Managing workplace hazards, evaluating risks, and implementing controls are foundational steps to ensure workplace safety. It's why organizations need to plan and implement a robust occupational health and safety management system to prioritize employee well-being.
However, implementing OHSMS in your organization is more than just about compliance; it's about creating proactive systems that protect lives and improve operational efficiency. At the same time, implementing an OHSAS management system can be confusing, especially when it comes to risk assessment, hazard identification, and defining controls.
This article dives into the processes behind identifying, managing, and mitigating workplace hazards and risks for ensuring occupational health and safety.
OHSAS Hazards
The OHSAS 18001:2017 describes hazards as any aspect or part of an organization's operations that can negatively impact the health or safety of its employees or visitors on the premises.
For instance, dangerous chemicals in your workplace can affect people's health, the moving parts of machines can injure operators, or ergonomic strain issues could affect employees who perform repetitive actions.
For any organization, it is important to manage these hazards by identifying them, assessing them, and implementing procedures and controls to minimize their effect, perhaps with a robust health and safety management system software.
Hazard management should always be pre-emptive and should identify and prioritize the applicable risks and controls. The complete process should also be fully documented.
Identifying Hazards
Here's how you can identify hazards within your workplace to create a safer work environment-
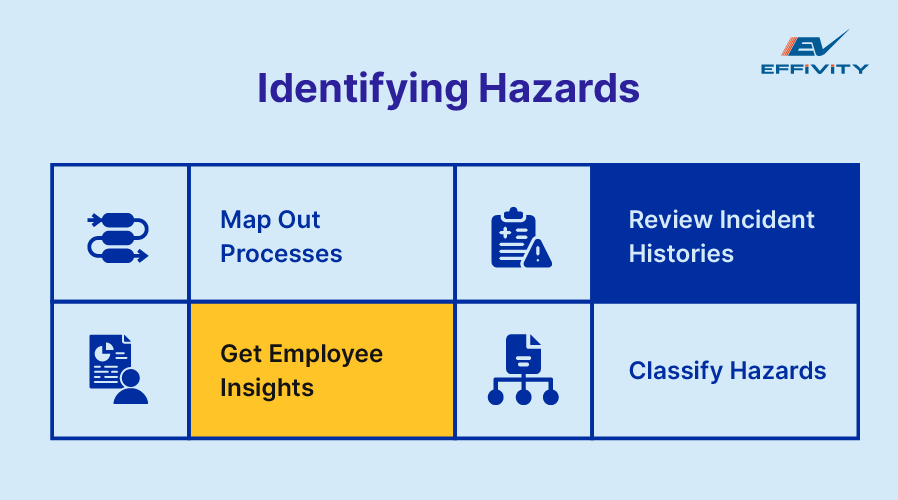
Map Out Processes:
Start by dissecting your operational workflows. Every process has unique inputs, outputs, and interactions that may harbor hidden hazards. For instance, in manufacturing, consider not just machinery but also energy sources, manual handling, and even the proximity of employees to moving parts. Identify the activities, both routine and non-routine, human capabilities and behavior, the organization's infrastructure and legal obligations, and materials and equipment used in the workplace.
Get Employee Insights:
Workers are the eyes and ears of your organization. Conduct safety dialogues or surveys to identify issues that may be overlooked by managers or auditors.
Review Incident Histories:
Your workplace's past incidents and near-misses are a goldmine of insight. Review past records and conduct periodic inspections to identify any new or recurring hazards.
Classify Hazards:
Not all hazards are created equal. Classification is key to effective prioritization and resource allocation. You can classify hazards based on their nature, impact, or severity.
OHSAS Risks
Once the hazards have been identified, the risk posed by these hazards needs to be assessed. The first step in risk assessment is to determine the likelihood of a hazard happening and assess the impact on the organization if the risk arises again.
The risk assessment is carried out to determine if the hazard will have a significant impact on your organization and whether you can manage it.
A risk is considered manageable and acceptable if it has been minimized to a level that the organization is comfortable with in terms of its OHSAS policy and its legal obligations.
One good example would be cutting yourself with paper in an office. Although the chance of it happening may be high, the severity of the injury will be low, and it will be deemed an acceptable risk with no controls required to mitigate it.
However, if a dangerous chemical is used every day, the probability of exposure to the chemical is also high, and the severity of the results will also be high. This can be classified as a risk that needs control to reduce the likelihood of it happening.
Effective Risk Assessment
Here are a few ways to assess OHSAS risks and controls within your organization-
Use a Risk Matrix:
The risk matrix ranks hazards based on severity and probability and helps you visualize priorities clearly. For instance, a high-severity, low-frequency hazard like a chemical spill might require specialized training but not round-the-clock monitoring.
Risk Clusters:
Some hazards often co-exist, such as poor lighting and increased trip hazards. Addressing these as clusters can yield quicker and more comprehensive solutions.
Behavioral Risk Analysis:
Understand how employee behaviors influence risks. Do workers consistently follow safety protocols, or are shortcuts common? Observing and addressing behavioral trends can prevent minor risks from snowballing.
OHSAS Controls
Once the risks are assessed, the OHSAS management system needs to implement controls that reduce risks presented by hazards.
The OHSAS standard requires that you can implement controls in a hierarchy in a way that you don't need to implement all. This means if the first control is implemented, the following ones are not required.
However, if the first control can not be used due to some reason, you can consider the next control, and so on.
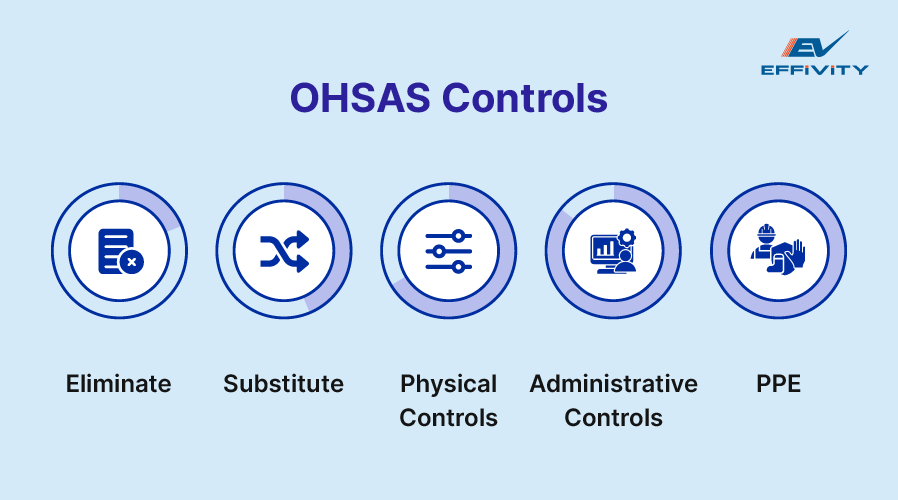
Eliminate:
The most effective controls remove hazards entirely. Can the hazard be eliminated from your process, e.g., don't use chemicals for a specific step?
Substitute:
Can your process use something less hazardous, e.g., can you achieve the same results with a less harsh chemical?
Physical Controls:
Can you prevent people from being exposed to the hazard, e.g., by putting barriers around moving machinery? This involves putting policies and procedures in place.
Administrative Controls:
Can you prevent people from being exposed to the hazard, e.g., by marking areas to keep people away from dangerous operations?
PPE:
PPE can be the last resort, not the default solution. Do your workers need to wear protective equipment like coats, goggles, or gloves when being exposed to the hazard?
Managing OHSAS hazards, risks, and controls requires a mix of vigilance, innovation, and collaboration. OHSAS 18001 gives your organization a framework to identify the hazards, assess the risks, and control them so that injuries or accidents do not happen.
After identifying hazards and risks within your organization, follow it up with a strong reporting mechanism that will allow workers to flag unsafe conditions or practices and conduct periodic inspections to ensure compliance and uncover new risks.