A comprehensive quality management system is the key to creating a culture of productivity, agility, and continuous improvement.
Product quality issues, delays, lower productivity, or decreased customer satisfaction – if this is what your company is dealing with, it's time to revisit the efficiency of your quality management system.
Effective quality management is the cornerstone of achieving product excellence for any business. It is a structured framework that helps a company direct, coordinate, manage, and record the processes needed to meet quality standards and comply with industry regulations.
Implementing a robust QMS that relies on modern technology, such as quality management software, not only improves productivity but also helps identify issues, reduce costs, ensure compliance, and achieve higher customer satisfaction.
However, the efficiency of your business processes will only be as good as the effectiveness of your quality management system processes. This article will explore 7 ways to improve your quality plan and ensure effective implementation of quality management systems.
What is a Quality Management System?
At its core, a quality management system is a formalised system of processes, procedures, and responsibilities aimed at maintaining product quality and safety, ensuring compliance, and improving customer satisfaction.
When it comes to an effective quality management system, ISO 9001:2015 "Quality Management System Requirement" is one of the most well-known approaches to achieving and maintaining quality standards. It is based on the seven quality management principles that help ensure a robust quality control improvement plan is in place.
7 Ways to Improve the Effectiveness of Quality Management System
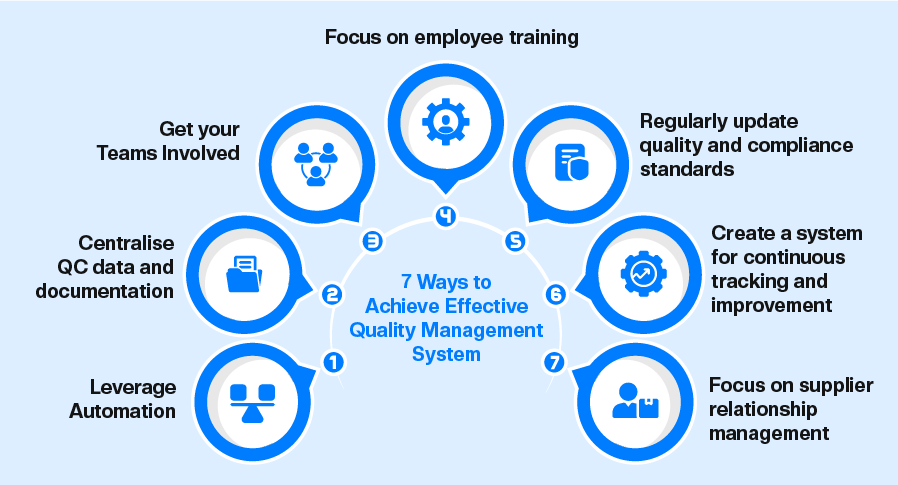
1. Utilise automation
One of the best ways to improve and streamline your quality systems is to implement quality control management software that automates the entire process. A paper-based QMS is not only inefficient and time-consuming, but it is also prone to human errors, requires frequent manual updates, and can be troublesome to maintain.
Instead, a digital solution will augment human efforts by automating reptitive tasks such as data entry and management, performance monitoring, maintaining documentation for improved audits, and so on. This way, organisations can free up time, minimise errors, and ensure a more centralised and integrated approach to quality management.
2. Centralise QC data and documentation
Today, most modern businesses have multiple products, departments, and stakeholders that generate tons of quality control data and documentation. Relying on manual and decentralised documentation management only leads to ineffective decision-making and chaos.
With the help of quality management software, businesses can bring all their quality control and management data to one transparent platform. This ensures that all the stakeholders can access the latest and accurate data to gain valuable insights.
When all the necessary data is available from a single source, it allows quality management teams to identify issues, plan for improvement, and achieve overall transparency within the organisation.
3. Get your teams involved
Effective quality management is never the responsibility of a single person or department. Rather, it is a collective effort where everyone in the company is committed to it.
Since quality is the backbone of every function, from product ideation and design to manufacturing, marketing, and customer service, companies must involve key leaders in the decision-making process.
In addition, establishing clear and open communication channels will ensure that different stakeholders understand their roles and responsibilities towards maintaining quality standards. Not to mention, a culture of feedback allows you to identify challenges to QC and foster a transparent and holistic approach to quality management.
4. Focus on employee training
Another aspect of an effective quality management system is a trained workforce. Regular training programs are essential to make employees aware of the quality standards and the need for better quality control and update them on the latest trends and technological advancements.
This helps ensure that the employees possess the relevant skills and knowledge to adhere to quality standards, internalise them, and foster a culture of commitment within the organisation. Creating a culture of employee training also involves recognising them for their contribution to processes and initiatives aimed at better quality control.
5. Regularly update quality and compliance standards
If you're looking to improve your quality management system , having standardised processes in place is a must. Having standard QC processes makes it much easier for various stakeholders, such as employees, managers, or suppliers, to monitor quality and ensure they meet the standards.
Besides, establishing key standards isn't enough. It is also important to regularly update the processes as per the industry standards to ensure the business is always on top of its quality management. For this, quality control management software comes updated with quality control best practices and regulatory standards to help you set up your QC workflows.
This ensures that stakeholders are always aware of the processes they have to follow to achieve better quality for the business.
6. Create a system for continuous tracking and improvement
Organisations must create a culture of analysis and improvement to stay ahead of the curve. This starts with establishing KPIs to provide measurable targets for QMS efficiency. By continuously evaluating your quality objectives and monitoring KPIs, businesses can effectively track performance, understand trends, and identify gaps against set quality objectives.
Routine audits and assessments using quality management software can help businesses understand that. With access to key quality data points through quality management software, organisations gain insights into trends, identify root causes of quality issues, and make data-driven decisions to boost the effectiveness of their QMS and improve their processes.
7. Focus on supplier relationship management
Suppliers are crucial in maintaining the quality of your products or services. Establishing strong relationships with suppliers based on mutual trust, transparency, and collaboration can go a long way in achieving quality excellence.
For this, organisations must define clear quality requirements and expectations, establish processes for vetting new suppliers, conduct regular supplier evaluations, and work together to address any quality-related issues promptly.
In Conclusion
The benefits of an effective quality management system are multi-fold – it helps businesses reduce costs, ensure regulatory compliance, improve efficiency and productivity, and achieve customer satisfaction.
As a result, it becomes imperative to continuously monitor and evaluate your quality management system processes to ensure they align with your quality objectives, foster a culture of improvement and commitment, and establish a centralised approach.