Industries such as gas, oil, chemical manufacturing, and pharmaceuticals all require rigorous safety standards and efficient operations since they deal with hazardous and volatile materials. How do they accomplish this? This is where HAZOP comes in.
HAZOP can be seen as a sort of investigator—a set of tools that methodically uncovers any potential risks or operational non-compliance before they have the chance to grow into bigger problems.
HAZOP goes beyond just ticking safety boxes; it is a valuable system that allows companies to streamline their processes while ensuring that the environment, equipment, and people involved remain safe.
In this article, we will delve into HAZOP’s meaning, how it works, and why it is a must for any industry that prioritizes safety.
What is HAZOP?
Hazard and Operability Analysis, also known as HAZOP, is a systematic and strict technique for examining an organization’s structures and risk management. It is generally used to identify system-related hazards, operational challenges, and other problems that could lead to the production of products that do not comply with regulations.
It uses predetermined parameters and something called “guide words” that provide a list of deviation perspectives. This HAZOP technique is also used to help team members brainstorm potential deviations.
How Does a HAZOP Study Work?
A HAZOP study is a meticulous process. It involves teams of experts from multiple disciplines, such as operations, safety, process engineering, maintenance, etc. The key steps it follows include:
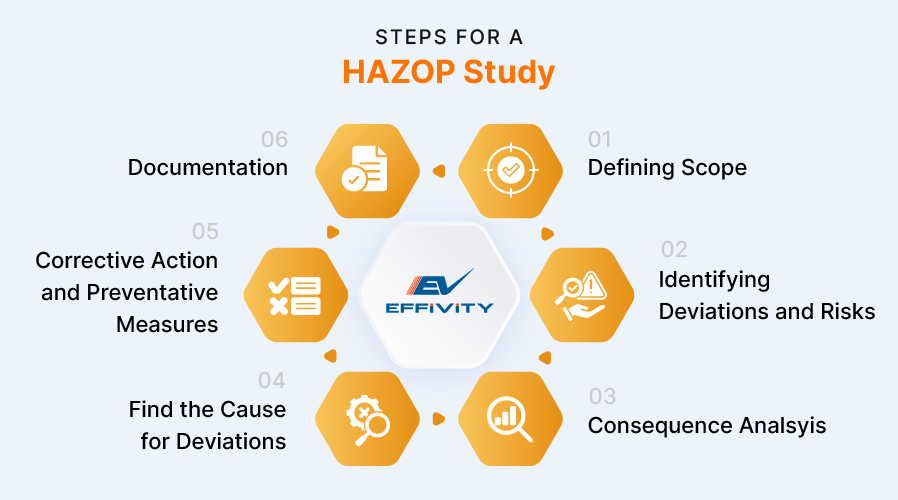
1. Defining Scope
The first step of a HAZOP analysis is defining the scope and objective it will cover, assembling a team, and determining the methodology for the study. This is also when your organization establishes which system or process needs to be examined, collects the relevant information, data, or documents, and creates a session schedule.
2. Identifying Deviations and Risks
Next, the HAZOP analysis studies the predetermined systems to look for any deviations from their intended design and functions. Analyze the process or system systematically and identify potential deviations from intended design parameters. Some variables could be temperature, pressure, or flow deviations. Teams may use guide words like “no,” “as well as,” “less,” more,” etc., to brainstorm thoughts and identify any risks.
3. Consequence Analysis
After analyzing any risks or deviations, the teams will have to determine the consequences these deviations may have on performance, operations, and safety. Depending on the industry, these could be of varying degrees of severity, such as fires, human errors, chemical releases, environmental impact, and damaged equipment. Team members will have to determine the severity of the consequences.
4. Find the Cause
Once deviations have been identified, they need to be resolved as well. This can be done by finding their underlying causes or any factors that may be leading to these problems. These could be flaws in the design, procedural errors, human error, damaged or faulty equipment, or more.
5. Corrective Action and Preventative Measures
After identifying the root cause and underlying factors, experts can plan the appropriate course of action to address the challenges or employ preventative measures to minimize the risk of potential hazards. Some examples of this include improving training, correcting design flaws, implementing new machinery, etc.
6. Documenting All Findings
A report should document the HAZOP study’s findings, processes, and recommended actions. These reports will be valuable reference points for future modifications, designs, business operations, and procedure changes.
Why is HAZOP Important?
OSHA’s Process Safety Management Standard (or PSM) recognizes HAZOP studies as a Process Hazard Analysis method. It identifies and controls possible risks before they can turn into major disasters.
This is especially vital in industries that deal with hazardous materials and processes, like the chemical, oil, gas, nuclear, or mining industries.
HAZOP helps organizations in the following ways:
- Identifying any risks or potential hazards in business operations
- Identifying past incidents that had the potential to have negative consequences
- Determining the consequences of any operations failures, such as health and safety risks
- Mitigating risks early on during the planning or design stages
- Investigating how organizations, their manufacturing/processing plants, or systems deviate from business goals and how this could affect personnel
What are Some Examples of Applications for HAZOP Study?
HAZOP studies are regularly used in various industries worldwide. These include oil, gas, chemicals, mining, and others that pose high safety and security risks. For example, HAZOP studies are primarily conducted in the oil and gas industry to analyze refineries, pipelines, and offshore facilities.
These studies can identify gaps in procedures, design, or equipment that could have significant consequences on the environment, human safety, or business procedures.
Chemical plants also use HAZOP studies to ensure that hazardous chemicals are handled safely and accidents are prevented. Similarly, pharmaceutical companies implement HAZOP analyses to catch any potential challenges or risks in the production process.
HAZID vs. HAZOP: What is the Difference?
HAZID vs HAZOP are often confused. While they are both used to identify and prevent hazards in business operations and procedures, there are significant differences between the two.
1. HAZOP
HAZOP involves an in-depth and rigorous review of established or newly designed processes. This systematic framework is used to uncover potential deviations from the design’s intent, find risks, and prevent issues.
2. HAZID
HAZID stands for Hazard Identification. This tool is used to identify potential hazards that could have disastrous consequences on people, equipment, or the environment in the early stages of a business’s project.
HAZID identifies and documents any sources of damage or injury that may occur in an area of operation, and can be used to plan and implement corrective measures to prevent disaster.
In Conclusion
The Hazard and Operability Analysis (HAZOP) is a key tool that organizations can implement to manage and mitigate risks while enhancing operational efficiency. HAZOP’s systematic and structured approach allows potentially dangerous industries to prevent major accidents, protect employees, and streamline operations. This tool is especially significant in a world where industrial errors can devastate human life, the environment, and an organization’s finances.
You need the right software to ensure your organization complies with health and safety standards. Effivity’s HSE Operations module helps you request, generate, and manage work permits, plan how to deal with emergencies, define and test plans on a regular basis, and more.
To learn more, visit Effivity’s website today!