In today's advanced economy, manufacturing activities remain critical for both developing and developed markets. However, given the rapid advancements in technologies and an ever-evolving regulatory scenario, most manufacturers, from global manufacturers to small, more regional organizations, struggle to keep up with the industry's quality, safety, and environmental requirements.
A South African manufacturing and distribution company looking to expand its production was also struggling with operational inefficiencies, ineffective customer management, and improper safety and quality management. Realizing their challenges, they partnered with Effivity to enhance its operations and compliance with the integrated QHSE management software.
About the South African Company
This company, headquartered in Johannesburg, South Africa, is a leading manufacturer and distributor of global building and environmental solutions. It offers various products to its clients with extensive sales and distribution networks in major cities across South Africa.
With years of expertise in offering superior environmental solutions to its clients, the company was now planning to expand its production into the global market. However, to do so, they wanted to address the various challenges in their organization related to quality and safety, risk management, as well as customer management.
Challenges Faced
The South Africa-based manufacturer was dealing with fragmented data, inconsistent processes, and challenges in complying with both local and international regulatory requirements. Below are some of the key challenges the company encountered:
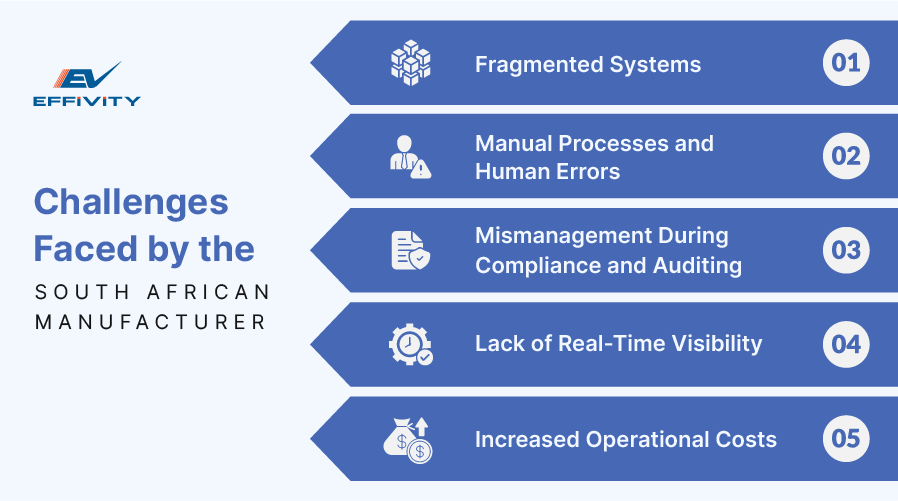
1. Fragmented Systems
The company relied on multiple systems and documentation to manage quality, health and safety, and environmental standards. This lack of cohesion resulted in data silos, making it difficult to track performance across departments and ensure alignment with corporate QHSE goals.
2. Manual Processes and Human Errors
Most of the company's QHSE processes were managed manually, resulting in human errors, reporting delays, and difficulty maintaining up-to-date records. The reliance on manual tracking also made audits more time-consuming and prone to mistakes, jeopardizing compliance with industry standards.
3. Mismanagement During Compliance and Auditing
Regulatory compliance, especially in manufacturing industries, requires access to accurate documentation and adherence to stringent protocols. The lack of a centralized QHSE system made it challenging for the company to maintain easy access to documentation and consistent compliance across different sites. Each department managed its own records, leading to gaps in data that often resulted in inaccurate audits and penalties.
4. Lack of Real-Time Visibility
With data scattered across multiple platforms, management struggled to gain real-time insights into QHSE performance. A lack of visibility delayed decision-making, especially when prompt response was necessary to ensure safety within the organization. This further hindered the company's ability to identify and rectify potential safety or quality issues before they escalated.
5. Increased Operational Costs
The inefficiencies in managing multiple systems and relying on manual processes increased operational costs. These additional expenses strained the company's resources and reduced its ability to invest in further QHSE improvements.
The Solution- Effivity's Integrated QHSE Software
Given these challenges, the company sought a cloud solution to provide integrated safety and quality management, risk management, customer management, and in-depth risk-based performance monitoring.
After exploring multiple solutions, they narrowed it down to Effivity QHSE software, which offers a unique approach to implementing and managing organizational processes with a single integrated platform while improving visibility, efficiency, and profitability. It enables an organization to improve processes and efficiency by applying cross-organizational benchmarking and enhanced gap analysis.
With its end-to-end capabilities to capture nonconformance, conduct root-cause analysis, capture risk, and create risk matrices, the solution can help organizations ensure the highest level of safety. Further, the customer complaint module helps streamline customer management operations, provides better visibility to customers' records, and improves quality processes to mitigate further customer complaints.
"Effivity's integrated modules & its robust reporting feature not only helps an organization to gain visibility but also drives continuous improvement & helps them to achieve their objectives," said Kaushal Sutaria, Senior Manager of Effivity.
Effivity's QHSE software is designed to help companies like the South Africa-based manufacturer achieve operational excellence through seamless integration and management of their QHSE processes.
Here are the key features that helped the South African company take a systematic approach to QHSE management in the organization-
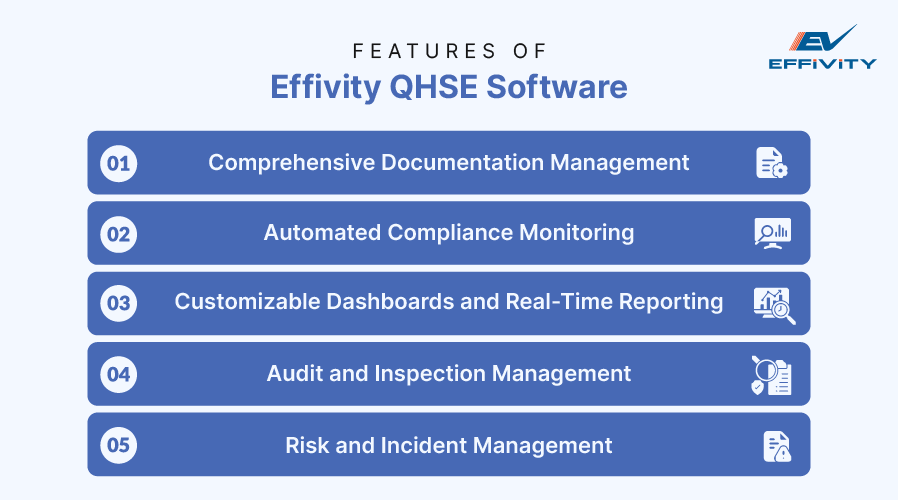
1. Comprehensive Documentation Management
Effivity's software offers a robust documentation management system that stores all QHSE records in a centralized location. This way, it eliminates the risk of missing or outdated records and makes it easy to retrieve information during audits or compliance checks.
2. Automated Compliance Monitoring
Effivity's built-in compliance monitoring tools help organizations stay on top of local and international regulatory requirements. The software automatically flags non-compliance issues, generates corrective action plans, and provides automated reminders for follow-ups, ensuring continuous improvement in the company.
3. Customizable Dashboards and Real-Time Reporting
The customizable dashboards provide real-time insights into QHSE performance, allowing management to identify potential risks, enhance quality processes, and address safety issues within the workplace. With these insights, the company can make data-driven decisions and improve its overall QHSE standards.
4. Audit and Inspection Management
Effivity's software simplifies the audit process by automating inspection schedules, tracking corrective actions, and generating reports. All audit-related tasks are completed on time, and any identified issues are promptly addressed.
5. Risk and Incident Management
Effivity's QHSE software includes tools for managing risks and incidents, enabling organizations to track and mitigate potential hazards. The system allows users to document incidents, perform root cause analysis, and implement corrective actions to ensure a safer working environment.
To Wrap Up
Effivity is a customer-first-choice Governance – Risk – compliance software solution that offers a powerful platform to augment Quality, Environment, Health, and Safety management systems.
The tool is highly flexible and scalable, thanks to its cloud-based deployment model, which even allows you to customize various modules to align with your business needs. Easy to use and operate, Effivity will grow as your income grows.
Effivity's comprehensive compliance management software for QHSE compliance not only helps in effectively managing all regulatory and quality requirements for various standards like ISO 9001:2015, ISO 14001:2015, ISO 45001, ISO 17025, ISO 13485, ISO 22000 but also helps to achieve ISO certification with utmost ease.
Explore the unique capabilities of Effivity QHSE software with a free demo today!