Production planning and control are common words in the world of business, with countless organizations ensuring they follow strict guidelines. But what exactly is it, and why does it matter? These two strategies work together in the manufacturing world to find the most efficient ways to produce goods.
The objectives of the production planning process include determining when to produce, how much to make, control techniques, and more. These methods ensure that your organization performs at its optimum capacity. In this article, we will explore production planning and control, why they are essential, and the steps involved in the process.
What is Production Planning and Control?
Production planning is the process by which manufacturing companies organize their production. It helps determine what, when, and how much to produce at a given time. Additionally, it establishes your organization's production capacity, identifies the raw materials needed, and creates a workable action plan. A well-crafted production plan can help organizations streamline operations, manage resources more efficiently, and quickly meet customer demands.
Production control goes hand-in-hand with production planning. Its functions involve monitoring production, measuring your organization's performance, and improving visibility and reporting. The process identifies areas where corrective action may be required and implements different control techniques to ensure streamlined and efficient production performance.
The Steps in Production Planning and Control
The process of production planning and control involves several key stages. These include:
1. Planning
Planning is the first stage in the process. It determines the production process's what, how, when, and where. It also involves describing the manufacturing operations in detail, determining the order of operations, the resources, and the equipment required. Time planning also involves deciding how much time different resources and machines will need to complete their tasks.
At this step, organizations must determine the materials, equipment, labor, and manufacturing techniques they will employ in their manufacturing process. This information must often be gathered and compiled from different sources. For example, the requirements for order quantity may be derived from sales data, whereas the materials and production requirements could be gathered from engineering and product development.
A thorough planning process can improve your organization's production, help meet demand, maintain quality, and avoid the waste of resources. Miscommunications during the production process are also minimized.
2. Loading and Routing
Put simply, routing is the stage where the 'route' raw materials will take from the beginning to the end of operations is determined. Loading determines the workload for each routing point, which is defined and managed. This phase is crucial for assigning tasks and checking the process's efficiency. This step of the production control and planning process also helps determine how raw materials will be moved through the various machinery and points of production.
This phase also helps to find the most appropriate sequence of operations, determine the machinery and personnel required to complete specific tasks and identify the resources needed at each phase of the production process. Success during this stage of the planning process can ensure that the necessary machinery is available and that bottlenecks do not occur at any stage.
3. Production
Following planning, routing, and loading, the production phase releases the orders for production. Also known as the dispatching phase, this process step ensures that all items employees require to complete their tasks are available. During this phase, organizations ensure that their raw materials are present at the appropriate workplace, that any necessary tools for specific operations are available, and that the process follows the plan and routing directions. All physical operations are carried out in this stage.
4. Follow-Up
After production and dispatching, the follow-up stage is a must. It involves checking for any bottlenecks, disruptions, or issues that could disturb the flow of production. This step helps organizations to understand the effectiveness of their planning and control measures. Also known as 'expediting,' it checks on the progress and efficiency of the production process. The performance of the production process, from planning to routing to carrying it out, can all be measured here. Any defects or gaps in the process can be identified and rectified.
5. Inspection and Correction
Production planning and control do not end once production is over. It is a continuous process that requires regular re-evaluation and correction to maximize efficiency. This can be achieved through regular internal and external audits and inspections to identify that all production activities meet quality standards. The results of these audits can be examined to identify problem areas and determine the proper corrective action. It helps to improve future production cycles.
The Benefits of Production Planning and Control
A successful and well-designed production planning and control process comes with a number of benefits. These include:
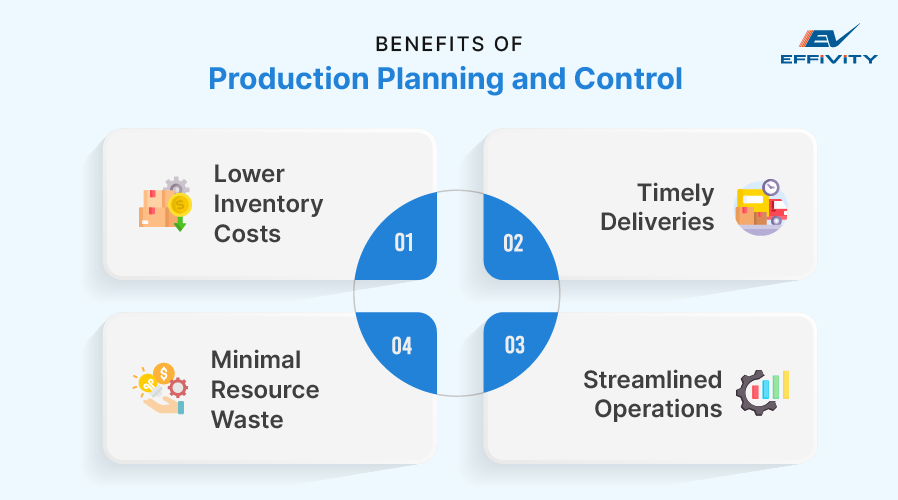
- Lower inventory costs: Manufacturers can identify and hold on only to the necessary inventory. Inventory surpluses can be avoided using the right scheduling software, reducing storage costs.
- Timely deliveries: The production planning and control process also helps to ensure that the manufacturing process is optimized and product deliveries are carried out promptly. This helps ensure customer satisfaction, improve customer retention, and improve loyalty.
- Streamlined operations: This process also ensures that the right materials and other resources are available when required and at what capacity they are available. This helps to ensure that the production line runs smoothly, improving employee satisfaction and minimizing interruptions in the workflow.
- Minimal resource waste: Waste is often a significant issue in manufacturing. A proper production planning and control system can eliminate material shortages or surpluses, ensuring reduced resource waste, including time and capital.
To Conclude
As we can see, production planning and control are some of the most important strategies to plan manufacturing operations. Production planning and control involves multiple departments, including marketing, procurement, sales, engineering, and more. Effective communication between these departments is a must.
It ensures that processes are carried out smoothly and promptly, resources are available when needed, and operations are streamlined and efficient. It also helps maintain production quality, improving customer satisfaction and loyalty.
The right management software can help your organization to streamline its operations and improve efficiency. Effivity's QMS software comes with quality inspection, management, and internal audit modules that are essential for manufacturing.
To learn more, visit Effivity's website today!