Planning to build a quality management system (QMS)? We’re sure the term “ISO 9001” has popped up more than once. It’s like they’re two peas in a pod.
But what does ISO 9001 stand for? What is it about and why do businesses consider it as the linchpin of a robust QMS?
If you’re struggling with these questions, look no further. In this blog, we’ll cover everything between the ISO 9001 certification full-form and its process.
By the end of it, you’ll gain a proper understanding of ISO 9001, its significance for building QMS, and the certification procedure.
What Is ISO?
Let’s start with the ISO full-form, which is “International Organization for Standardization.” It is a body of experts representing different national standards organizations worldwide.
Their goal is to create quality and safety guidelines for products, services, and processes so that businesses adopt a standardized (and right) way to do things.
ISO 9001: A Quick Overview
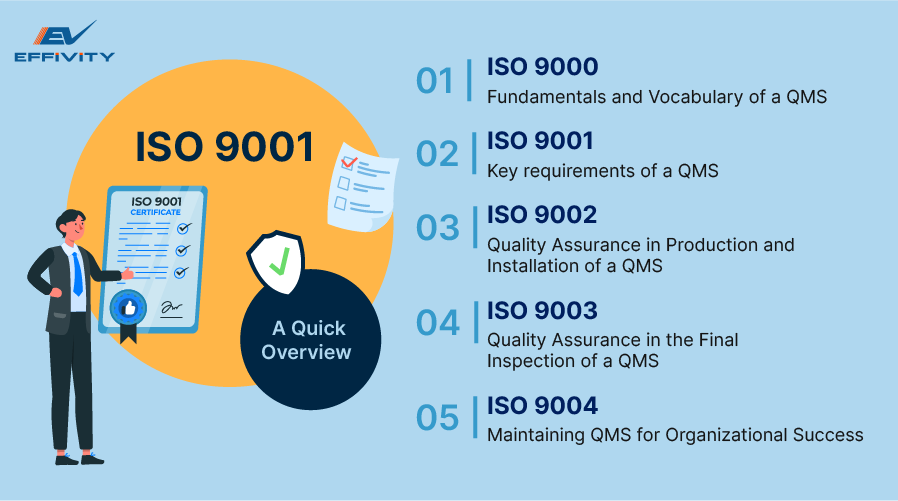
ISO 9001 is one of the many standards created and published by ISO. This particular one falls under the ISO 9000 series, which is a collection of 5 quality management standards:
- ISO 9000 - fundamentals and vocabulary of a QMS
- ISO 9001 - key requirements of a QMS
- ISO 9002 - quality assurance in production and installation of a QMS
- ISO 9003 - quality assurance in the final inspection of a QMS
- ISO 9004 - maintaining QMS for organizational success
ISO 9001 is the most sought-after quality management standard for organizations worldwide. It lays down the criteria or requirements for building an effective QMS to deliver quality and consistent products/services.
There are five versions of the ISO 9001 standard, with the latest revision made in 2015. Hence, the current standard is known as ISO 9001:2015.
What Does ISO 9001:2015 Cover?
ISO 9001:2015 includes 10 clauses. These are explained below in detail:
1. Scope
The first clause is introductory. It sheds light on the applicability of the ISO 9001:2015 standard.
2. Normative References
The second clause provides a list of references (other standards and publications) necessary to understand ISO 9001:2015.
3. Terms and Definitions
The third clause is a glossary of the common terms and concepts related to quality management systems.
4. Context of the Organization
The fourth clause explains how to define the context of your organization to understand the scope of the QMS correctly.
5.Leadership
The fifth clause emphasizes the role of leadership and top management's commitment to the entire process.
6. Planning
The sixth clause charts out a map for building QMS. For example, creating quality policy statements and objectives, identifying risks, etc
7. Support
The seventh clause addresses the essential resources for building a QMS—human resources, infrastructure, communication, quality management documentation, etc.
8. Operation
The eighth clause covers the planning and control of QMS-related processes. Product planning, design and development, and service provision are some of them.
9. Performance Evaluation
The ninth clause talks about monitoring the QMS through audit preparation, customer satisfaction, and management reviews.
10. Improvement
The final clause of ISO 9001:2015 explains the concept of continuous improvement—identifying opportunities for growth and taking corrective/preventive actions.
Benefits of ISO 9001 Certification
Why should organizations get their quality management systems certified? Let’s find out:
1. ISO Accreditation
ISO standards are internationally recognized, thus accounting for credibility in organizations with relevant ISO certifications, including 9001:2015.
2. Boosted Productivity
ISO 9001-certified QMS framework helps streamline processes,enhance risk management, and make evidence-based decisions, thus boosting an organization’s productivity.
3. Happy Customers
ISO 9001:2015 is customer-centric. A QMS aligned with such quality management principles delivers quality products/services. As a result, you can retain more customers, and easily attract potential buyers.
4. Compliance
ISO 9001 certification ensures your QMS is up to date with legal and industrial compliance standards.
ISO 9001 Certification Process Overview
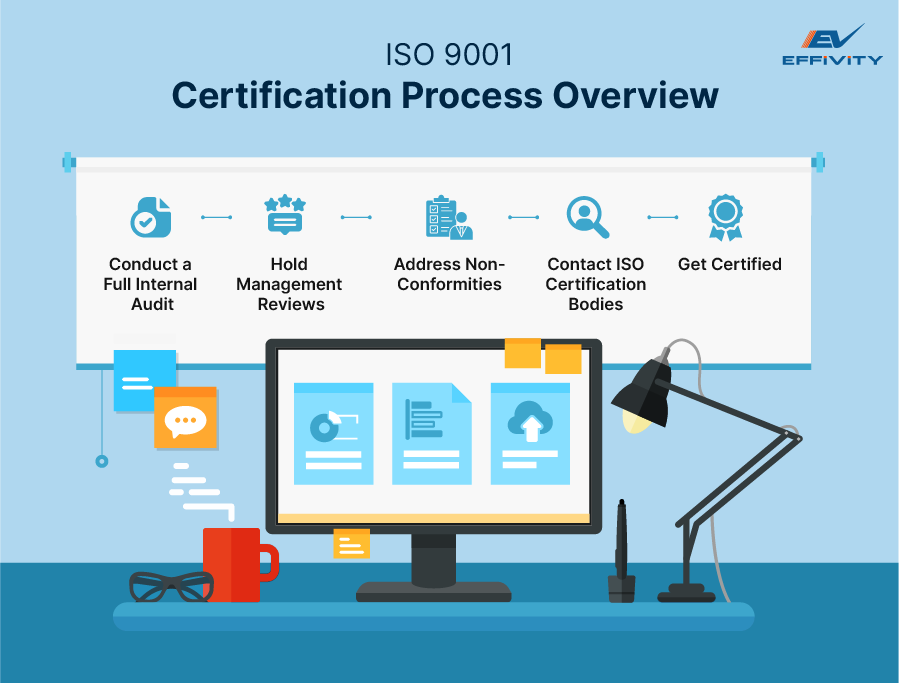
Wondering how to get your QMS ISO 9001:2015 certified? Check out the process below:
- Conduct a full internal audit to see where your QMS currently stands, and how it can improve.
- Management reviews are essential for evaluating the QMS processes, including decision-making, alignment with business objectives, conformance, communication, etc.
- Take the necessary corrective actions to improve the efficiency of your QMS.
- Reach out to ISO certification bodies to initiate the certification process. They will first check your documentation before running a full ISO audit on the QMS.
- That’s it! If your QMS follows all the certification requirements and ISO compliance guidelines, you’ll soon get the green light.
Set Up ISO 9001-certified QMS in Minutes!
Building a quality management system from scratch and getting it certified can be a pain in the neck.
Effivity brings a smarter way to approach quality management—a no-code cloud-based QMS software. All you need to do is choose from our ISO 9001 modules and select a pricing model to get the system up and running.
Our QMS software is user-friendly, automated, secure, and compliant. Start a 15-day free trial today to see the magic live!