In today’s fiercely competitive global landscape, businesses constantly try to improve their processes, grow and expand and provide better products and services to their customers. To successfully achieve your organizational goals, it is crucial to have some sort of framework and technique that allows you to collect data, identify errors and eliminate defects, all backed by solid statistics.
This is where Six Sigma enters. This statistical technique measures how far your processes deviate from the “perfect” level. Initially introduced in 1986 by Bill Smith, an engineer with Motorola, the method revolutionized quality management, with organizations like General Electric, Amazon and Toyota adopting it.
It has also been used in various industries, including finance, healthcare, manufacturing and service, helping companies worldwide reduce their costs, improve profits and enhance customer experience. This article looks at Six Sigma, the Six Sigma levels and how it differs from Lean Six Sigma.
What is Six Sigma?
Six Sigma refers to a set of techniques aimed at bettering business processes. Initially introduced in the 1980s by Motorola, the practice has become standard across several industries across the world. Practitioners often utilize financial analysis, statistics, project management and more to identify errors, reduce defects, minimize errors and improve efficiency and quality.
The Six Sigma model was created assuming that all business processes could be measured, streamlined and optimized. Initially used in the manufacturing industry for quality control. Since then, it has evolved to meet more general business standards, expanding beyond manufacturing to include
But what does Sigma mean? Initially derived from the bell curve used in statistics, “Sigma” denotes the standard deviation from the center. These deviations represent any problems in the organization, including failures of business processes, defective products and more. Therefore, a process with six of these is expected to achieve an exceptionally low rate of defects.
Six Sigma has now evolved to be a more general concept in business, focusing on meeting customer requirements, improving retention rates, enhancing process capability and more.
Steps Involved in Six Sigma
Six Sigma takes a step-by-step approach to identifying and improving process capabilities. According to practitioners, these steps can solve any problems an organization may face, including seemingly unsolvable ones. This 5-step process is termed DMAIC, where the letters stand for Define, Measure, Analyze, Improve and Control in that order. Here’s what each step entails:
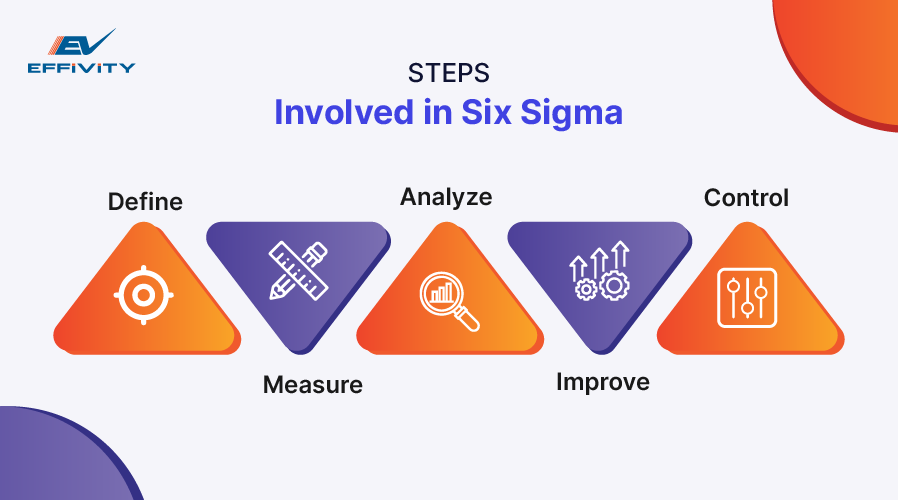
1. Define
In this stage, a Six Sigma expert and a team will identify and define a process or problem it wants to improve or solve.
2. Measure
After identifying and defining an issue, the team will measure the process’s performance. Then, they will create a goal or benchmark for the problem and compile a list of factors that may negatively affect performance.
3. Analyze
Next, each factor outlined in the above step must be analyzed and tested to determine if it is the root cause of the issue.
4. Improve
Once the factors contributing to failure have been identified, the next step is to make the necessary changes to improve performance.
5. Control
The last step involves placing controls to ensure that processes do not become ineffective again.
What The Sigma Levels Involve
Individuals can obtain different certification levels for Six Sigma. Process Sigma levels indicate an individual’s understanding of the Six Sigma process and how skilled they are at implementing it. Let’s take a look at what the Sigma levels mean.
1. Level One: White Belt
The White Belt encompasses the most basic Six Sigma level. Individuals in this tier have initial experience with the process but no formal training or certifications yet. They are qualified to be team members for the Six Sigma method but cannot lead a team.
2. Level 2: Yellow Belt
This is the lowest level of Six Sigma training an individual can attain. It involves multiple training sessions and provides participants with the knowledge to assist managers from more advanced tiers or even lead small teams.
3. Level 3: Green Belt
This tier requires a more comprehensive training course, which should equip participants to become leaders for more complicated projects.
4. Level 4: Black Belt
Black belt certification is the final and top-most tier level an individual can reach. This prepares them for leadership roles in more complex and large projects. They are considered to be “masters” or experts in the Six Sigma process, strong leaders and top-notch problem solvers.
Lean Vs. Six Sigma: What’s the Difference?
Another important method of enhancing business processes is Lean. Lean Six Sigma refers to a managerial approach that is more team-focused and aims to improve performance by eliminating waste and boosting work standardization.
It significantly differs from the traditional Six Sigma methodology, combining its tools with the lean enterprise philosophy. The lean manufacturing philosophy primarily aims to reduce waste by trimming down the time, effort, physical resources and talent used to complete a project while assuring high-quality standards. According to Lean methodology, any resources that do not create any value for the end customer are considered waste and eliminated.
To put it simply, Lean is a hybrid approach. In contrast to the traditional Six Sigma methodology, Lean combines quality, consistency and efficiency. Because of its commitment to efficiency, cost-effectiveness and higher quality, Lean has become the most widely used methodology in several industries, from governance to healthcare. It comes with countless benefits, including increased profits, lower costs, improved efficiency and better customer satisfaction and retention.
The Importance of Six Sigma
Implementing the Six Sigma methodologies means committing to operating in the pursuit of perfection. It comes with several benefits for business, including:
- Minimizing defects
- Reducing variations in the consistency of products and services
- Taking advantage of statistical analysis to uncover the root causes of problems
- Measure and analyze processes in detail
- Lead to significant savings by reducing errors
- Cultivating a culture of innovation and data-driven solutions
The Bottom Line
Six Sigma has evolved to become a valuable tool for business, bringing with it far-reaching impacts on the efficiency and success of an organization. Today, many Quality Management Systems utilize the Six Sigma method to maintain standards and foster an environment of continuous improvement.
A Quality Management System (QMS) can be a valuable tool if you want to enhance your business processes. Effivity’s QMS utilizes Total Quality Management, Continuous Quality Improvement, Lean Manufacturing, Six Sigma and Agile Quality Management to ensure that you have access to the best possible tools for quality management.
To learn more, visit Effivity's website today!