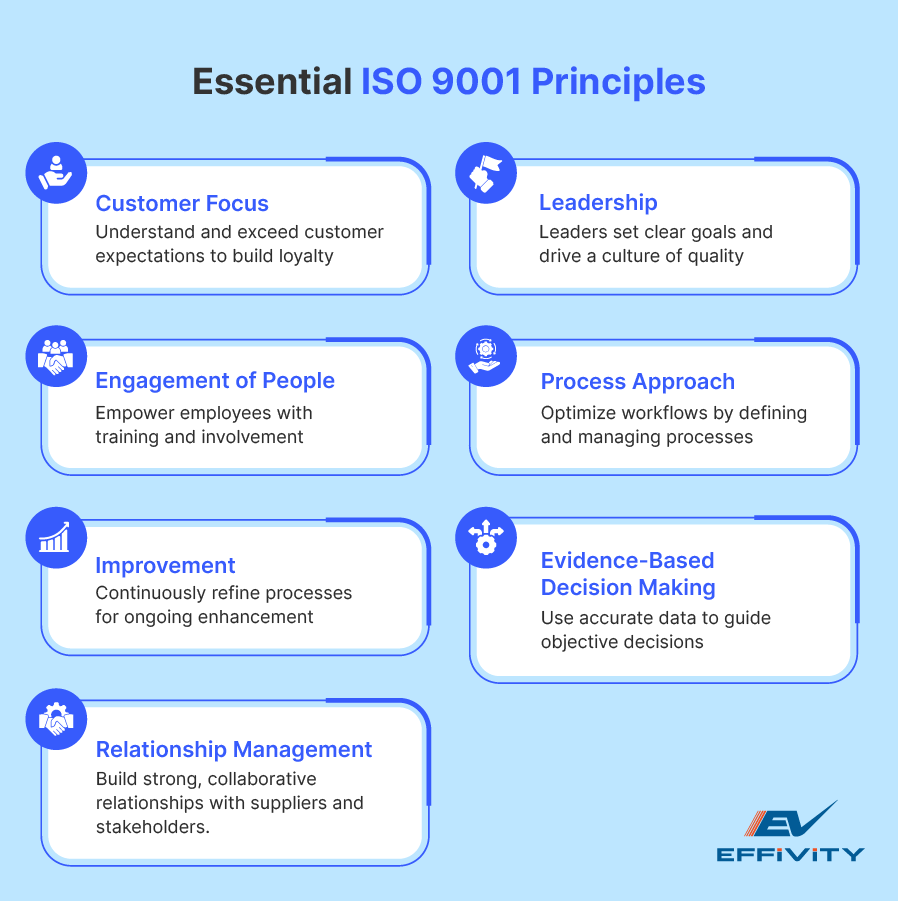
Principle 1: Customer Focus
Customer focus in 9001 emphasizes the importance of understanding and meeting customer needs. Your organization should strive to exceed customer expectations consistently. This focus helps in building long-term relationships and loyalty.
Customer-centricity involves every aspect of your business, from product development to service delivery. By prioritizing customer feedback, you can identify areas for improvement. This approach satisfies customers and enhances your market reputation.
Principle 2: Leadership
Leadership commitment is crucial for implementing ISO 9001 effectively. Your leaders must set clear objectives and motivate the team. This ensures everyone aligns with the organization's quality goals.
Top management involvement is vital for fostering a culture of quality. When leaders actively participate in quality management processes, it sets a positive example. This involvement drives accountability and continuous improvement throughout the organization.
Principle 3: Engagement of People
Empowering people means giving them the tools and training they need to succeed. When employees feel valued, they are more likely to contribute positively. This empowerment leads to better performance and higher morale.
Engaging employees at all levels fosters a collaborative environment. Your organization benefits when everyone is involved in decision-making processes. This engagement encourages innovation and a sense of ownership among employees.
Principle 4: Process Approach
A process approach to quality ensures that activities are well-defined and managed. By focusing on processes, you can identify inefficiencies and areas for improvement. This approach helps in achieving consistent results.
Process orientation involves understanding how different processes interact. By analyzing these interactions, you can optimize workflows and reduce errors. This leads to better resource utilization and enhanced productivity.
Implementing a process approach requires clear documentation and consistent monitoring. Establishing key performance indicators (KPIs) for each process allows you to measure effectiveness and make data-driven adjustments. With systematic planning, you can ensure that your organizational goals align with continuous improvement.
Principle 5: Improvement
Improvement is at the center of ISO 9001. Regularly evaluating and refining processes ensures ongoing enhancement. This focus on improvement helps your organization stay competitive.
Ongoing enhancement of processes requires a proactive approach. By identifying opportunities for growth, you can implement changes effectively. This ensures that your organization adapts to evolving market demands.
Creating a culture of continuous improvement involves engaging all employees in the process. Encourage your team to suggest ideas for enhancements and recognize their contributions. An inclusive approach leverages diverse perspectives and boosts overall morale.
Principle 6: Evidence-based Decision Making
Data-driven decision making in QMS involves using accurate data to guide actions. Reliable data helps in identifying trends and making informed choices. This approach minimizes risks and enhances outcomes.
Objective decisions are crucial for maintaining quality standards. By relying on data and analytics, you avoid biases and make fair assessments. This ensures that decisions are transparent and justifiable.
Effective evidence-based decision-making also involves continuous data collection and analysis. By consistently monitoring performance metrics, you can detect deviations and address them promptly. A proactive approach ensures that your organization remains agile and responsive to changes.
Principle 7: Relationship Management
Relationship management is crucial for the overall success and sustainability of any organization. Strong relationships with suppliers, partners, and stakeholders form the backbone of a reliable organization.
Supplier relationship management is essential for maintaining a consistent supply chain. Building strong relationships with suppliers ensures quality and reliability. This collaboration benefits both parties and leads to mutual growth.
Collaboration and communication with stakeholders to improve overall performance. By fostering open communication, you can address issues promptly. This approach builds trust and enhances cooperation.
How to Implement These Principles into QMS?
Quality management system (QMS) implementation requires a structured approach to ensure all principles are effectively integrated. By following these steps, you can build a robust QMS that aligns with ISO 9001 standards and drives continuous improvement.
1. Conduct a Gap Analysis
Evaluate your current processes against ISO 9001 requirements. Identify areas that need enhancement or development. This helps in creating a roadmap for QMS implementation.
2. Engage Leadership
Ensure top management commitment to the QMS. Leaders should communicate the necessity of quality and their expectations. Their involvement drives accountability and inspires the team to prioritize quality.
3. Train Employees
Provide well-rounded and comprehensive training to employees at all levels. Focus on the importance of quality management principles and their roles in the QMS. This empowerment leads to better engagement and performance.
4. Develop Documented Processes
Create clear, documented procedures for all key processes. Ensure these documents are accessible and understood by all relevant employees. Consistent documentation helps maintain standards and improve efficiency.
5. Monitor and Review
Regularly monitor the effectiveness of the QMS. Use data and feedback to identify areas for improvement. Schedule periodic reviews and audits to ensure ongoing compliance and continuous improvement.
Final Thoughts
Understanding and applying the principles underpinning ISO 9001 is essential for creating a robust quality management system (QMS). By focusing on customer needs, engaging leadership, empowering employees, and maintaining a process-oriented approach, your organization can achieve consistent quality and continuous improvement.
Implementing these principles can be streamlined with the use of QMS software. This software provides tools to document processes, track performance, and ensure compliance with ISO 9001 standards. By automating routine tasks and centralizing data, QMS software helps in maintaining accuracy and efficiency.
QMS software offers functionalities such as document control, audit management, and corrective action tracking. These features facilitate better process management, timely audits, and effective resolution of issues.
By integrating QMS software into your organization, you can simplify the implementation of ISO 9001 principles and drive continuous improvement.