Regardless of the industry, businesses constantly face risks. These might include manufacturing accidents or errors, inventory issues, customer service challenges, or scheduling conflicts. Such threats can lead to regulatory compliance issues, production disruptions, customer satisfaction declines and financial losses. This is where corrective action comes into play.
Corrective action plans can help your organization tackle any unexpected issues during business operations, ensuring that the same problems do not reoccur in the future. They involve thorough documentation, monitoring and tracking. In this article, we outline a corrective action plan and the steps you can take to ensure its success.
What is a Corrective Action Plan?
ISO 9001 says corrective action is any action taken to combat the cause and impacts of a problem to prevent its recurrence. Put simply, a corrective action plan (or CAP) refers to specific documentation outlining the steps required to address and rectify organizational problems. Its main aim is to improve and streamline processes, eliminate recurrent issues, improve product quality and customer satisfaction and ensure that the organization complies with regulatory standards.
CAPA’s often address problems such as recurring equipment failure, customer complaints, scheduling delays and more. By following the steps outlined in a well-designed corrective action plan, companies can strengthen their operations, create better products, improve employee performance and satisfaction and comply with regulatory compliance standards.
An example of corrective action is if an organization receives increased customer complaints caused by delayed shipments. They could make a plan to investigate what is causing the delay and identify what steps need to be taken to correct the issue. This could be through stricter quality and time control checks, employee training and better monitoring.
Why Are Corrective Action Plans Important?
When designed correctly, corrective action plans play significant roles in an organization's proper functioning and success. They resolve issues at the root level rather than simply addressing them at a surface level. A corrective action plan can:
- Mitigates recurring risks and other threats
- Provide precise details regarding problems
- Improve transparency to business operations
- Empower employees to take the necessary corrective measures
- Support ISO certification
How Can Corrective Action Plans Support ISO Certification?
Corrective action plan template allows companies to prevent mistakes and mitigate risk, which becomes crucial when dealing with ISO certification. The International Organization for Standardization is a federation of national standards bodies that outlines manufacturing standards for countless industries. When it comes to ISO certification, mistakes are called "non-conformities" and can be of two kinds: major and minor.
Minor non-conformities generally refer to smaller issues that can be resolved easily. Conversely, major non-conformities are problems that are more significant, difficult to rectify and sometimes systemic. If they are not handled efficiently, they can have severe consequences for the organization.
Corrective action plans are essential documentation in the quality management process. They are designed to address gaps in business operations. They ensure that both major and minor non-conformities are resolved, allowing the company to safely and effectively comply with ISO standards.
How Can You Make a Successful Corrective Action Plan?
To create a successful corrective action plan, organizations can take the following steps:
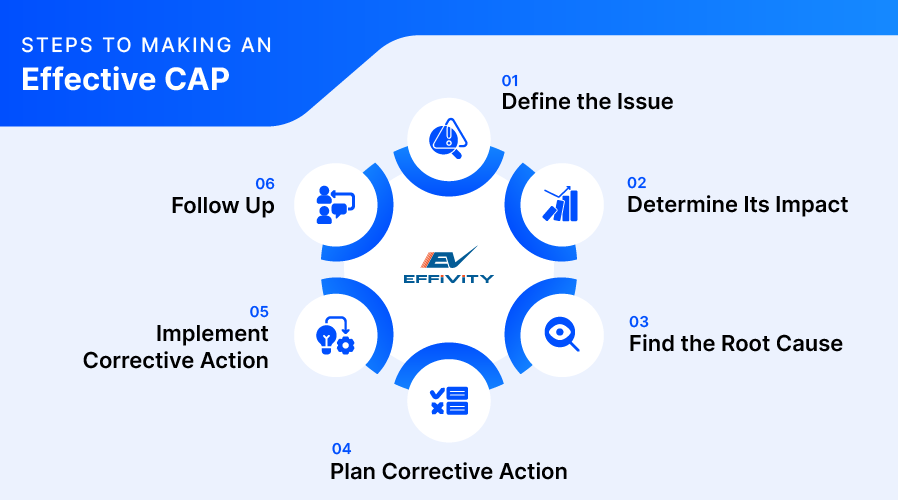
1. Identify and Define the Problem
The first step towards creating is to identify and define the problem. This can be done using several methods, such as internal audits, monitoring, incident investigation and data analysis. After the issue has been identified, it must be defined and documented.
This requires thorough research into all areas impacted by the problem, describing the who, when, what, where and why. There should also be a clear understanding of the outcome. For example, if an organization is facing issues because its inventory is backed up, some statements in its CAP could be, "We have only 600 steel parts" and "We should have 1000 steel parts."
2. Determine the Effect of the Problem
The next step is to determine how severe the issue is and its impact on your organization's operations. For example, if the problem affects the company's entire supply chain, then it is best to treat it as a priority. Conversely, if the problem occurs infrequently or does not have much of an impact on operations, it can still be dealt with but does not need to be a priority.
3. Find the Root Cause
The most important part of the process is getting to the root cause of the problem. Using the right techniques to dig deeper ensures you uncover the actual issue, not just the surface-level symptoms. Take the "5 Whys" method, for example—it's a simple but effective approach where you ask "why" five times to drill down to the real cause.
4. Plan the Corrective Actions to Address the Root Cause
After detecting and defining the issue and finding its root cause, the next step is to determine how to tackle it. One way of creating a successful CAP is to develop SMART goals (specific, measurable, realistic, time-bound) and a timeline. These steps should focus entirely on addressing the root cause of the problem, outlining every action needed to eliminate the underlying issue.
5. Implement the Corrective Action Plan
After outlining and creating the process, the next step is to carry out the CAP. This could be a simple software upgrade, replacing faulty machinery, or retraining employees. It could also involve more detailed steps. For example, if recurring product defects occur, the organization may need to halt its production, audit all of its machinery, recalibrate the faulty pieces, retrain staff and install more frequent quality checks.
6. Follow Up
Once a corrective action plan is started, it's crucial to monitor it closely. This includes regular follow-ups to ensure the implemented measures remain effective. After implementation, thorough documentation of the issue is equally important to maintain a clear record and support future improvements.
The Bottom Line
Corrective action plans (CAPs) are crucial to your organization's everyday operations. The right management system and software can ensure that you can create a well-designed and efficient CAP for any issues that may arise.
Effivity's QMS and CAPA management systems provide organizations with the tools to create successful CAPs. These include employee training modules, internal audit software and document control. To learn more, visit our website today!