When your team feels safe and valued, it shows. When your employees feel secure and valued, you'll see a positive impact on their productivity and happiness at work. For this, you have to create a place where people feel respected, heard, empowered, and, most importantly, safe.
There are many different tools and guidelines available to help you achieve a safe workspace. OHSAS 18001 is one such framework that ensures your organization prioritizes a safe and healthy environment for your people.
To successfully adopt a standard like the OHSAS 18001, you need to follow a structured approach. That's where the Plan-Do-Check-Act (PDCA) framework comes in. The PDCA cycle helps you manage and improve your health and safety practices in a way that's organized and focused on continuous progress. The PDCA cycle makes sure your safety efforts are effective, evaluated often, and always getting better.
In this article, we'll dive into how the PDCA framework can streamline your implementation of OHSAS 18001 in your workplace. We'll also explore how the right Health and Safety Management Software can amplify your efforts.
What is the PDCA cycle
The Plan-Do-Check-Act cycle also called the PDCA cycle, is a management tool that your business can use to control and improve your processes and products. Implementing PDCA in workplace safety helps you create a well-defined approach to tackle all health and safety issues within your organization. The cycle encourages a systematic process for safety enhancement, allowing for constant reevaluation and optimization of practices.
Plan
Identify an opportunity and plan for change.
- Determine what you want to achieve, such as reducing workplace incidents.
- Assess current operations to identify areas for improvement in safety measures.
Do
Implement the changes on a smaller scale to test their effectiveness.
- Implement the safety solutions designed in the planning stage.
- Ensure all employees are trained on the new procedures.
Check
Use data to test the results of the modification and determine whether it made a difference.
- Compare the outcome with the expected objectives to gauge effectiveness.
- Obtain employee input on the changes and their impact on workplace safety.
Act
If the change is successful, implement it on a larger scale and continuously monitor your results. If the change does not work, begin the cycle again.
- Apply successful strategies on a broader scale within the organization.
- Based on learned experiences, plan new changes to continuously improve safety measures.
What is OHSAS 18001?
OHSAS 18001 is a regulatory standard for occupational health and safety management systems. It provides a structured plan for organizations to minimize workplace risks, improve safety performance, and demonstrate a commitment to employee well-being. Adhering to this standard can also assist with meeting legal and regulatory requirements. By adhering to OHSAS 18001, companies can establish an effective health & safety system that enhances employee well-being and organizational resilience.
How to Use PDCA for OHSAS 18001?
Implementing the PDCA cycle within the framework of OHSAS 18001 enhances safety management effectiveness. This iterative process aids your organizations in establishing, implementing, maintaining, and continually improving you Occupational Health and Safety Management System. By aligning PDCA with OHSAS 18001, companies can ensure systematic identification, assessment, and management of health and safety risks, adapting their strategies to legislative changes and organizational developments.
Best Practices for PDCA Cycle in OHSAS 18001
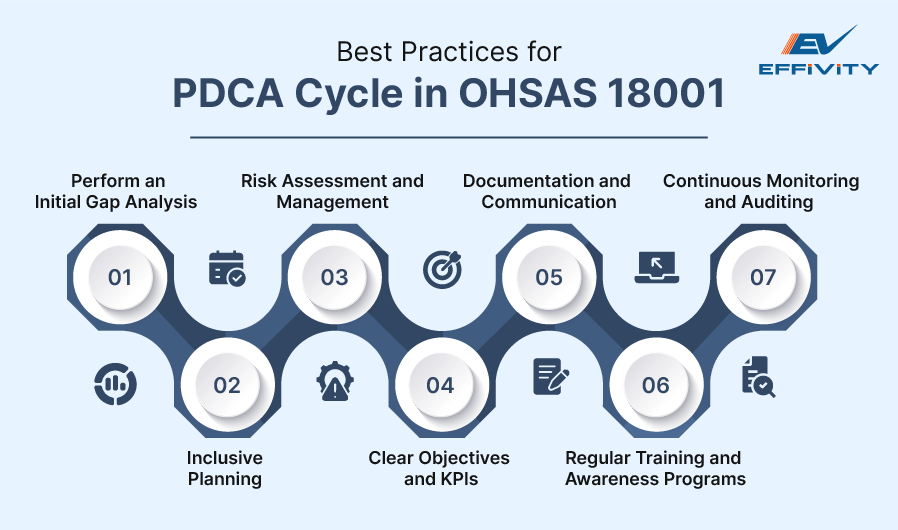
To maximize the effectiveness of the PDCA cycle in the context of OHSAS 18001, organizations should adhere to the following best practices:
- Before beginning the PDCA cycle, conduct a thorough gap analysis to compare current health and safety practices against the requirements of OHSAS 18001. This helps identify specific areas that need improvement.
- Engage a variety of stakeholders, including management and employees, during the planning phase. This collaboration ensures that the plans are comprehensive and practically applicable.
- In the planning phase, focus on comprehensive risk assessments to identify and evaluate occupational hazards. Implementing risk management strategies is crucial for reducing potential accidents and health issues.
- Set clear and actionable, measurable objectives and key performance indicators (KPIs) for every step of the PDCA cycle. This allows for precise monitoring and evaluation of safety performance against the set benchmarks.
- Maintain detailed documentation of all procedures, findings, and corrective measures. Effective communication across all hierarchies of the organization ensures everyone understands their roles within the system.
- Conduct frequent training sessions and awareness programs to inform employees about their roles in the OHSMS and updates to safety procedures.
- Continuously monitor implementation processes and conduct regular OHSAS 18001 audits and review processes to assess the effectiveness of safety measures and compliance with the standard.
Benefits of Using PDCA Cycle for OHSAS 18001
Adopting the PDCA cycle for OHSAS 18001 offers numerous benefits that contribute to the robustness of an organization's health and safety management:
- The PDCA cycle gives you a structured approach to managing safety, ensuring all aspects of workplace health and safety are continually reviewed and improved.
- Regularly revisiting each phase of the PDCA cycle helps your organization remain compliant with legal, statutory, and regulatory requirements
- Integrating risk management with PDCA and OHSAS 18001 allows for proactive identification and resolution of hazards, leading to a safer workplace environment.
- Employees working in a well-managed safety environment are more likely to be engaged, which would lead to higher productivity and retention rates.
- The iterative nature of the PDCA cycle fosters an environment of continuous improvement in OHSAS 18001, with each cycle building on the successes and learnings of the previous one.
The Bottom Line
By applying the PDCA cycle to OHSAS 18001, you'll gain a powerful system for elevating workplace safety and driving constant improvement. This structured approach of planning, implementing, measuring, and refining your safety practices will lead to greater effectiveness, stronger compliance, and reduced risk.
Additionally, integrating Health and Safety Management Software will take your efforts to the next level. These tools offer real-time monitoring, insightful data analysis, and streamlined reporting. This technological support makes your PDCA-driven safety efforts more efficient, consistent, and easier to track over time. The result is a safer workplace and a culture where proactive safety becomes the norm.