When you're managing a business, mistakes happen. A product might not meet quality specifications, a process might slip off-track, or a service could fall short of expectations. However, what separates a quality-driven organization from the rest is how it identifies, addresses, and prevents any mistakes from happening again.
And that's done with the help of a Non-Conformance Report (NCR).
NCR reports are essential to your quality control process, ensuring that every deviation from the standard is accurately identified, recorded, rectified, and transformed into an opportunity for growth.
If you're looking to achieve compliance with ISO 9001 standards, understanding the purpose, process, and NCR meaning can make a world of difference.
Let's break down everything you need to know about NCR's full form, how they work, and why they're game-changers for maintaining quality and compliance.
What is a Non-Conformance Report (NCR)?
A Non-Conformance Report is a formal document that records any deviation from agreed standards, procedures, or requirements in a product, service, or process.
In the context of ISO 9001, these reports play a critical role in identifying instances where products, processes, or systems fail to meet the criteria outlined in the QMS. A non-conformance management software can assist in creating and managing accurate NCR reports.
For example, if a batch of products doesn't meet the required specifications or if a process doesn't align with documented procedures, an NCR would be created to address the issue. This ensures accountability and helps the organization maintain its quality objectives.
Types of NCR Reports
Non-conformance reports can vary based on the nature of the issue and the processes involved.
1. Product Non-Conformance
This type of NCR report is issued when a product fails to meet established specifications or requirements. Product NCRs provide an extensive report of the nature of the defect, its location, severity, root cause, and so on to clearly understand and address the issue.
A product non-conformance could be
- A manufactured part with incorrect dimensions.
- A finished product that doesn't meet customer expectations.
2. Process Non-Conformance
Process-related NCRs arise when a procedure or workflow deviates from standard operating procedures (SOPs). This can occur due to:
- Failure to follow documented processes.
- Inadequate training or miscommunication.
The NCR helps identify the cause through various ways, such as process monitoring, performance metrics, or employee feedback.
3. System Non-Conformance
System non-conformities occur when the overall management system, policies, or practices fail to meet the requirements of ISO 9001 or internal policies. The causes of such non-conformity can stem from issues like ineffective quality management systems, cultural challenges in the organization, or inadequacy in compliance management processes.
Examples of system non-conformance include:
- Lack of proper documentation.
- Failure to conduct regular audits.
What is the Purpose of Using NCRs?
The major purpose of using NCR is to guarantee that the established standards for quality within the organization are met accurately and any deviations are reported promptly. Here's the purpose an NCR report serves for your business-
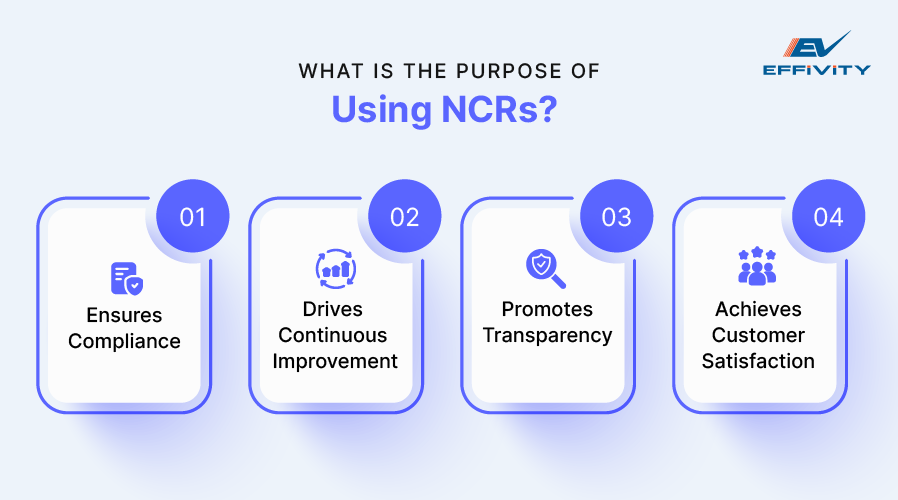
Ensures Compliance
ISO 9001 mandates a systematic approach to managing non-conformities. NCRs help organizations stay compliant with these standards, reducing the risk of audits revealing unresolved issues.
Drives Continuous Improvement
Each NCR provides valuable insights into areas that need improvement. You can analyze trends in non-conformance, understand the root causes, and implement accurate corrective actions to prevent recurring issues.
Promotes Transparency
Documenting non-conformities fosters a culture of transparency, where employees are encouraged to report issues without fear. This ensures problems are addressed promptly.
Achieves Customer Satisfaction
Resolving non-conformities helps maintain product or service quality, which leads to better customer satisfaction and loyalty.
The NCR Process
Managing non-conformities might seem daunting, but following a structured process makes it efficient and effective. Here's a step-by-step look at how NCRs are typically handled:
1. Identification
The NCR reporting process begins with identifying a non-conformance. This could be during routine inspections, audits, or as a result of customer feedback, depending on the nature of the non-conformance.
2. Documentation
Once the non-conformance is identified, it needs to be meticulously documented in an NCR report form, capturing details such as:
- Description of the non-conformance
- Date and location of occurrence
- Responsible parties
- Severity
- Reference to relevant procedures or standards
3. Root Cause Analysis
Following documentation, the root cause of the non-conformance is investigated. This is where the underlying causes behind the deviation are identified by analyzing factors such as manufacturing errors, material quality, design flaws, or lack of effective quality control.
The root cause analysis is crucial for developing strategies to address the non-conformance and prevent recurrence.
4. Corrective Action Plan
Based on the analysis, a corrective action plan is created to address the non-conformance. This includes steps to resolve the immediate issue and prevent it from recurring. Once these corrective actions are implemented, they must be monitored regularly to track the progress.
5. Verification
Finally, you must verify that the issue has been resolved and that the corrective actions are effective through regular internal audits, reviews, and updates in standard procedures. If not, alternative courses of action can be developed to address weak areas and avoid reoccurrence. Once verified, the NCR can be closed.
Key Benefits of Non-Conformance Reports
Non-conformance reports (NCRs) serve as a vital element in a successful ISO 9001 Quality Management System (QMS). Here's how-
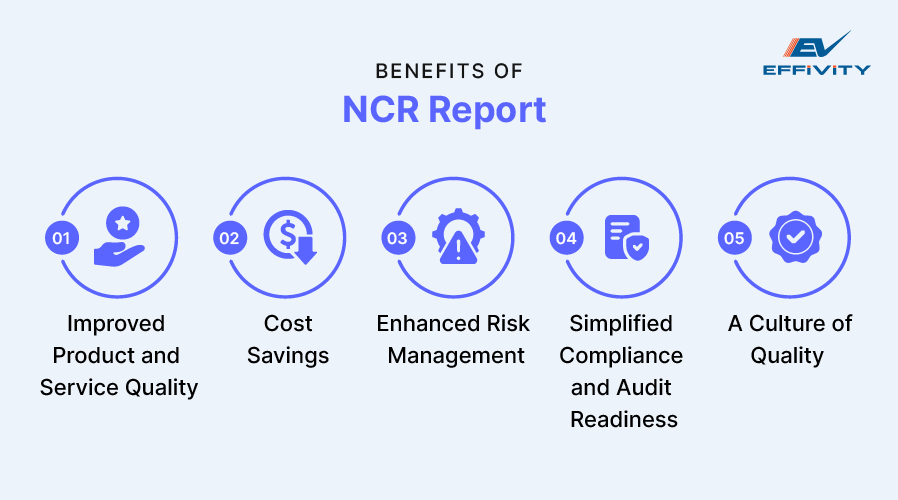
1. Improved Product and Service Quality
NCRs enhance product and service quality by identifying and addressing deviations from established standards. When a non-conformance occurs, organizations can investigate the root cause, implement corrective actions, and prevent the issue from recurring.
This systematic approach ensures that quality standards are upheld consistently, reducing the likelihood of defects and enhancing customer satisfaction.
2. Cost Savings
Unresolved quality issues can lead to financial losses due to rework, recalls, or wasted materials. NCR reports help organizations detect and address these problems early, avoiding costly consequences.
For instance, identifying and resolving a supplier issue before production begins can save significant costs associated with defective materials or components.
3. Enhanced Risk Management
A well-structured NCR process is essential for proactive risk management. NCR provides valuable insights into potential vulnerabilities within the system, allowing organizations to address them before they escalate.
This is particularly crucial for ISO 9001 compliance, where risk-based thinking is a fundamental requirement.
4. Simplified Compliance and Audit Readiness
For organizations adhering to ISO 9001, NCRs are an essential part of maintaining compliance. They provide documented evidence of how non-conformities are identified, resolved, and prevented. During audits, this documentation demonstrates a commitment to quality and continuous improvement.
Additionally, maintaining a clear trail of NCRs ensures the organization is always prepared for compliance checks, reducing the stress and effort associated with audits.
5. A Culture of Quality
Finally, NCR contributes to creating a culture where quality is prioritized at every level of the organization. By encouraging transparency and focusing on solutions rather than blame, NCRs empower employees to report issues confidently.
As a result, it ensures that quality becomes an integral part of daily operations, fostering a workplace where continuous improvement is the norm.
Final Thoughts
Non-conformance reports are a powerful tool for driving quality and fostering a culture of improvement. With a clear process and the right tools, managing NCRs can become an opportunity to enhance efficiency, reduce risks, and deliver better outcomes for your customers.
Effivity's quality management software is designed to simplify quality management within your organization, from creating non-conformance reports and risk management to conducting audits and addressing issues.
Effivity empowers your organization to meet ISO 9001 standards with confidence. Explore our website to know more.