Imagine a manufacturing company develops and ships a batch of untested products only to get them rejected because they don't meet the specifications. The result? Frustrated clients, financial losses, and reputational damage.
Or consider an organization that overlooks a minor safety lapse, which spirals into a workplace accident. These situations are not just costly but avoidable—if managed proactively.
Scenarios like these underscore the importance of identifying and addressing non-conformance in organizational processes. It refers to any quality, environmental standards, or workplace safety issues that can affect operations and risk compliance with standards like ISO 9001, ISO 14001, and OHSAS 18001.
But here's the thing: non-conformances are an opportunity for improvement. By understanding what causes deviations, how they occur, and how you can address and improve them, you can manage non-conformances effectively and ensure operational excellence.
In this article, we'll delve into the causes, types, and solutions for addressing non-conformance while aligning with ISO standards.
What is Non-conformance?
Non-conformance occurs when a product, process, or system deviates from established requirements. These requirements include regulatory standards, internal procedures, customer expectations, or the criteria specified in ISO certifications. For instance:
- Under ISO 9001 requirements for quality management systems, a non-conformance may involve defective products or inefficiencies.
- In ISO 14001, a non-conformity could relate to environmental impacts exceeding permissible levels.
- Within the scope of the occupational health and safety management system, non-conformance might arise from workplace hazards that compromise employee safety.
Non-conformances can be classified into minor, which involve limited impact and easy resolution, or major, which indicate significant failures that may disrupt operations or risk certification.
Common Causes of Non-conformance
Identifying the root causes of non-conformance is crucial in implementing effective solutions. These can include-
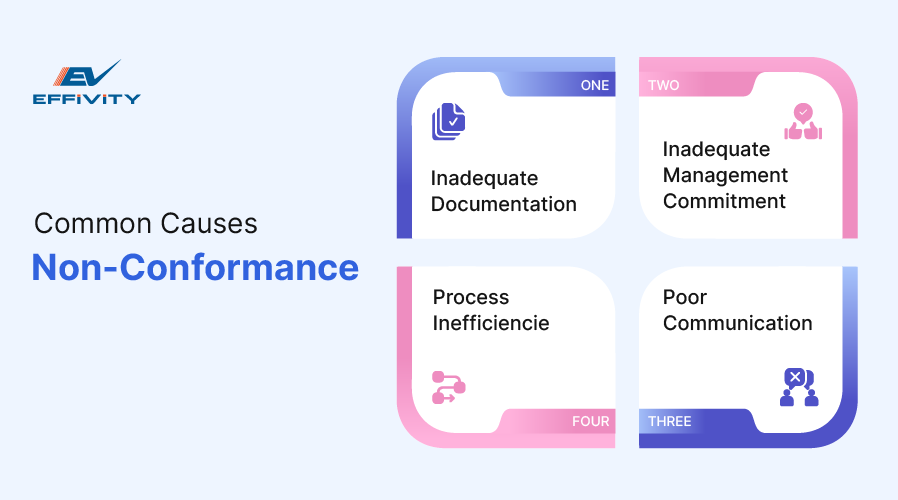
1. Inadequate Documentation
When it comes to ISO compliance, proper documentation is essential for accuracy and efficiency. Poorly defined processes or incomplete documentation often lead to errors or inconsistencies in execution. It can cause a lack of awareness among stakeholders, leading to non-conformities.
2. Inadequate Management Commitment
Successful ISO implementation requires a strong commitment from the top management to establish and maintain various management systems. However, low involvement from the C-suite can often lead to poor resource allocation—whether tools, personnel, or infrastructure, ineffective communication, and ineffective implementation of management systems.
Without management support and resource allocation, it can be difficult to manage processes and often results in non-conformities.
3. Poor Communication
An organization that is highly coordinated in its processes and has strong communication between departments can ensure a better handle on non-conformities. Why? Because miscommunication between departments or stakeholders can lead to misunderstandings about requirements or responsibilities. This can also result in duplication of efforts and affects how you manage a non-conformity before it becomes a serious issue.
4. Process Inefficiencies
For ISO certification, organizations must establish, implement, and manage various processes to meet the regulatory requirements. This further requires establishing responsibilities and maintaining strong control to ensure efficiency.
However, if any of these processes or controls are lacking, it could lead to non-conformities in the organization. Outdated or inefficient processes, which are not evaluated or updated periodically, can be highly risky for a company.
Types of Non-conformances
Non-conformance can typically manifest itself in two ways, depending on the severity of the non-conformance for specific products, services, and processes.
Major Non-Conformance
A major non-conformance is an issue or failure that significantly impacts the product's quality, safety, or compliance and can potentially affect the organization's workflow. A major non-conformance can have a serious impact on a company, costing time, resources, and effort.
It can often be a repeated occurrence or complex issue that needs time to be resolved and can possibly impact the business's reputation. Examples of major non-conformance include supplying untested products, making multiple unauthorized changes to documentation, or security vulnerabilities that can lead to data breaches.
Minor Non-Conformance
A minor non-conformance is any failure that happens at a small scale and is unlikely to impact the product or the entire organization. Such non-conformances are often isolated events with limited consequences and can be easily resolved with effective corrective actions.
However, if left unchecked, minor non-conformances can easily turn into bigger ones. So, it is important to have effective processes in place to identify, address, and correct non-conformances proactively.
Examples of minor non-conformances include failure to meet internal deadlines, minor defects in the product, or customer complaints that are not addressed and resolved on time.
Steps to Address Non-conformance
Resolving non-conformance involves a systematic approach that ensures both corrective and preventive actions are implemented effectively. The following steps are critical:
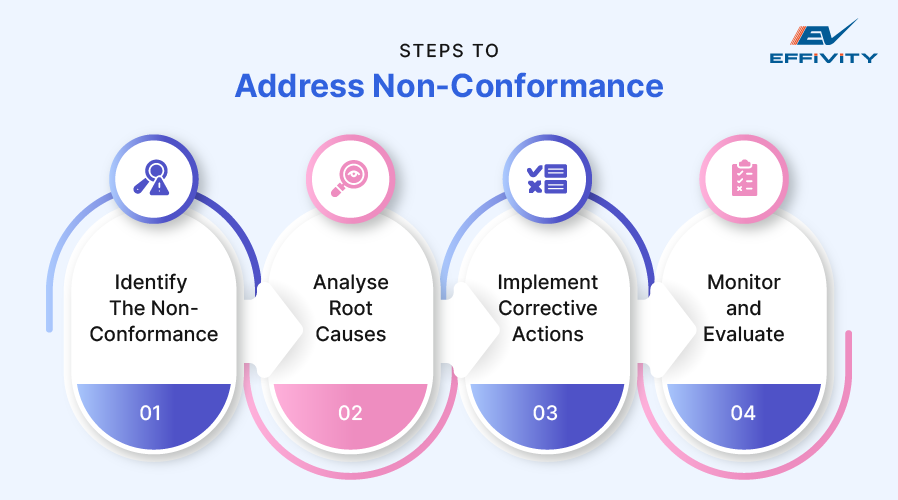
1. Identify the Non-conformance
The objective is to identify non-conformances in the organization that do not meet the organizational requirements, specifications, or standards. For this, audits, inspections, or customer feedback can be used to detect deviations from requirements.
This also includes creating formal documentation detailing all the identified non-conformances, including their location, nature, date, people involved, products, processes, and more. The documentation will make it easier to share essential information with relevant stakeholders and ensure that non-conformances are addressed properly.
2. Analyse Root Causes
Once you've identified the non-conformance, the next step is to investigate and determine its root causes and severity for effective corrective actions. Understanding the root causes will help you determine if there is any way you can eliminate or reduce the root causes.
3. Implement Corrective Actions
Implement immediate corrective actions to fix the non-conformance and mitigate its impact. For example, repairing faulty equipment or revising a defective process. Proactive action is necessary to minimize the impact of major non-conformances or prevent minor non-conformances from turning into major ones.
Further, depending on the cause and severity of non-conformance, focus on preventing recurrence by updating procedures, enhancing training, or improving communication.
4. Monitor and Evaluate
It is important to regularly monitor the progress and effectiveness of corrective and preventive actions. Conduct follow-ups via internal audits and investigations and review KPIs to ensure compliance is maintained.
Maintain and update the non-conformance report, which will highlight the issue, the corrective action, and the resolution of the problem. If the non-conformity is not resolved, another report must be created detailing the original issue and why it wasn't resolved.
Solutions for Minimising Non-conformance
Organizations can proactively reduce the occurrence of non-conformance by implementing robust strategies tailored to ISO standards:
1. Strengthen Employee Training
Regular training sessions ensure that employees are well-versed in ISO requirements and understand their roles in maintaining compliance.
2. Improve Documentation Practices
Comprehensive, accurate, and accessible documentation reduces ambiguity in processes and ensures consistency. Using automated systems for your management systems makes it easy to create, manage, edit, and share documents in real-time and ensures consistency in processes.
3. Adopt a Risk-Based Approach
ISO standards like ISO 9001 encourage organizations to anticipate potential risks and implement controls to prevent non-conformance.
4. Leverage Technology
Invest in Quality Management Software (QMS) to streamline the tracking, analysis, and resolution of non-conformance issues. Digital tools ensure real-time monitoring and provide actionable insights.
5. Foster a Culture of Accountability
Encourage employees to take ownership of their tasks, report deviations promptly, and actively contribute to continuous improvement.
6. Conduct Regular Audits
Periodic internal and external audits provide a clear picture of compliance levels and areas requiring attention. Such a proactive approach puts you on a path to continual improvement, ensuring the same non-conformances do not reoccur.
Conclusion
Non-conformance is an inevitable part of managing complex systems, but its impact can be minimized through effective strategies. It is important for organizations to address the root causes, implement robust solutions, and maintain strong processes to ensure compliance, improve efficiency, and achieve long-term success.
Ultimately, a proactive approach to managing non-conformance not only safeguards certifications but also fosters a culture of excellence and continuous improvement.