Have you ever felt that your quality management system is holding your organization back? If you have felt this, you might still be using the older ISO 9001:2008 standard instead of the most recent version.
Adhering to an older ISO version when your competitors are quickly adapting to the ISO 9001:2015 version is like standing still when everyone moves forward without you. If you feel that your organization needs better alignment with current international business standards, it's time to make the switch.
If you are unsure where to start or still aren't fully convinced about why you should make this transition, read on for our complete guide on adapting ISO 9001:2015 and how this can be managed better with Quality Management Software.
Key Changes to the ISO Standard
The major changes that were made to ISO standard include:
Structure and Terminology:
The adoption of the Annex SL structure makes it easier to integrate with other management systems.
Risk-Based Thinking:
A proactive approach to identifying and addressing risks and opportunities.
Context of the Organization:
The new standard encourages understanding internal and external issues and the needs of interested parties within your organization.
Leadership and Commitment:
Increased involvement of top management in the QMS.
Documented Information:
More flexibility regarding documentation requirements.
Why Transition to ISO 9001:2015?
Let's try to understand why the move from the older to the newer version of ISO is even needed. Transitioning to ISO 9001:2015 has many benefits like:
1. The 2015 version emphasizes risk-based thinking, helping organizations proactively identify and mitigate potential issues.
2. It encourages top management to be more involved in the quality management system (QMS). This ensures better alignment with business strategy.
3. The updated standard promotes a more integrated process approach to help increase efficiency and effectiveness.
4. ISO 9001:2015 is designed to be more flexible, making it applicable to organizations of all sizes and industries.
ISO 9001:2008 to ISO 9001:2015: Step-by-Step
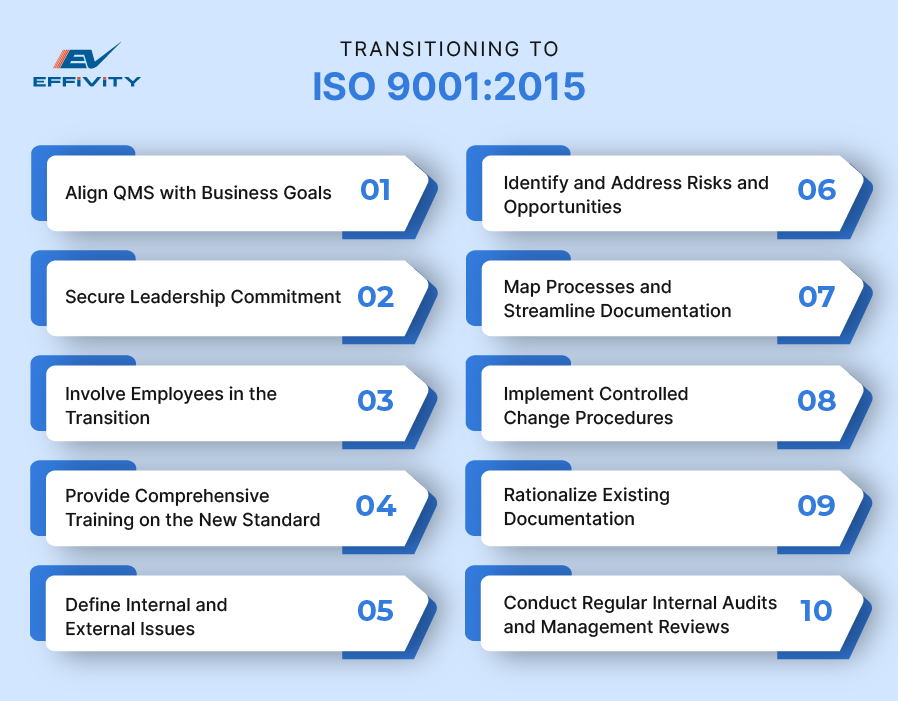
1. Define Strategic Alignment with Your Business and QMS
Begin by reviewing your organization's strategic direction and how the QMS supports it. This alignment ensures that quality objectives are integrated with business goals.
Understand your long-term vision and how quality management contributes. Ensure that quality policies and procedures support strategic objectives.
2. Engage Top Management
Leadership commitment is crucial for a successful transition. Present the benefits and requirements to top management. Clarify the role that your organization's leadership has to play within the new QMS context and how they have to support the transition.
Top management should establish a quality policy that reflects the organization's purpose and context and supports its strategic direction.
3. Ensure Employee Participation
Employee engagement is of utmost importance for the successful implementation of the QMS. Inform all employees about the transition, the reasons behind it, and how it will affect their roles. Include representatives from different departments in the planning process to gain diverse insights and foster ownership.
Establish channels for employees to provide suggestions and report issues related to quality. Implementing software solutions can ensure better communication within the organization.
4. Train Employees on ISO 9001:2015 Standard
Comprehensive training ensures that everyone understands the new requirements and how to apply them. Identify training needs for different roles and create a schedule that covers all necessary topics.
Combine classroom sessions, workshops, online courses, and practical exercises to cater to different learning styles. After training, evaluate employees to ensure they have understood the material and can apply it in their work.
Offer resources such as manuals, guidelines, and access to experts for continuous learning.
5. Define Internal and External Issues
Understanding your context of organization is a new requirement in ISO 9001:2015. Examine factors within the organization that can affect the QMS. This includes organizational culture, resource availability, and operational capabilities.
You can use tools like PESTLE (Political, Economic, Social, Technological, Legal, Environmental) analysis to identify external factors that could impact your QMS. Find out who has an interest in your QMS, such as customers, suppliers, regulators, and employees.
Keep records of the identified issues and interested parties, including their needs and expectations.
6. Identify Risks and Opportunities
Define how risks and opportunities will be identified, assessed, and addressed. Look at all aspects of your operations to find potential risks and opportunities. Then, evaluate the likelihood and impact of identified risks and prioritize them accordingly.
Develop strategies to reduce risks and seize opportunities, integrating these actions into your QMS processes.
7. Define Processes and Documentation
A process approach improves efficiency and consistency. You can visually map out all processes, showing inputs, outputs, resources, and interrelationships to determine which processes have the greatest impact on quality and customer satisfaction.
Develop standard operating procedures (SOPs) for critical processes to ensure consistency and decide which processes require documented information based on their complexity and importance.
8. Implement Controlled Change Management
Managing changes effectively prevents unintended consequences. Establish formal procedures for proposing, reviewing, approving, and implementing changes. Before implementing changes, analyze their potential effects on the QMS and operations.
9. Review and Rationalize Existing Documentation
Ensure that documentation is relevant, accurate, and adds value. Review all existing documents to identify duplicates, outdated information, or unnecessary complexity. Revise documents to reflect current processes and the new requirements of ISO 9001:2015. Then, implement controls to manage document creation, approval, distribution, and revision.
10. Carry Out Internal Audits and Management Reviews
Regular audits and reviews are essential for continuous improvement. Develop an audit schedule covering all processes over a defined period, ensuring objectivity and impartiality. Ensure auditors are competent and understand both the QMS and auditing techniques.
Evaluate processes against the requirements of ISO 9001:2015 and your organization's procedures and document non-conformities, observations, and opportunities for improvement. Address these audit findings promptly by identifying root causes and preventing recurrence.
Final Thoughts
When making a transition to ISO 9001:2015 do not forget the role of technology and how it can help you. A good QMS software solution can help you create automated systems that map and manage all processes efficiently. These software solutions act as centralized repositories for all your documentation and create a platform for better communication and collaboration.
Effivity's QMS Software solution allows for real-time monitoring and tracking of compliance and performance metrics. It is user-friendly and easily adaptable to various organization sizes and all industries.
Start your transition to the new ISO standard with Effivity. Visit our Effivity website for more information.