Over 55% of consumers pledge their loyalty to brands that consistently deliver exceptional-quality products and services. Customers tend to return when they are sure that the brand will always deliver the expected quality of product or service. Businesses take many measures to ensure this consistent quality is maintained across the board. To do this, they follow certain frameworks and guidelines that allow them to optimize their performance.
One such guideline is the ISO 9001 standard. This is a framework that pushes organizations towards redesigning and optimizing their quality management system to make sure that they are able to remain consistent with the products they deliver.
The ISO standard is updated regularly. To stay compliant, organizations must be familiar with these changes. In this blog post, we dive into the newest changes to the ISO 9001 standard, its new principles and how you can implement this standard successfully in your business.
What is the ISO 9001 Standard?
The ISO 9001 Standard is a rulebook that helps your business maintain quality and consistency across your processes and products. It ensures that all business processes are optimized in a way that quality and customer satisfaction are prioritized. The standard ensures that the quality management systems in your organization are efficient and facilitates continual improvement.
The ISO 9001 Standard is revised regularly to incorporate changes in market conditions and industrial expectations. The new ISO 9001:2015 standard replaces the older ISO 9001:2008 as the framework to follow to ensure that the organization meets quality expectations. Compliance with the ISO 9001 certification requirements ensures that your organizational processes run smoothly, you consistently maintain quality and that your customers remain satisfied.
ISO 9001:2015 vs. ISO 9001:2008: Key Differences
ISO 9001:2015 and ISO 9001:2008 differ significantly in structure, terminology, and principles. Understanding these differences helps organizations transition smoothly and enhance their quality management systems.
Structure
ISO 9001:2015 features a new High-Level Structure (HLS), which aligns with other ISO management standards. This change introduces a standardized framework, making it simpler for organizations to integrate multiple management systems. The 2015 version has ten clauses, compared to eight in the 2008 version. These ten clauses provide a more comprehensive and organized approach to quality management.
The new structure includes:
-
Scope:
Delineates the boundaries and applicability of the standard. -
Normative References:
Lists documents that are essential for understanding and applying the standard. -
Terms and Definitions:
Explains specific terms used within the standard. -
Context of the Organization:
Requires understanding of the organization's context and relevant stakeholders. -
Leadership:
Emphasizes the role of top management in quality management. -
Planning:
Focuses on risk-based thinking and planning. -
Support:
Covers resources, competence, awareness, communication, and documented information. -
Operation:
Addresses the planning, control, and production of products and services. -
Performance Evaluation:
Involves monitoring, measurement, analysis, and evaluation of performance. -
Improvement:
Focuses on continual improvement and addressing nonconformities.
New Terminology
The 2015 version introduces several new terms based on a modern approach to quality management. Some of these terms are:
-
Products and Services:
Replace the term "product" to clarify that the ISO 9001:2015 standard applies to both tangible products and intangible services. -
Documented Information:
Combines "documents" and "records" into a single term, offering flexibility in how organizations manage and store information. -
External Provider:
Replaces "supplier" to emphasize the broader range of external entities involved in the supply chain. -
Risk-Based Thinking:
Encourages a proactive approach to identifying and addressing risks and opportunities. -
Context of the Organization:
Requires organizations to comprehensively evaluate all external and internal elements that have the potential to influence their quality management system. -
Interested Parties:
Expands the focus from customers to include other stakeholders like employees, suppliers, and regulators. -
Leadership:
Emphasizes the active involvement and accountability of top management. -
Improvement:
Broadens the concept to include continual improvement, not just corrective actions.
New Principles of ISO 9001:2015
ISO 9001:2015 introduces several new principles that build upon those in ISO 9001:2008. Here are the key principles:
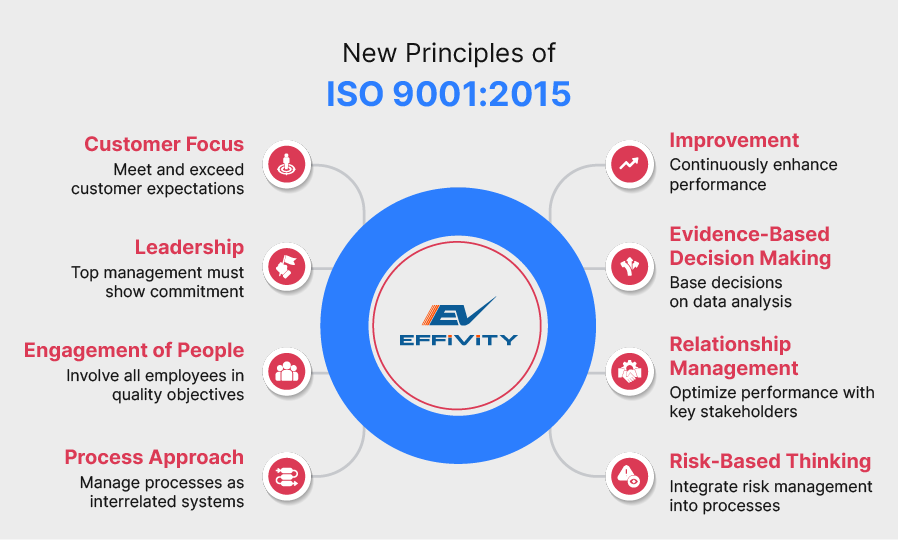
1. Customer Focus:
Organizations must prioritize meeting and exceeding customer expectations. This principle emphasizes understanding customer needs, meeting requirements, and striving to exceed customer expectations. Continuously seeking and leveraging customer feedback is essential for proactively refining and enhancing products and services.
2. Leadership:
Top management plays a decisive role in driving quality by demonstrating strong leadership and unwavering commitment. Leaders must foster a unified vision and clear direction to cultivate a workplace culture that prioritizes the achievement of quality objectives.Quality policies must be communicated, understood, and applied throughout the organization.
3. Engagement of People:
All employees should be involved in achieving quality objectives. Engaged employees are more motivated, competent, and empowered to contribute to the organization's success. Organizations should build an environment of trust and collaboration, providing opportunities for training and development to enhance skills and competencies.
4. Process Approach:
Organizations must understand and manage processes as interrelated systems. This approach enhances efficiency and effectiveness, leading to consistent and predictable results. By mapping out processes, identifying inputs and outputs, and monitoring performance, organizations can optimize operations and reduce waste.
5. Improvement:
Organizations must continuously improve performance. This involves identifying and acting on opportunities for improvement to enhance the quality management system. The principle encourages a proactive attitude towards finding ways to make processes more efficient, reduce errors, and increase customer satisfaction.
6. Evidence-Based Decision Making:
According to ISO 9001 Quality Management system standard requirements decisions must be based on analysis and evaluation of data. Reliable data from monitoring and measuring helps organizations make informed decisions, leading to better outcomes. By gathering and analyzing data on all key performance metrics, organizations can identify trends, assess risks, and make strategic decisions that drive improvement.
7. Relationship Management:
Relationships with interested parties must be managed to optimize performance. Effective relationship management with suppliers and partners enhances performance and creates value. Organizations should establish mutually beneficial relationships with key stakeholders, ensuring clear communication, collaboration, and shared objectives.
8. Risk-Based Thinking:
Risk management must be integrated into all processes. This proactive approach helps identify and mitigate potential issues before they arise, ensuring resilience and capability in achieving objectives. By assessing risks and opportunities, organizations can implement preventive measures, allocate resources effectively, and maintain continuous improvement.
Final Thoughts
Successfully implementing ISO 9001:2015 involves a systematic approach. Start by thoroughly familiarizing yourself with the standard's requirements, then assess your current practices to pinpoint areas that need to be enhanced or aligned with the standard. Develop a clear action plan, secure top management commitment, and train your team on the standard. Document your processes, conduct internal audits, and seek certification from an accredited body.
Using a Quality Management System software can streamline this process. It automates documentation, tracks compliance, and ensures continuous improvement, making it easier to meet ISO 9001:2015 requirements and rise above competition in the industry.