Quality, in essence, refers to how well a product or service meets customer expectations.
Quality management is the process of ensuring that every aspect of production or service delivery adheres to these high-quality standards.
A Quality Management System (QMS) formalizes this approach, documenting every process and responsibility to achieve quality objectives. It provides a structured approach to quality management.
In this guide, we’ll break down the essentials of QMS, including definition, core elements, benefits, and implementation. We’ll also discuss QMS software in detail.
Table of Content
- What Exactly Is a Quality Management System?
- 5 Key Methodologies That Are Used in a QMS
- 10 Core Elements of a Quality Management System
- 5 Most Important Benefits of Implementing a QMS
- A Detailed 5-Step Guide to Implementing a QMS
- Paper-based QMS vs Software-driven QMS
- 8 Reasons Why You Must Use QMS Software
- How to Choose QMS Software?
- 5 Signs That You Need to Transition to a Software-driven QMS
What Exactly Is a Quality Management System?
A quality management system is a comprehensive system within an organization that encompasses all activities and resources necessary to direct and control the quality of a product or a service.
This framework has a defined set of policies, procedures, and processes that guide how an organization operates to ensure consistent product or service quality.
Who Needs a QMS?
Any organization that desires to consistently deliver high-quality products or services can benefit from implementing a quality management system.
For small businesses, it provides structure and consistency. Larger enterprises can leverage a QMS to manage complex processes and regulatory demands effortlessly.
3 Industries That Benefit the Most from Implementing a QMS
Implementing a QMS brings significant advantages across various industries by ensuring consistent quality, regulatory compliance, and risk management.
Here are the top three industries that benefit from leveraging a quality management system:
1. Manufacturing
In manufacturing, a QMS enhances production efficiency, reduces waste, and ensures product consistency. It helps meet industry standards and regulations, minimizes defects, and boosts customer satisfaction.
2. Healthcare
Healthcare providers rely on quality management systems to improve patient safety and service quality. A QMS helps them comply with stringent healthcare regulations and manage risks such as medical errors. In addition to this, accurate documentation and process control contribute to better health outcomes.
3. Construction
The construction industry benefits from QMS by managing project complexities and ensuring compliance with quality standards. It standardizes processes, reduces risks like construction delays or defects, and enhances communication among project stakeholders.
What Are Some Common QMS Frameworks?
Below are some common frameworks that govern quality management systems in different contexts:
1. ISO 9001:2015
ISO 9001 is a universal standard for quality management systems. It focuses on enhancing customer satisfaction through continuous improvement and streamlined processes.
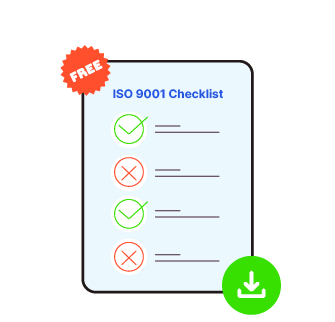
Break down every ISO 9001 compliance requirement and get certified faster with our free checklist
By clicking download, you agree to the Effivity Terms Of Use and Privacy Policy
2. ISO 13485
ISO 13485 emphasizes regulatory compliance and risk management tailored for medical device manufacturers so that medical devices meet necessary safety and performance criteria.
3. ISO 15189
Designed for medical laboratories, ISO 15189 ensures high standards in laboratory operations, from accurate diagnostics to reliable test results, directly impacting patient care and treatment efficacy.
4. ISO/TS 16949
ISO/TS 16949 integrates QMS principles to enhance product reliability and safety in the automotive sector. It mainly focuses on defect prevention and consistency in the automotive supply chain.
5. ICH Q10
Aimed at pharmaceutical companies, ICH Q10 provides a framework for maintaining consistent product quality throughout the drug lifecycle.
6. AS9011
AS9100 builds on ISO 9001, incorporating additional requirements to meet the rigorous safety and reliability standards essential in aerospace manufacturing.
5 Key Methodologies That Are Used in a QMS
Now, let’s look at five key methodologies used in quality management systems:
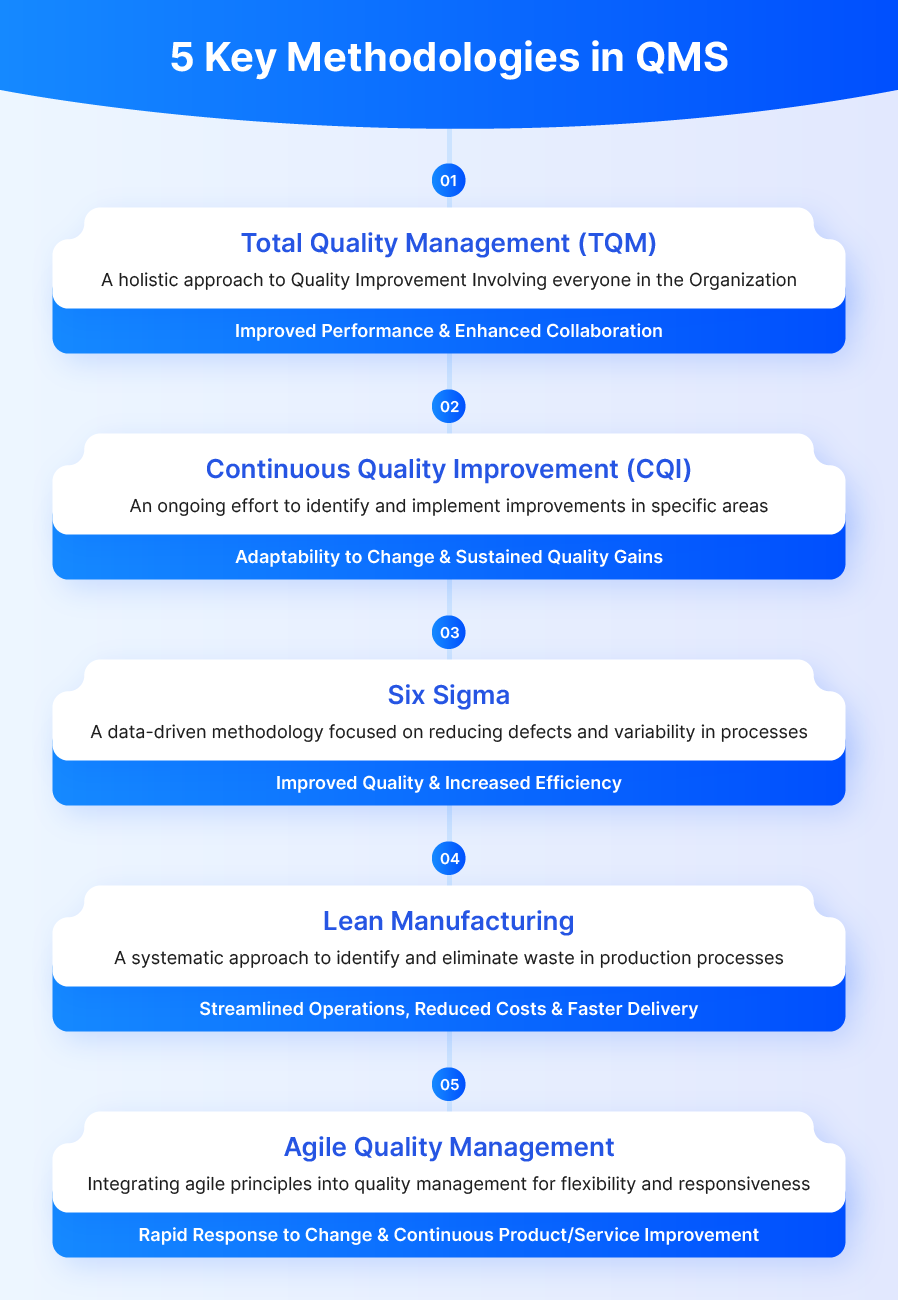
1. Total Quality Management (TQM)
Total Quality Management emphasizes the need for every individual within the organization to contribute to quality improvement—from top management to frontline workers.
The primary focus is on the customer’s needs. By doing so, TQM aims to enhance performance while also fostering a collaborative work environment.
Key principles include strong leadership, employee involvement, and data-driven decision-making.
2. Continuous Quality Improvement (CQI)
CQI is an ongoing effort to improve products, services, and processes. Unlike TQM, which involves the entire organization, CQI often targets specific areas for enhancement. It relies on iterative processes, using feedback and data analysis to identify and implement improvements.
The CQI approach is dynamic, thus allowing organizations to adapt quickly to changes and ensure sustained quality improvements.
3. Six Sigma
Six Sigma is a data-driven methodology aimed at reducing defects and variability in processes. By using statistical tools and techniques, Six Sigma identifies the root causes of errors and implements solutions to enhance process performance.
It follows a structured approach known as DMAIC (Define, Measure, Analyze, Improve, Control) to drive improvements.
Six Sigma’s focus on quality and efficiency makes it ideal for industries such as manufacturing, where precision and consistency are critical.
4. Lean Manufacturing
Lean Manufacturing focuses on reducing waste and increasing value in production processes. It identifies and eliminates non-value-added activities, thus streamlining operations and improving efficiency.
By optimizing resource use and enhancing process flow, lean manufacturing helps organizations deliver higher-quality products faster and at lower costs.
5. Agile Quality Management
Agile Quality Management integrates agile principles into quality management practices, emphasizing flexibility, collaboration, and customer feedback. It allows organizations to respond quickly to changes and continuously improve products and services.
This approach is particularly effective in IT and software development, where rapid innovation and responsiveness to customer needs are crucial.
10 Core Elements of a Quality Management System
Below, we delve into the 10 key components that form the foundation of an effective QMS:
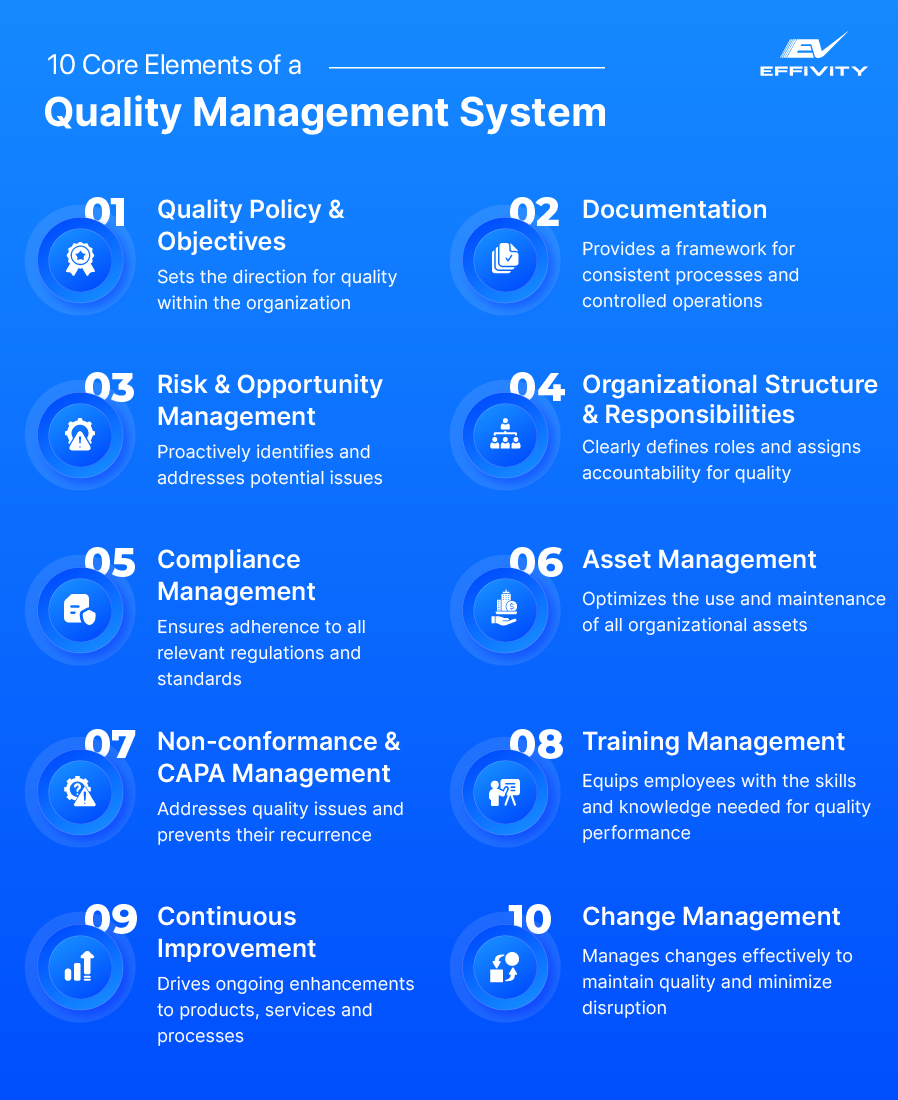
1. Quality Policy & Objective
The quality policy and objectives define the overarching goals and commitment to quality within an organization.
The policy sets the tone for a quality-driven culture, providing a framework for setting measurable objectives. It aligns with the company’s strategic direction, ensuring that all employees understand the importance of quality and work towards common goals.
2. Documentation
Proper documentation ensures consistency in processes, provides a reference for training, and also serves as a foundation for audits and inspections, offering evidence of adherence to established procedures.
Effective document control practices, including regular updates and secure storage, are essential to prevent discrepancies and maintain operational integrity.
3. Risk & Opportunity Management
Risk and opportunity management involves identifying, assessing, and mitigating potential risks that could impact quality, as well as leveraging opportunities for improvement.
This proactive approach helps organizations anticipate and address issues before they escalate, ensuring resilience and adaptability.
4. Organizational Structure and Responsibilities
A well-defined organizational structure clarifies roles, responsibilities, and authorities within the QMS. This element ensures that all employees understand their specific duties related to quality management and fosters accountability.
Establishing a quality management team or appointing a Quality Manager can further enhance oversight and ensure consistent implementation of QMS practices.
5. Compliance Management
Compliance management ensures that the organization adheres to relevant regulatory requirements, standards, and internal policies. Effective compliance management reduces the risk of legal penalties, enhances credibility, and supports continuous improvement by identifying areas for enhancement.
Regular audits and inspections are integral to this process, providing an objective assessment of the QMS’ effectiveness.
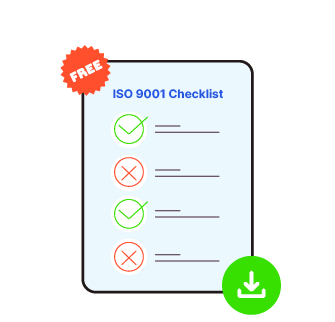
Break down every ISO 9001 compliance requirement and get certified faster with our free checklist
By clicking download, you agree to the Effivity Terms Of Use and Privacy Policy
6. Asset Management
Asset management involves the systematic process of developing, operating, maintaining, and disposing of assets in the most cost-effective manner. It ensures that all physical and intangible assets, such as machinery, technology, and intellectual property, are optimally utilized to maintain quality standards.
Regular maintenance schedules, tracking asset performance, and ensuring assets meet safety and quality requirements are all crucial to proper asset management.
7. Non-conformance and CAPA Management
Non-conformance management addresses instances where processes or products fail to meet specific standards. This element involves identifying, documenting, and analyzing non-conformities to determine their root causes.
Corrective and Preventive Actions (CAPA) are then implemented to rectify the immediate issue and prevent recurrence.
8. Training Management
Training management is crucial for ensuring that all employees possess the necessary skills and knowledge to contribute to quality objectives. It includes identifying training needs, developing training programs, and tracking their effectiveness.
A well-implemented training management system supports competency development, reduces errors, and enhances overall process efficiency.
9. Continuous Improvement
Continuous improvement focuses on consistently enhancing processes, products, and services. This means regularly reviewing performance, identifying areas for improvement, and implementing changes to drive better results.
Tools such as Plan-Do-Check-Act (PDCA) cycles and Lean methodologies are often employed to facilitate their process.
10. Change Management
Change management within a QMS ensures that any changes to processes, systems, or products are implemented in a controlled and systematic manner. It involves assessing the impact of proposed changes, obtaining necessary approvals, and effectively communicating changes to all stakeholders.
When executed correctly, this element helps minimize disruptions, maintain quality standards during traditions, and support the organization's adaptability to new challenges and opportunities.
5 Most Important Benefits of Implementing a QMS
A quality management system brings a host of benefits that extend beyond just maintaining quality standards. Let’s explore them one by one:
1. Standardization
By defining clear procedures and work instructions, a QMS helps maintain uniformity across different departments and locations. It ensures that processes are consistent and predictable, reducing variability and errors. This leads to improved product quality and service delivery, as every task is performed according to established standards.
Standardization also simplifies training and onboarding, as employees have a clear understanding of their roles and responsibilities.
2. Compliance
A QMS provides a framework for identifying applicable regulations, implementing necessary controls, and maintaining documentation to demonstrate compliance. This systematic approach helps organizations avoid legal penalties, prepare for external audits, and build trust with stakeholders.
Regular internal audits and reviews, a core element of every QMS, play a key role in ensuring continuous compliance.
3. Customer Satisfaction
Customer satisfaction is at the heart of any successful business.
A quality management system focuses on understanding customer needs, delivering products and services that meet or exceed expectations, and addressing any issues promptly. Plus, by implementing feedback mechanisms, a QMS ensures continuous improvement in customer experience.
Most importantly, consistent quality facilitated by a QMS helps build a strong brand reputation, thus attracting new customers and retaining existing ones.
4. Greater Accountability
Quality management systems foster a culture of accountability by clearly defining roles, responsibilities, and expectations for all employees. It establishes a transparent system for tracking performance and holding individuals accountable for their actions.
This clarity empowers employees to take ownership of their work, which leads to higher engagement and productivity.
5. Competitive Advantage
In today’s competitive market, having a robust QMS can be a significant differentiator. It enables organizations to consistently deliver high-quality products and services, which can be a key factor in winning and retaining customers.
A QMS also supports innovation by providing a structured approach to process improvement and risk management. Additionally, achieving certifications like ISO 9001 can enhance an organization’s credibility and open up new business opportunities in global markets.
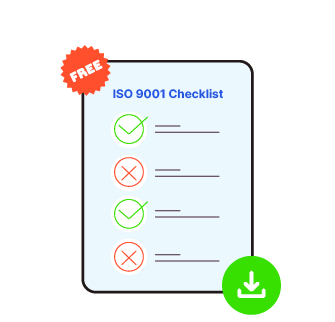
Break down every ISO 9001 compliance requirement and get certified faster with our free checklist
By clicking download, you agree to the Effivity Terms Of Use and Privacy Policy
A Detailed 5-Step Guide to Implementing a QMS
Implementing a quality management system is a strategic process. Each step plays a critical role in ensuring that the QMS is effective, sustainable, and aligned with the organization’s goals.
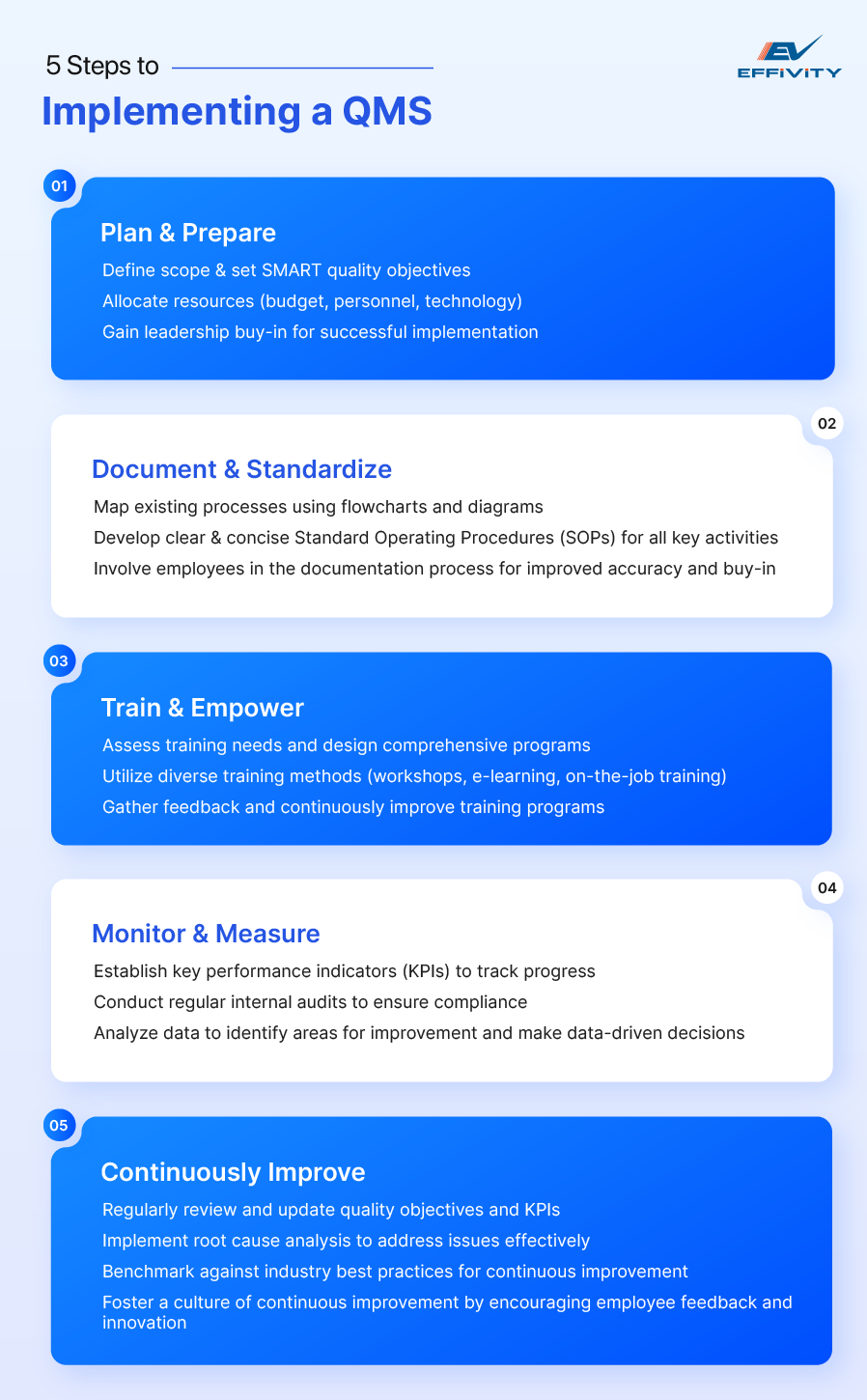
1. Planning the QMS
Begin by defining the scope of your quality management system. This entails identifying the specific processes, products, and services encompassed by the system, while simultaneously determining the specific needs of your organization and stakeholders.
Next, establish clear and concise quality objectives that directly support your overall business goals. These objectives should be SMART: Specific, Measurable, Achievable, Relevant, and Time-bound. For example, instead of a general goal like “improve customer satisfaction,” aim for a concrete target like “reduce customer complaints by 20% within the next 12 months.”
Resource allocation is another critical factor in QMS implementation. This involves identifying and securing the necessary personnel, technology, and financial resources.
It’s best to create a dedicated quality team or appoint a QMS manager to oversee the process. Developing a detailed timeline with key milestones is also essential.
Finally, engage leadership and secure their commitment. A successful QMS requires top-down support, and leaders set the tone and prioritize quality throughout the organization.
2. Documenting Processes and Procedures
Effective process documentation starts by conducting a thorough examination of each step within your workflow, from the initial customer inquiry to final product delivery. Utilize flowcharts, diagrams, or written descriptions to capture these processes comprehensively.
Once you have a clear understanding of your processes, it’s time to standardize them by developing detailed procedures. These should outline the specific steps, responsibilities, and criteria for each task. For example, a procedure for handling customer complaints might detail how complaints are logged, investigated, and resolved, including timelines and communication protocols.
It’s important to involve employees who are directly engaged in these processes during documentation. Their firsthand knowledge ensures accuracy and helps build buy-in.
Additionally, use simple, clear language to make the documents accessible to everyone, avoiding technical jargon that could create confusion.
3. Training the Team
First, assess the current skill levels and knowledge gaps within your team. This assessment will help you tailor the training programs to meet specific needs.
Next, develop a comprehensive training plan that includes both initial and ongoing training sessions. Initial training should cover the basics of the QMS, including its objectives, benefits, and how it applies to each team member’s role.
You can use a mix of training methods to cater to different learning styles. These could include workshops, e-learning modules, on-the-job training, and interactive sessions. Encourage active participation and provide opportunities for hands-on practice to reinforce learning.
In addition to this, you must create a feedback mechanism to gauge the effectiveness of the training. Regularly solicit feedback from participants to identify areas for improvement and adjust the training content accordingly.
Lastly, document all training activities, including attendance records and evaluation results. This documentation serves as evidence of compliance and can be useful during audits or reviews.
4. Monitoring and Measuring Performance
Once the QMS is implemented, the next critical step is monitoring and measuring its performance.
This mainly involves identifying key performance indicators (KPIs) that align with your quality objectives. For example, defect rates, customer satisfaction scores, and on-time delivery rates. Analyzing this data helps you identify trends and root causes of issues, enabling you to take proactive measures.
Besides clearly defined KPIs, you must also conduct regular reviews and audits to ensure the QMS remains effective. Internal audits allow you to assess compliance with established procedures and identify any discrepancies or non-conformities. You must use audit findings to make informed decisions about necessary adjustments or corrective actions.
It’s important to involve employees in the monitoring process. Encourage them to report issues and suggest improvements. This not only enhances their engagement but also fosters a culture of continuous improvement.
Also, regularly communicate performance results to the team, highlighting successes and areas for improvement.
5. Continually Improving the QMS
To cultivate a culture of continuous improvement, you must:
- Regularly evaluate your quality objectives and KPIs: As your organization evolves, so too should your quality goals. Periodic management reviews can help assess and enhance the effectiveness of the QMS.
- Use tools such as root cause analysis and corrective action plans: When a problem arises, investigate thoroughly to understand the underlying causes and implement solutions that address these root causes rather than just the symptoms.
- Adopt best practices from industry standards: Stay updated with the latest developments in quality management. Benchmarking against industry leaders can provide valuable insights into areas where your QMS can improve.
- Foster a culture that encourages innovation and feedback: Encourage employees at all levels to contribute ideas for improvement. Recognize and reward their efforts to motivate ongoing participation.
Paper-based QMS vs Software-driven QMS
A quality management system is a framework of policies, procedures, and documents that serve as a basis for quality management within an organization.
QMS software, on the other hand, is an automated approach that facilitates quality management. It comes with pre-built modules to perform all the necessary quality management activities more smartly and efficiently.
Here’s what essentially differentiates a QMS from a QMS software:
Aspect | QMS | QMS Software |
---|---|---|
Type | Framework | Software Application |
Components | Quality policy, objectives, manual, organizational structure and responsibilities, etc. | Features for risk management, reporting, tracking KPIs, etc. |
Goal | Establishing quality management standards | Executing and improving quality management |
Implementation | Manual | Automated |
Ownership | Managed by the organization | Provided by vendor through licensing or subscription |
Maintenance | Determined by the growing needs of the organization | Vendor-supported updates |
8 Reasons Why You Must Use QMS Software
A quality management system software goes beyond simply automating processes. It revolutionizes how organizations manage quality by introducing efficiency, consistency, and scalability.
Let’s understand how:
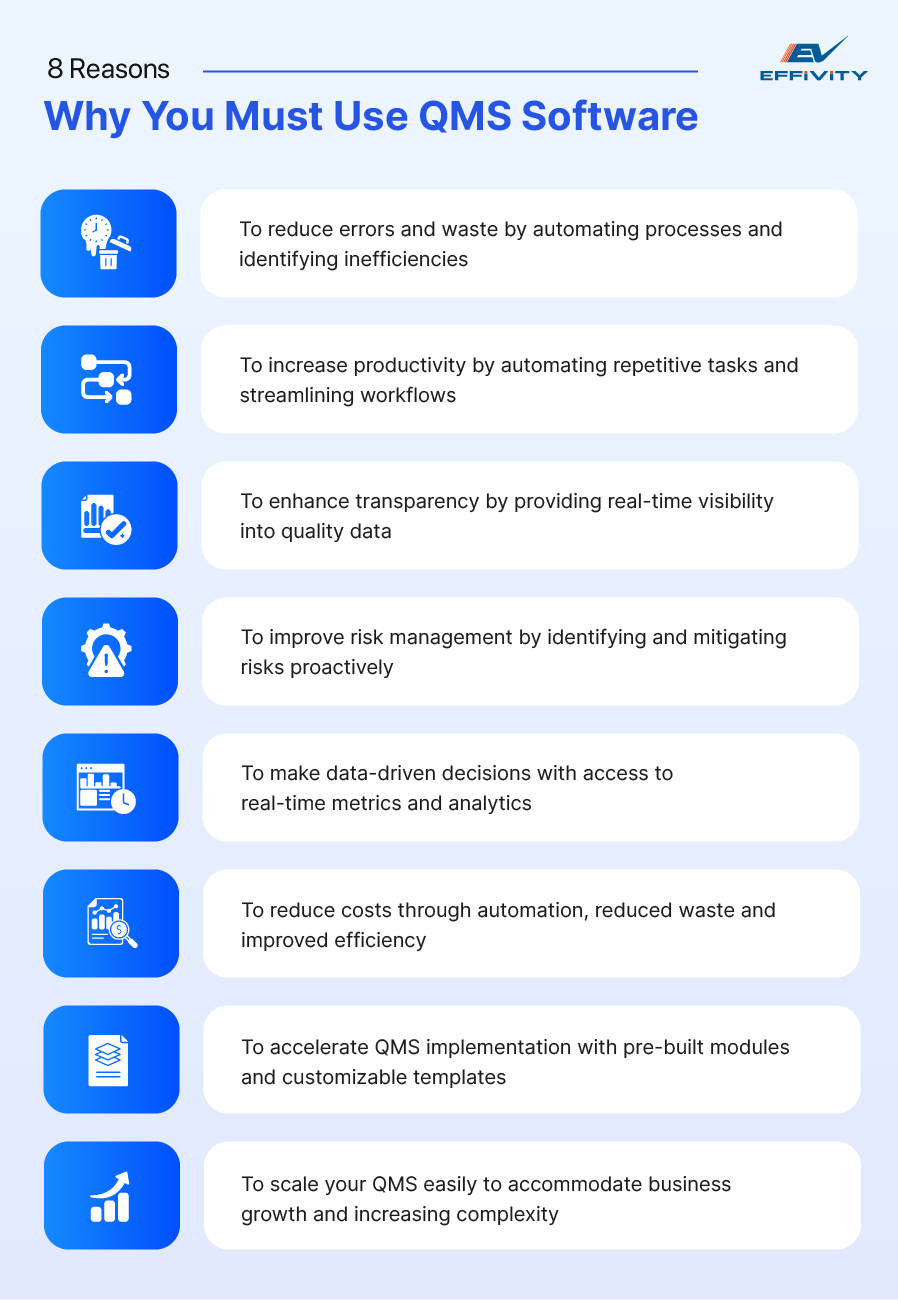
1. Reduced Error and Waste
QMS software significantly reduces errors and waste by automating key processes, thus minimizing human intervention. For example, automated document control prevents the use of outdated procedures, while automated data entry reduces manual input errors.
Additionally, real-time tracking of quality metrics helps identify inefficiencies and areas of waste promptly, allowing organizations to implement corrective actions swiftly.
2. Increased Productivity
By automating repetitive tasks such as data collection, reporting, and compliance monitoring, QMS software frees up time so that employees can focus on more strategic activities. Features like automated notifications and reminders ensure that tasks are completed on time, reducing bottlenecks and delays.
Furthermore, centralized data management allows quick access to necessary information, facilitating faster decision-making and smoother collaboration among teams.
3. Transparency
Automated quality management fosters greater transparency by providing a centralized platform for all quality-related data and activities.
It offers real-time visibility into processes, performance metrics, and compliance statuses. Detailed audit trails and comprehensive reporting ensure that all actions are recorded and traceable, promoting accountability.
This level of transparency not only builds trust within the organization but also enhances stakeholder confidence, as everyone has access to clear, accurate information.
4. Enhanced Risk Management
Risk management becomes more effective with QMS software due to its advanced capabilities in identifying, assessing, and mitigating risks. It allows organizations to conduct thorough risk assessments, automatically identify non-conformities, and trigger corrective actions to prevent risks from escalating.
Additionally, predictive analytics and real-time monitoring help anticipate risks before they become problems, ensuring proactive management.
5. Evidence-based Decision Making
A QMS software provides comprehensive dashboards and analytics so that the management can access key performance indicators, quality metrics, and audit trails instantly. This data-driven approach enables informed decisions based on tangible evidence rather than guesswork or assumptions.
6. Cost Savings
In QMS software, cost efficiency is achieved through several avenues:
- Automation reduces the need for manual labor, minimizing labor costs and the risk of costly errors.
- Improved process control and waste reduction contribute to material savings.
- The software streamlines compliance management, reducing the costs associated with audits, regulatory fines, and corrective actions.
The long-term savings from increased operational efficiency and reduced reward further amplify the return on investment.
7. Faster Implementation
QMS software accelerates the implementation of quality management practices by providing pre-built modules and templates that are easily customizable.
Unlike traditional manual systems, which require extensive time to develop and document processes, software solutions come with ready-to-use frameworks that can be tailored to an organization’s specific needs.
8. Scalability and Growth
As a business grows, its processes and quality management needs become more complex. Most QMS software solutions are designed to accommodate this growth by integrating new modules, expanding functionality, and adapting to increased data volume.
How to Choose QMS Software?
Selecting the right QMS software is a critical decision that can significantly impact your organization’s quality management success. Here are some things to consider before making the decision:
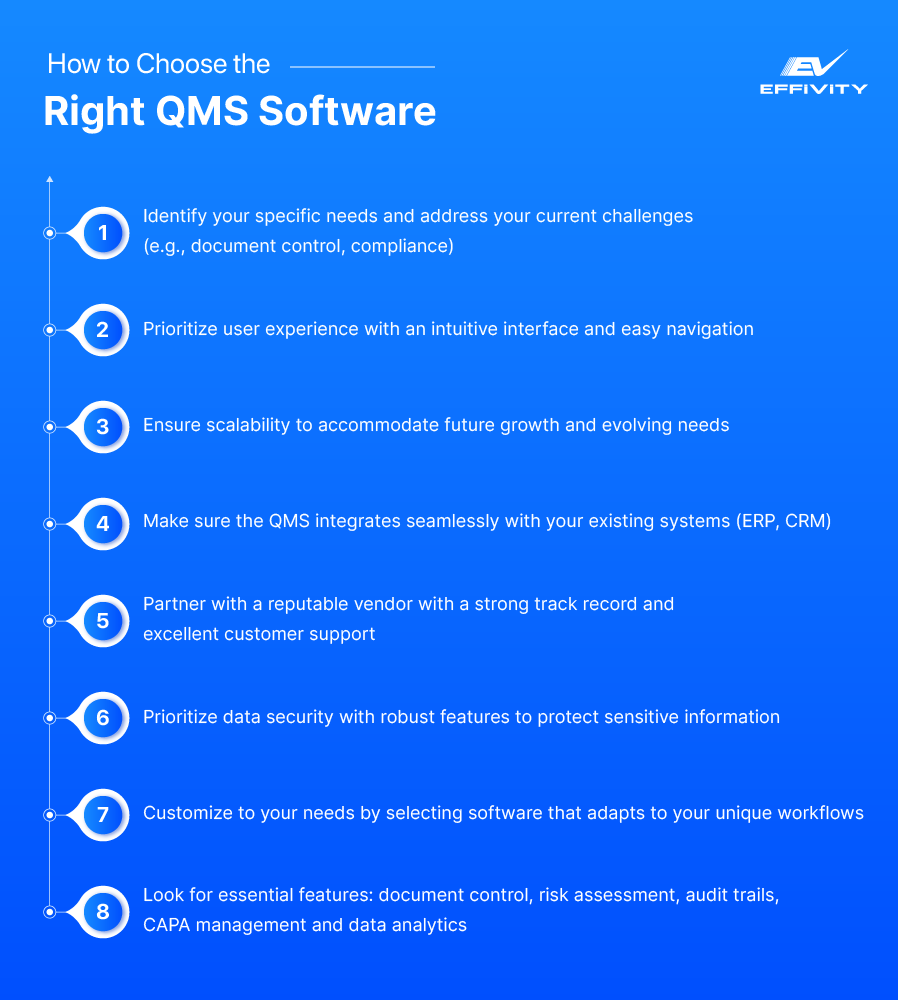
1. Your Organizational Needs
Are you struggling with manual document control, compliance tracking, or audit management? Knowing and understanding your challenges will help you focus on software that addresses these specific issues.
Most importantly, you must consider the industry-specific requirements you want your QMS software to meet, such as regulatory standards or customer expectations.
2. User Experience and Ease of Use
The software’s usability is crucial for successful adoption. Choose a QMS solution with an intuitive interface that minimizes the learning curve for your team.
This means looking for features like customizable dashboards, easy navigation, and a code-free approach to using the software.
If possible, request a demo or a free trial period to assess how user-friendly the QMS software is for your team.
3. Scalability
Your business needs today may not be the same in the future. Therefore, opt for a QMS software that can grow with your organization. This includes the ability to handle increased data volume, add new users, and incorporate additional modules as your processes evolve.
4. Integration Capabilities
A QMS software should seamlessly integrate with your existing systems, such as ERP, CRM, or production management tools. This integration ensures smooth data flow across departments, eliminates data silos, and enhances overall operational efficiency.
When evaluating your options, check if the software supports APIs or pre-built connectors that can facilitate integration without extensive customization.
5. Vendor Reputation and Support
The vendor’s reputation is as important as the software itself. Research the vendor’s track record, customer reviews, and case studies to ensure they have a history of delivering reliable solutions.
Additionally, evaluate their customer support services. Reliable post-implementation support, regular software updates, and a proactive approach to resolving issues are critical for long-term success.
6. Security
Quality data is sensitive, and safeguarding it is paramount. Ensure the QMS software adheres to robust security protocols, including data encryption, regular backups, and access controls.
Additionally, check if the software supports compliance with relevant standards such as ISO 9001, FDA regulations, or industry-specific guidelines.
7. Customization
Every organization has unique processes and workflows. A one-size-fits-all approach may not work for your specific needs.
So, look for software that offers customization options, allowing you to tailor workflows, reports, and dashboards to fit your exact requirements. Configurability ensures that the software adapts to your processes, rather than forcing your processes to fit the software.
8. Quality Management Features
Here are some must-have quality management features of every good QMS software:
- Automated Document Updates and Control: Ensures that all documents are up-to-date and accessible, reducing manual errors.
- Real-time Risk Assessment Alerts: Provides immediate notifications of potential risks, enabling proactive management.
- Customizable Audit Checklists: Allows you to tailor audits to specific needs, improving accuracy and relevance.
- Automated Compliance Tracking: Keeps track of regulatory requirements and ensures your organization stays compliant.
- Instant CAPA Notifications: Alerts you to corrective and preventive actions needed, speeding up response times.
- Interactive Training Modules: Enhances team training with engaging, hands-on learning experiences.
- Supplier Performance Metrics: Tracks and evaluates supplier performance, ensuring quality across the supply chain.
- Detailed Analytics and Insights: Provides in-depth analysis of quality data, helping in informed decision-making.
- Secure Cloud Access: Offers remote accessibility with robust security for data safety and flexibility.
5 Signs That You Need to Transition to a Software-driven QMS
While the benefits of automation and efficiency are clear, timing the shift correctly ensures a smooth transition and maximizes the return on investment.
Here are key indicators and considerations to help determine when it’s the right time to make the switch:
1. Increasing Volume of Documentation
As an organization grows, the volume of quality-related documentation expands significantly. If managing this increasing pile of documents becomes overwhelming, leading to delays in retrieving information, frequent errors, or missed updates, it’s a strong sign that you need QMS software.
Digital systems simplify document control, making it easier to store, access, and update records, which can be particularly beneficial for growing companies.
2. Complexity of Quality Processes
Organizations operating in highly regulated industries or those with complex quality processes may find it challenging to maintain compliance manually.
When the processes become too intricate to handle effectively through paper-based systems, especially for audits, risk management, or corrective actions, it’s time to consider transitioning.
3. Prolonged Time to Resolution for Quality Issues
Manual systems often slow down the resolution of quality issues due to the time it takes to identify, document, and address problems. If your organization experiences prolonged times to resolve customer complaints, defects, or non-conformities, it may be time to adopt automated quality management.
4. Frequent Non-compliance Issues
Is your organization struggling to keep up with regulatory requirements or industry standards? Are you facing recurring non-compliance issues or failed audits?
If yes, then quality management software can help you automate compliance, reduce the risk of penalties, and improve overall quality performance.
5. High Cost of Quality Management
Manual quality management often incurs hidden costs, including labor-intensive document handling, error rectification, and audit preparations. If your organization is experiencing high costs related to these activities, transitioning to a software-driven QMS can lead to significant cost savings.
Frequently Asked Questions
1. What is the difference between a quality management system (QMS) and quality control (QC)?
QMS is a comprehensive system that manages overall quality, including policies, procedures, and continuous improvement.
QC, on the other hand, focuses specifically on identifying and correcting defects in products or services.
2. How often should a QMS be reviewed?
A QMS should be reviewed regularly, typically annually, or whenever significant changes occur in processes, regulations, or organizational structure.
3. How does ISO 9001 relate to a QMS?
ISO 9001 is an internationally recognized standard for QMS, providing a framework of principles and requirements that organizations can follow to ensure quality management best practices.
4. Is QMS software suitable for small businesses?
Absolutely. Scalable QMS solutions can be tailored to fit the needs of small businesses, offering cost-effective options that grow with the company.
5. How long does it typically take to implement QMS software?
Implementation timelines vary but generally range from a few weeks to several months, depending on the complexity of the organization and the QMS software.