Implementing ISO 9001:2015 standards is one of the first steps organizations take towards creating a quality management system. However, it is unfortunate that a majority of organizations fail to successfully implement the changes dictated by these standards in the long run. If your organization faces similar challenges, know you aren't alone.
We must begin with a basic understanding that a quality management system is not a one-size-fits-all framework. It must be tailored to fit exactly what your organization needs at a specific time. It needs to address your challenges. You might be overwhelmed by documentation or struggling to get your team on board. Each challenge requires a unique solution.
In this article, we explore the twelve most common reasons why ISO standard implementation fails and provide detailed actions you can take to take your implementation from failure to a resounding success.
Top ISO 9001:2005 Standard Implementation Mistakes
Let's take a closer look at the issues that may arise when trying to implement ISO standards and the practice measures you can take to tackle these QMS implementation obstacles head-on.
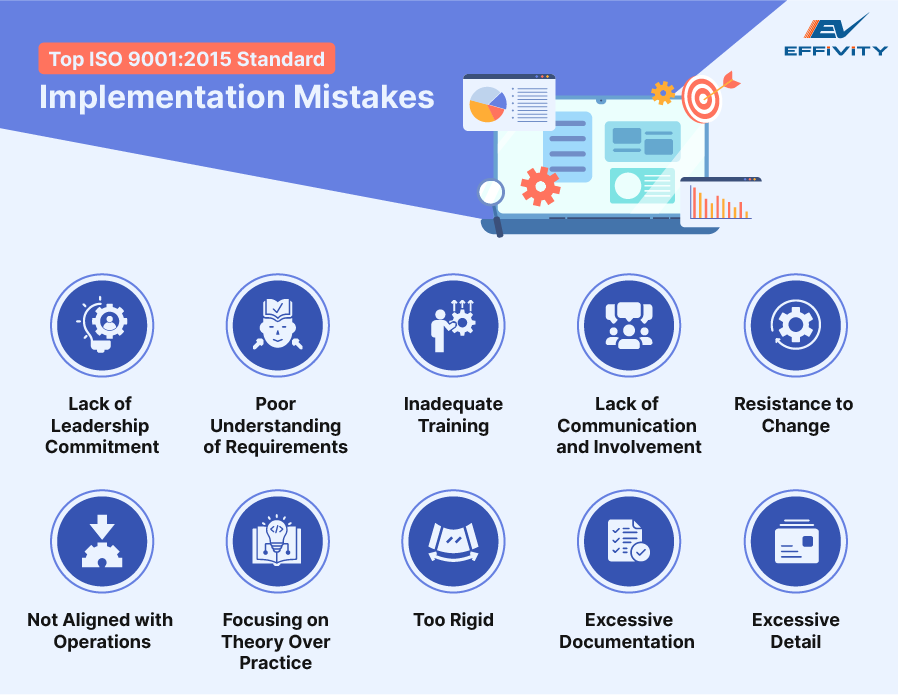
Lack of Leadership Commitment
When top management doesn't fully support the ISO 9001:2015 standard implementation , the process loses momentum. This leadership commitment in QMS often shows up as insufficient resources, unclear goals, and low employee engagement. Leaders might not see the value or might be too focused on short-term goals. Without their active involvement, the initiative struggles to succeed.
Corrective Actions
- Engage top management in the QMS process from the start
- Clearly communicate the benefits of ISO 9001 to leadership
- Allocate necessary resources, including time and budget
- Set clear, achievable goals for the QMS
- Regularly review progress with leadership involvement
Poor Understanding of Requirements
Misunderstanding ISO 9001:2015 requirements can lead to incorrect or incomplete implementation. This issue often arises when organizations don't invest enough time in understanding the standard. It results in non-conformity , wasted resources, and confusion among employees. Without a clear grasp of what the standard entails, the QMS cannot function effectively.
Corrective Actions
- Provide thorough training on ISO 9001 requirements
- Consult with experts or hire a consultant if needed
- Regularly review and discuss the requirements with your team
- Use clear, accessible resources to understand the standard
- Conduct internal audits to ensure compliance
Inadequate Training
Employees without proper training cannot effectively contribute to the ISO 9001:2015 standard implementation. This results in mistakes, low morale, and a poorly functioning QMS. Employee training for QMS is often neglected due to time constraints or budget issues. However, without adequate knowledge, employees cannot understand their roles or the standard's requirements.
Corrective Actions
- Provide comprehensive training for all employees involved
- Schedule regular training sessions to keep skills updated
- Use a mix of training methods, such as workshops and online courses
- Ensure training covers both the theory and practical application of ISO 9001
- Evaluate the effectiveness of training and make improvements as needed
Lack of Communication and Involvement
When communication is poor and employees are not involved in the ISO 9001:2015 standard implementation, the QMS suffers. Employees might see the QMS as irrelevant or burdensome, leading to minimal participation and low morale. This lack of engagement often stems from unclear roles, inadequate information, and limited feedback channels.
Corrective Actions
- Lucidly communicate the objectives and benefits of the QMS to all employees
- Involve the team in the planning process and implementation
- Regularly update staff on progress and changes
- Establish open channels for feedback and suggestions
- Recognize and reward employee contributions to the QMS
Resistance to Change
Employees often resist new procedures and changes introduced by the ISO 9001:2015 standard implementation. This resistance can manifest as reluctance to adopt new methods, low morale, and even active pushback. Causes include fear of the unknown, comfort with current systems in place, and lack of understanding of the benefits.
Corrective Actions
- Communicate the reasons for change and its benefits clearly
- Involve employees in the change management process to foster ownership
- Provide support and training to ease the transition
- Highlight quick wins to show the positive impact of changes
Not Aligned with Company Operations
A one-size-fits-all approach to ISO 9001:2015 standard implementation often fails because it doesn't fit the unique needs of the organization. When the QMS is not tailored to align with internal operations and overall strategy, it becomes ineffective and burdensome. This misalignment leads to confusion, inefficiencies, and lack of engagement from employees.
Corrective Actions
- Customize the QMS to reflect your company's specific processes and goals
- Engage primary stakeholders in the planning and implementation stages
- Ensure the QMS supports and enhances existing operations
- Regularly review and adjust the QMS to stay aligned with business objectives
- Gather feedback from employees to improve the system continuously
Focusing on Theory Over Practice
When organizations focus too much on the theory of ISO 9001 and not enough on practical application, the QMS becomes impractical and ineffective. This issue arises when teams strive for perfection in design without considering real-world usability. The result is a system that looks good on paper but fails to add value to daily operations.
Corrective Actions
- Prioritize practical implementation over theoretical perfection
- Test processes in real-world scenarios to ensure they work effectively
- Simplify procedures to make them user-friendly
- Continuously seek employee feedback to improve practicality
Too Rigid
A Quality Management System (QMS) that is too rigid cannot adapt to changing business needs and environments. This inflexibility results in a system that quickly becomes outdated and ineffective. A rigid QMS stifles innovation and makes it difficult to implement necessary improvements.
Corrective Actions
- Design the QMS with flexibility in mind to accommodate changes
- Regularly review and update processes to keep them relevant
- Encourage a culture of continuous improvement
- Involve employees in identifying areas that need adjustments
Excessive Documentation
Creating too much documentation can overwhelm employees and hinder the effectiveness of the QMS. This issue often results from a misconception that more documentation ensures better compliance. Instead, it leads to confusion, wasted time, and reduced focus on actual quality improvement.
Corrective Actions
- Streamline documentation control to include only essential information
- Focus on creating clear, concise, and accessible records to prevent QMS documentation issues
- Use documentation to support daily operations, not to complicate them
- Regularly review and update documents to keep them relevant
Excessive Detail
Including too much detail in QMS documentation can make it cumbersome and difficult to use. This often leads to confusion and slows down processes as employees struggle to find relevant information. The time and resources spent on overly detailed documentation do not add value to the system.
Corrective Actions
- Focus on necessary details that directly support QMS activities
- Ensure compliance with laws and regulations without overcomplicating documents
- Ask if each detail adds value before including it in the documentation
- Keep documents concise and user-friendly
- Regularly review and simplify documentation as needed
Understanding and addressing common challenges in ISO 9001:2015 standard implementation can significantly improve your chances of success. By prioritizing leadership commitment, proper training, effective communication, and practical application, you can create a QMS that truly enhances your operations. Implement these corrective actions through a quality management software to drive your organization towards success.