Running a business today means managing a web of different systems—quality assurance, environmental responsibility, workplace safety, and more. Each plays a vital role, but when handled separately, they can create compliance inefficiencies and duplicate work.
An Integrated Management System (IMS) unifies these separate processes under one roof and promotes a more cohesive approach to meeting business objectives.
Let’s break this down.
What Is an IMS?
An Integrated Management System is like one overarching system that brings together multiple management systems. So, instead of managing quality, environmental, health and safety, and other areas in silos, an IMS creates synergy by interconnecting these processes.
As a result, it provides a holistic view of an organization’s performance. This helps businesses align their objectives, improve efficiency, and ensure consistency across all processes.
Common Standards Covered Under an IMS
An IMS can integrate various international standards, each targeting specific aspects of business operations. Here are some of the most commonly included standards:
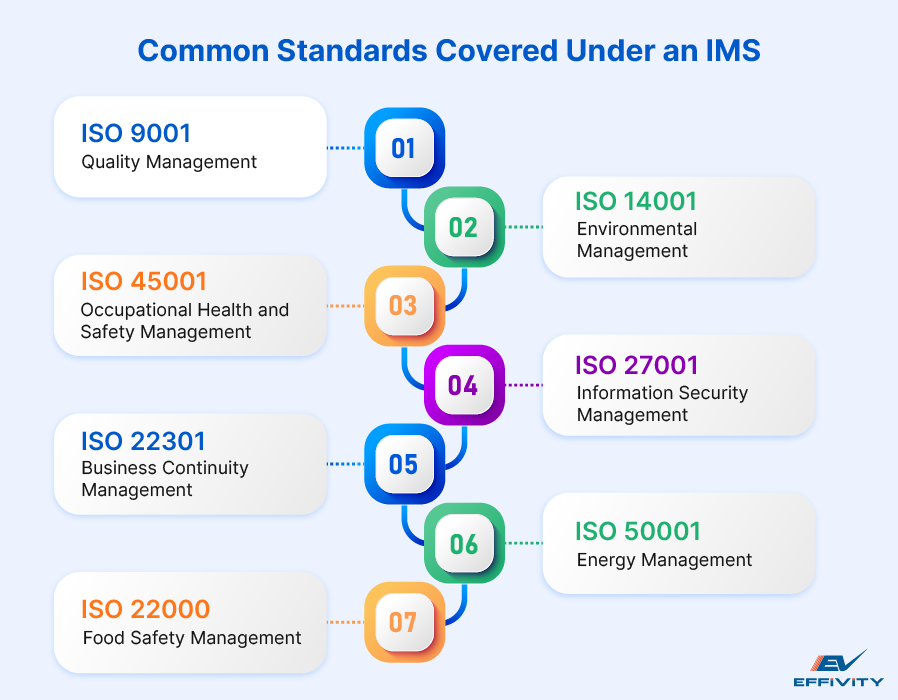
-
ISO 9001: Quality Management
Focuses on consistently meeting customer and regulatory requirements while also enhancing customer satisfaction through a process of continuous improvement.
-
ISO 14001: Environmental Management
Provides a framework for managing environmental responsibilities, aiming to reduce environmental impact and ensure compliance with regulations.
-
ISO 45001: Occupational Health and Safety Management
Helps organizations provide a safe and healthy workplace by reducing work-related injuries and illnesses.
-
ISO 27001: Information Security Management
Addresses the protection of information assets, ensuring that information security risks are managed effectively.
-
ISO 22301: Business Continuity Management
Prepares organizations to deal with disruptive incidents, ensuring that critical business functions continue during and after a crisis.
-
ISO 50001: Energy Management
Focuses on improving energy performance, including energy efficiency, use, and consumption.
-
ISO 22000: Food Safety Management
Ensures that food products are safe for consumers by managing food safety risks at every stage of the supply chain.
Benefits of Implementing an Integrated Management System
Below are six ways an IMS transforms your business:
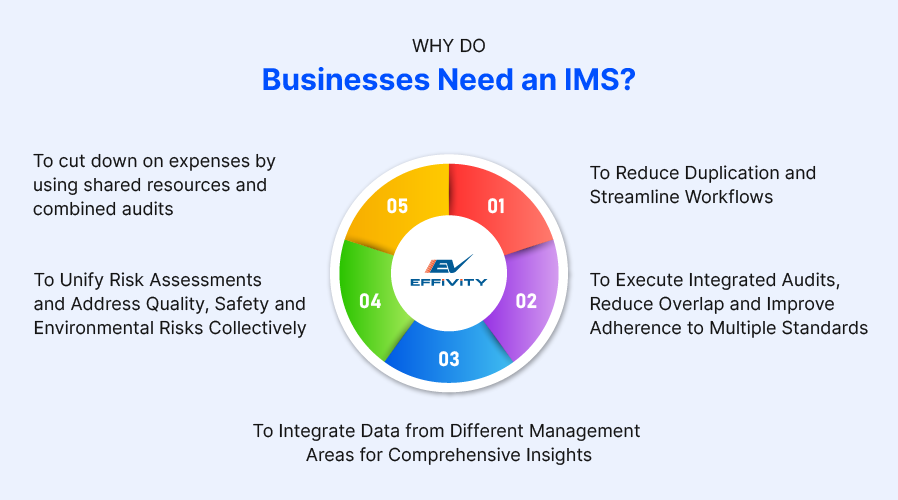
1. Streamlines Operations for Maximum Efficiency
An integrated management system eliminates the need for separate systems, which reduces administrative tasks and frees up employee time to focus on core functions. With a unified approach, processes become more efficient in terms of quicker turnaround times and higher productivity.
Additionally, teams also work better together as everyone follows the same rules, thus speeding up processes.
2. Enhances Compliance Through Unified Standards
Consider a healthcare provider that must adhere to ISO 45001 for occupational health and safety and ISO 27001 for information security. By integrating these standards using an IMS, the provider can conduct unified audits, thus reducing audit fatigue often experienced by staff.
Moreover, an IMS also ensures that the organization meets all regulatory requirements with minimal overlap so that there are fewer penalties and increased accountability.
3. Helps You Make Decisions Backed by Data
IMS enhances decision-making by centralizing data from various management areas, allowing leaders to make informed choices based on comprehensive insights.
For instance, a logistics company using an IMS can track quality control, environmental impact, and safety incidents in one dashboard. This integrated approach allows management to spot trends, such as a recurring issue with a particular supplier, and address them promptly.
A holistic view ensures decisions are not made in silos but consider the interconnected nature of business processes.
4. Encourages Proactive Risk Management for Greater Stability
By integrating risk management across all systems, IMS helps businesses identify and mitigate potential risks before they escalate. This unified approach ensures that risks related to quality, safety, and environmental factors are addressed collectively, providing a comprehensive risk profile.
For instance, a construction firm implementing ISO 45001 for safety and ISO 14001 for environmental management can use the IMS to conduct integrated risk assessments.
5. Saves You Money by Combining Efforts
An integrated management framework saves money by bringing different management tasks together, reducing the need for separate resources.
For example, a retail chain that combines quality, environmental, and safety systems can create one training program instead of three. Similarly, audits can be combined to cut down on time and costs.
These savings can be reinvested in other parts of the business, such as innovation or employee development.
How to Implement an IMS?
Implementing IMS requires a strategic approach to ensure seamless integration of various management systems. Here’s a step-by-step guide to help businesses navigate the process effectively:
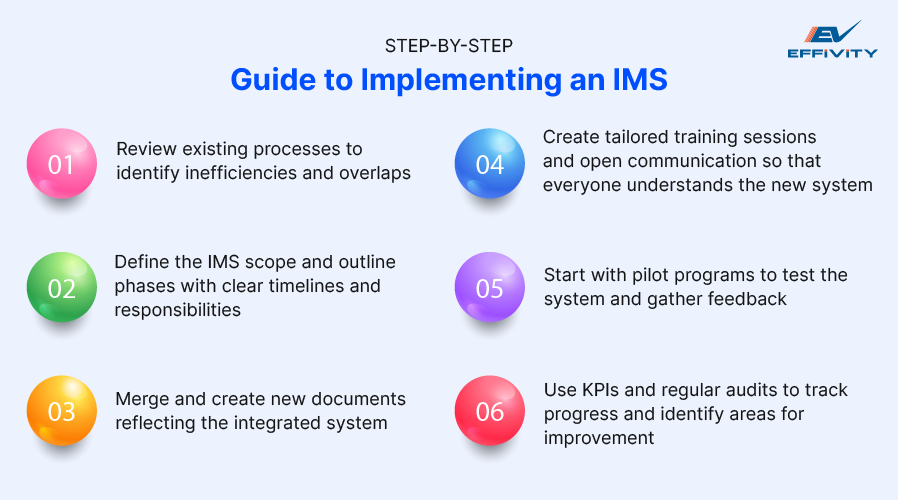
1. Start With an Initial Assessment
Start by reviewing all existing processes, policies, and standards to pinpoint inefficiencies, duplications, or gaps. Engage stakeholders across departments to get a holistic view of the current state and gather insights on areas needing improvement.
For example, a manufacturing company using separate systems for quality (ISO 9001) and environmental management (ISO 14001) may find overlapping reporting processes that could be unified.
2. Create a Detailed Plan
Define the scope of your IMS clearly—whether you’re integrating two or more standards. Break down the process into phases with specific timelines, resources needed, and responsibilities that need to be assigned.
Set a milestone for each stage of implementation so that everyone knows their role and what to expect.
3. Develop Comprehensive Documentation
This step involves more than just merging existing documents—it requires creating new ones that reflect the integrated nature of your system. You must clearly outline responsibilities, procedures, and compliance requirements, making it easy for employees to understand and follow.
For instance, a technology firm combining ISO 27001 and ISO 9001 might develop a unified policy manual that addresses data security within the context of overall quality management. This approach not only reduces the paperwork burden but also helps ensure consistency and clarity across all areas of the business.
4. Conduct Training and Foster Communication
Employees at all levels must understand the newly integrated processes, why they are being introduced, and how they impact on their daily tasks.
To achieve this, begin with targeted training sessions tailored to different roles—senior management, operational staff, and department heads. Alongside formal training, maintain open channels of communication, such as regular team meetings and updates, to address questions and gather feedback.
5. Roll Out the Implementation
Start with pilot programs in specific departments or locations to test the new system’s effectiveness and iron out any issues. Use this phase to gather real-world feedback, make necessary adjustments, and demonstrate quick wins.
The gradual implementation also allows for careful monitoring and gives employees time to adapt, ensuring that the transition to an integrated system is manageable and effective.
6. Monitor Performance and Drive Continuous Improvement
Continuous monitoring and improvement are essential to ensure the system remains effective and compliant with evolving standards.
Therefore, set up key performance indicators (KPIs) to track progress, such as reduction in audit times or improved compliance rates. In addition to this, regular internal audits and management reviews should be conducted to identify areas for improvement.
What Is IMS Software?
An integrated management system software is a digital tool designed to streamline the integration and management of multiple standards within an organization. It combines processes for quality, environmental, health and safety, and other management systems into an automated unified platform.
Why Implement IMS Software?
Let’s explore the key benefits of an IMS software:
- Centralized Management: Simplifies the management of various standards by bringing all processes under one platform, so you don’t have to switch between different platforms
- Automated Compliance: Automates compliance tracking and reporting, ensuring you stay up to date with regulatory requirements
- Enhanced Efficiency: Streamlines workflows by automating routine tasks such as audits, corrective actions, and document updates
- Real-time Insights: Provides dashboards and reports that offer real-time insights into system performance, helping identify areas for improvement
- Scalability: Easily adapts to organization growth or changes, allowing for the integration of additional standards as needed
Factors to Consider When Choosing an IMS Software
Choosing the right IMS software is crucial for effectively managing your integrated systems. Here’s what you should consider when selecting IMS software:
- Customization: Ensure the software can be tailored to your organization’s specific needs and industry requirements.
- User-friendliness: Look for an intuitive interface that requires minimal training for your team to adopt.
- Integration Capabilities: Check if it can integrate with existing systems like ERP or CRM tools for seamless operation.
- Compliance Features: Verify that the software supports the specific standards your organization needs to comply with.
- Support and Updates: Opt for a provider that offers robust customer support and regular software updates to keep up with regulatory changes.
How Effivity’s IMS Software Can Help?
Effivity’s IMS Software simplifies the integration of multiple management systems and provides you with a holistic view of all your operations in one place.
Most importantly, you can customize the IMS to add or remove management systems and create unique combinations. So, if you want an integrated QHSE management software, you can choose to integrate Effivity’s quality as well as health and safety systems to build your IMS.
Effivity’s IMS software has been developed by seasoned ISO experts, thus offering features such as a secure cloud infrastructure, 30+ integrations, pre-built templates, real-time reports, multilingual support, etc.
Start a free trial today to explore Effivity IMS!