Thinking that your workplace is hazard-free may be one of the most expensive mistakes you can make. The truth is that every workplace harbors hazards. Of course, the degree to which hazards are prevalent varies. However, even low-risk workplaces, such as offices, are prone to hazards.
A hazard in your workplace is anything that can cause injuries, damage to property, or harm to the environment. Every organization has the responsibility to keep its employees, the environment, and its own property safe. To do this, they must be able to identify and prevent hazards before they occur.
Hazard assessment can help you identify elements in your workplace that threaten to cause harm to your employees. But the big question is, “Who is responsible for conducting a hazard assessment?”
In this article, we answer this question and also take an in-depth look into how the hazard assessment process works, what steps you need to follow, and how automation can help simplify this process.
What is a Hazard Assessment?
A hazard assessment is a carefully planned process by which you can identify potential risks and threats in your workplace that could harm your employees, your property, and the environment. A typical hazard assessment starts with identifying possible sources of harm, evaluating the risks they pose and how much damage they can actually cause, and finally, putting in place control measures to either eliminate or minimize these risks.
Who is Responsible for Conducting a Hazard Assessment?
Your organization carries the primary responsibility for conducting a hazard assessment. While you may not have to perform the assessment yourself, the accountability falls on your business. Assigning clear occupational safety roles ensures hazards are identified and addressed before they lead to workplace accidents.
Here are major reasons why this responsibility lies with employers:
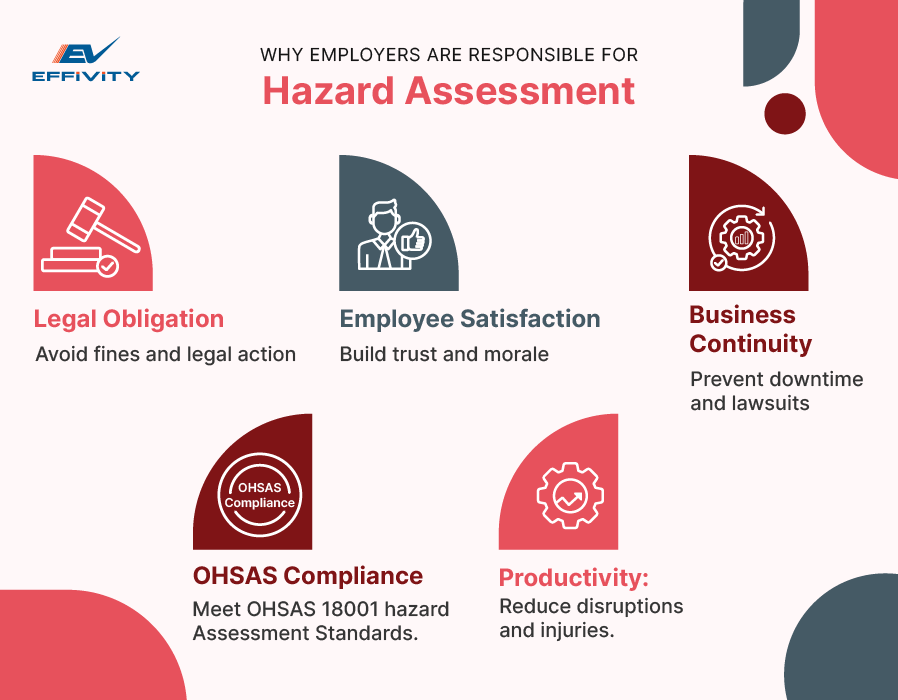
- Legal Obligation: Workplace safety laws require organizations to assess and control hazards. Failure to comply with workplace safety accountability standards can result in fines, legal action, or reputational damage.
- OHSAS Compliance: Adhering to OHSAS 18001 hazard assessment protocols ensures your workplace meets international safety standards, reducing risks and liability.
- Employee Satisfaction: Workers feel more secure when they see their employer prioritizing safety. A well-executed hazard assessment builds trust and improves workplace morale.
- Employee Productivity: A safe workplace environment leads to fewer disruptions and injuries. Reduced absenteeism and workplace incidents help maintain operational efficiency.
- Business Continuity: Workplace accidents can lead to downtime, lawsuits, and insurance claims. Conducting assessments helps you prevent costly setbacks.
- Environmental Protection: Certain hazards can also impact the environment. Assessing risks allows you to implement measures that prevent pollution and regulatory fines.
How to Conduct a Hazard Assessment?
Every hazard assessment should follow a structured process. The HIRA (Hazard Identification and Risk Assessment) framework helps businesses place the steps of identifying workplace hazards in the correct order to ensure no risks are overlooked.
Step 1: Gather Information on Workplace Hazards
Begin by collecting all available data on existing hazards. Review past safety reports, incident logs, and regulatory requirements. This step helps you understand the risks already documented within your organization.
Step 2: Inspect the Workplace for Safety Risks
A physical inspection is necessary to uncover risks that may not be documented. Evaluate machinery, electrical systems, ventilation, and overall working conditions. Industrial hygiene practices can help identify exposure risks, such as poor air quality or hazardous chemicals.
Step 3: Identify Health Hazards
Not all risks are physical. Employees may be exposed to chemical, biological, or ergonomic hazards that affect their long-term health. Assess noise levels, repetitive strain risks, and chemical handling procedures.
Step 4: Investigate Past Incidents and Emergency Risks
Review accident reports to identify recurring issues. Additionally, consider risks associated with emergencies such as fires, spills, or power failures. Assessing both routine and non-routine situations ensures a comprehensive safety plan.
Step 5: Prioritize and Implement Safety Controls
Not all hazards carry the same level of risk. After identifying potential dangers, rank them based on severity and likelihood of occurrence. Introduce preventive measures, such as protective equipment, safety training, or engineering controls, to mitigate risks effectively.
Automating the Hazard Assessment Process
Manually conducting a hazard assessment involves extensive paperwork, compliance tracking, and documentation. The process can be pretty time-consuming, especially when multiple workplace safety regulations must be followed. Managing these tasks manually increases the risk of errors and delays in compliance reporting.
A digital tool aligned with OHSAS guidelines simplifies the assessment process by automating hazard identification, tracking, and mitigation efforts. Meeting ISO 18001 standards also becomes easier with a structured approach that ensures consistency in documentation.
Here’s how automation improves hazard assessments:
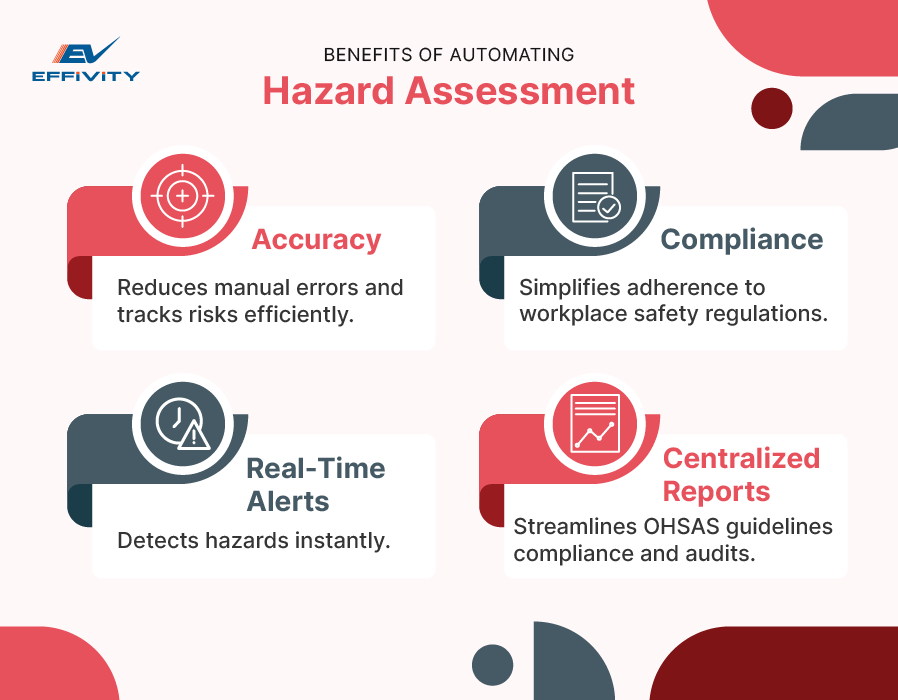
- Efficiency and Accuracy: Automated systems eliminate manual errors by systematically recording hazard data. This helps businesses track risks with precision and generate reports faster.
- Regulatory Compliance: A software solution simplifies adherence to workplace safety regulations by keeping track of evolving legal and industry hygiene requirements.
- Real-Time Monitoring: Automated tracking detects hazards instantly and provides alerts, allowing businesses to address safety concerns before they escalate.
- Centralized Documentation: Digital tools store all hazard assessment reports in a single platform, making compliance with OHSAS guidelines easier to manage and audit.
Final Thoughts
Conducting a hazard assessment is a major compliance requirement, and it directly impacts workplace safety, employee well-being, and business continuity. Identifying risks and implementing safety measures helps prevent accidents and costly liabilities.
Using OHSAS software solutions simplifies this process by automating assessments, tracking compliance, and generating real-time reports. A digital approach minimizes paperwork and integrates safety measures into daily operations seamlessly.
Effivity’s OHSAS software solution is designed to help businesses conduct hazard assessments efficiently. Schedule a consultation call with the Effivity team today to learn how it can enhance your workplace safety practices.