For businesses seeking to improve their quality, health, safety, and environment implementation and management, relying on multiple solutions can be inefficient. When the different systems are isolated in an organisation, it often results in duplication of efforts, miscommunication, and inefficient processes, ultimately leading to conflicts and lower productivity.
However, integrated management system software is an excellent solution that can bring all your management systems working together towards a common goal. It is a digital solution designed to integrate all your ISO management processes, such as quality management, environmental management, food safety management, and more, within one system, improving coordination, productivity, and compliance.
With a single integration management system software in place, businesses can effectively automate their quality, health, safety, and environment processes and documentation, identify risks, and take necessary steps to address concerns and maintain regulatory compliance.
Let’s explore the benefits of integrated system software and how you can implement it in your organisation.
Benefits of Integrated Management System Software
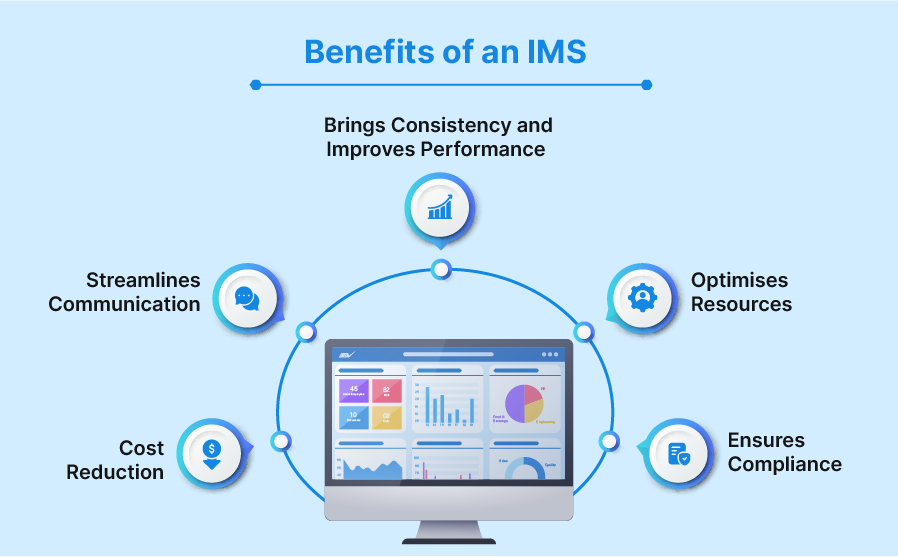
1. Brings Consistency and Improves Performance
An integration management system brings together the most common management systems of the organisation in one place. These could include
-
Quality management system:
A QMS system allows organisations to focus on consistently meeting industry quality standards to deliver high-quality products and services to its customers.
-
Environmental management system:
An EMS is a formal framework of processes and policies that helps organisations measure environmental performance and reduce its impact to maintain regulatory compliance.
-
Information security management system:
This software system allows organisations to monitor, manage, review, and improve their information security practices to keep sensitive data safe.
-
Occupational health and safety management system:
It offers a systematic approach to managing health and safety in a workplace to ensure a safe work environment.
-
Food safety and management system:
An FSMS is typically used in food industry businesses to manage, track, and improve their food safety practices.
With all the systems in one place, IMS software offers a holistic view of the organisation’s processes and establishes consistency. By integrating multiple management systems and standards, you can identify areas of improvement, track progress, manage documentation, and improve operational performance.
2. Streamlines Communication
By implementing an integration management system software, businesses can coordinate their efforts and facilitate cross-functional collaboration. An IMS eliminates departmental silos, so different functions and teams can collaborate towards a common goal. It helps you achieve a higher level of transparency in your communication and fosters a unified approach to problem-solving.
3. Optimises Resources
An IMS adds value to the organisation by optimising resources. When the systems work together, organisations can use their existing resources more efficiently to meet customer expectations and regulatory requirements.
Resources can be better utilised to focus on process implementation instead of multiple system maintenance, hence enhancing productivity in the organisation.
4. Cost Reduction
A single management system in the form of IMS software minimises the need for conducting multiple audits, handling tons of documentation, and managing certifications, which decreases your operational costs. It helps align multiple standards and their procedures, policies, and resources, which means you can even find common management system components.
For instance, you may be able to implement a single procedure for internal audits for quality control and environmental safety or integrate documentation for multiple standards. These similarities in processes can help you cut down on costs, time, and organisational resources.
5. Ensures Compliance
Organisations often need to follow various regulatory standards depending on their business and industry. An IMS brings together these standard requirements, typically including-
-
ISO 9001:2015: ISO 9001 is an internationally recognised standard for quality management systems. These standards include requirements for personnel, equipment, training, and services to help improve efficiency, reduce errors, and ensure quality standards are met consistently.
-
ISO 14001:2015: ISO 14001 pertains to environmental management systems that promote sustainability and environmental responsibility within organisations. It assists businesses in managing and reducing environmental impact.
-
ISO 45001:2018: This is a global standard for occupational health and safety that defines a framework for improving overall workplace safety and employee well-being and reducing workplace hazards.
By offering a centralised approach to maintaining regulatory standards, an IMS helps ensure and manage compliance. It automates processes, progress tracking, documentation, and reporting to make sure that business operations are aligned with the relevant industry standards.
How to Implement an Integration Management System?
Implementing an IMS in your organisation requires a systematic approach to ensure seamless integration and adoption with your existing processes.
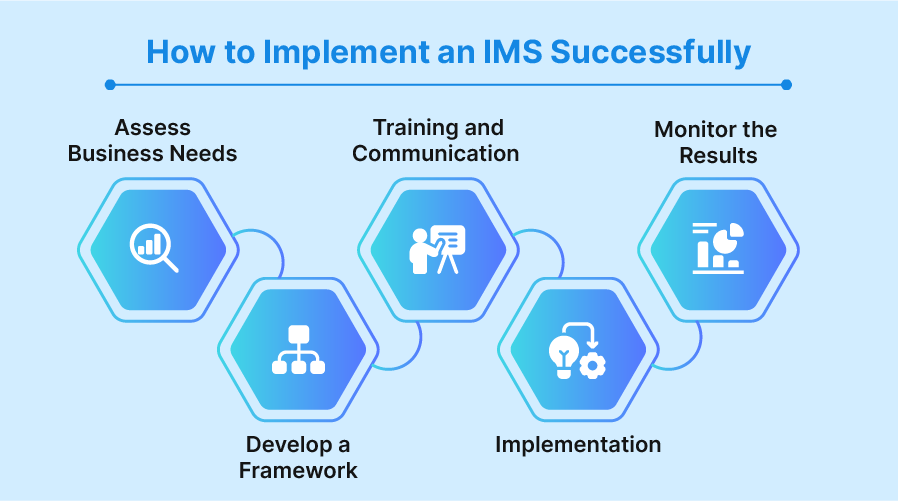
1. Assess Business Needs
Start by understanding the context of your business and assess the existing processes and management systems to identify any gaps within compliance practices. This will help you determine the areas for integration and the results you want to achieve.
2. Develop a Framework
It is important to develop a systematic framework that defines the various processes, policies, and documentation that will facilitate seamless implementation and communication in the organisation. Not to mention, it will align business goals and objectives with the management systems.
It is a good idea to assign a team to define and merge the various standard requirements, determine the need for resources, and oversee the implantation process.
3. Training and Communication
The success of implementing a QHSE-integrated management system relies on an effective training and communication program. It is important to communicate the features and benefits of an IMS with the employees, determine the specific roles and responsibilities, and train them on how to use the system effectively.
4. Implementation
Once the processes are in place and employee responsibilities are effectively communicated, it is time to go ahead with the implementation of the organisation’s operations.
5. Monitor the Results
Finally, it is equally critical to measure and review the results of the IMS to identify areas of improvement and update the processes so that the IMS system meets the requirements.
In the End
Integrated ISO management systems offer a comprehensive approach to planning, monitoring, implementing, and managing multiple management systems and regulatory requirements. By combining various processes, reporting, and documentation, businesses can achieve efficiency in their operations, reduce costs, and encourage continuous improvement.
Explore the features of Effivity’s integrated management system software to automate your business management processes. Schedule a demo today, or get in touch with us to know more.