If you’ve recently implemented a quality management software (QMS), here’s a truth-bomb: it isn’t foolproof.
Yes, even the best quality management system can hit a snag. With a growing business, it’s only realistic for a QMS to lose its edge over time.
Unless it is regularly monitored to eliminate such inefficiency and improve the effectiveness of the system.
Enter quality audits. A structured approach to assessing different aspects of a QMS, finding out loopholes, and addressing the pressing issues
In this blog, we’ll explore the meaning, types, and objectives of auditing. So that by the end, you’ll have a proper understanding of quality audits, their goals, and their significance.
What Is a Quality Audit?
A quality audit involves examining an organization’s quality management system to ensure its performance meets the best practices and compliance standards.
The goal is to identify non-conformities in the QMS and understand the causes behind such deviations to improve product/service/process consistency, and customer satisfaction.
Types of Quality Audits
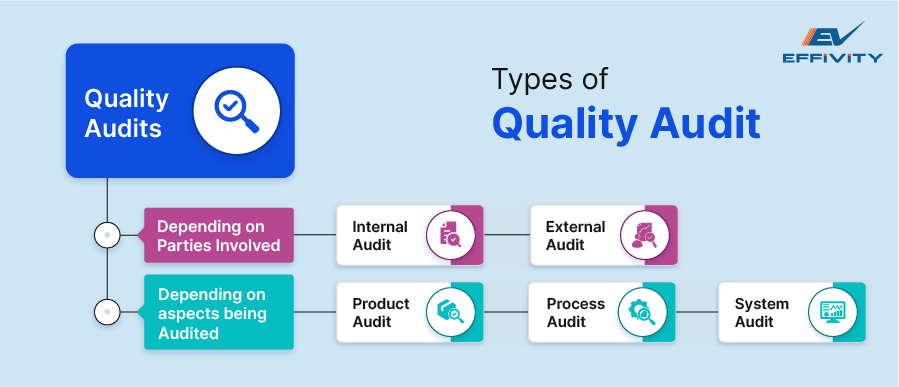
There are mainly two types of quality audits—internal and external.
As the name suggests, internal audits are conducted internally, i.e., without the interference of any external party. The primary objective of an internal audit is to conduct a period assessment of the QMS to ensure its alignment with the quality objectives of the organization.
External audits, on the other hand, are performed by auditing firms or certification bodies outside the organization. This is mainly done for compliance and certification purposes.
Here’s a comparison table for you to understand the differences better:
Aspect | Internal Audits | External Audits |
---|---|---|
Goal | Evaluate and improve the effectiveness of the QMS | Check the QMS for compliance with external standards and regulations |
Auditor | Internal auditors or employees of the organization | Independent auditors, auditing firms, and certification bodies |
Frequency | Once every 1-2 years | As required by the standards. For example, an ISO 9001 audit should be conducted once every 3 years. |
Cost | Low, since it is conducted by the employees | High |
Certification | Internal audits do not lead to certification | Yes, if the external audit is associated with certification as the end goal. |
Quality audits can also be categorized into product, process, and system audits, depending on the aspect being assessed.
What Are the Objectives of an Audit?
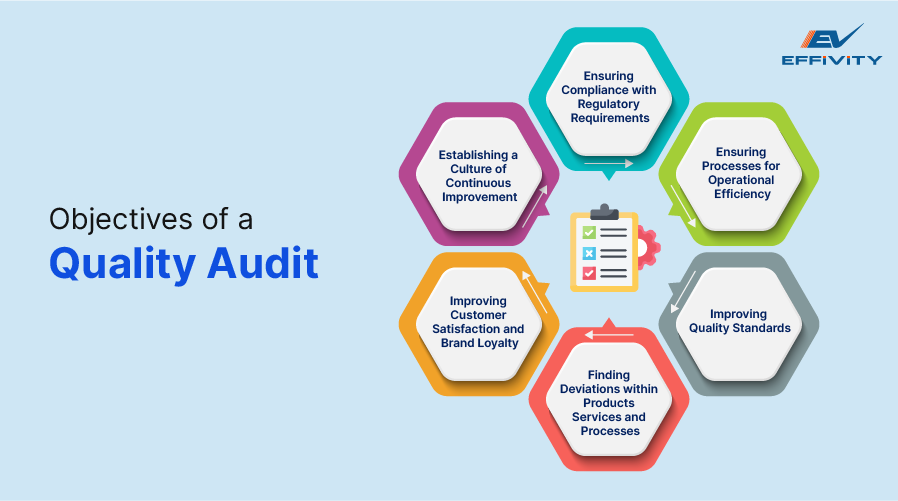
Given below are the 6 objectives of quality audits:
1.Ensuring Compliance
Both internal and external audits aim to verify the adherence of the QMS to the industrial and regulatory requirements. This involves a meticulous process and documentation review to identify deviations from established standards like ISO 9001.
As a result, organizations can avoid legal fines, risks, and penalties besides losing their reputation and name in the market for poor quality standards.
For example, by identifying problems within a QMS, a food processing facility can level up its sanitation procedures, storage practices, etc
2. Enhancing Processes
A quality audit helps analyze operational processes, workflows, and production lines to pinpoint inefficiencies. Thus, organizations can streamline and manage operations, depending on the audit findings.
For example, quality audits can bring forward issues like equipment failure and improperly planned layouts that cause production delays in a manufacturing plant.
They are also useful in recommending process improvement methods like implementing lean principles, automation, integration, encouraging employee and customer feedback, and so on.
3. Improving Quality Standards
Besides ensuring compliance with international standards like ISO 9001, conducting quality audits is crucial for evaluating the effectiveness of quality control measures. This means checking product testing protocols, defect detection mechanisms, infection control measures, etc.
It helps inspect products and services in detail to discover areas for quality enhancement. For example, design improvements and service delivery standards.
4. Finding Deviations
It’s not only important to tackle compliance deviations, but also inconsistencies within products, services, and processes.
Standardization is the best way to enhance operational efficiency. And for that to happen, organizations must track non-conformities within their systems and offerings.
By thoroughly reviewing processes, products, and services, quality audits assist in identifying non-conformities and documenting them for traceability, clarity, and corrective actions.
Root cause analysis is a fundamental part of quality audits where auditors dig deeper into the deviations to understand and address underlying causes.
5. Meeting Customer Satisfaction
A major objective of an internal audit is to assess customer feedback to improve the current level of customer satisfaction.
This is done by analyzing customer surveys, complaints, enquiries, and suggestions. The goal is to understand where your business stands in terms of product quality, service delivery, complaint resolution times, escalation procedures, and overall experience.
By identifying factors that influence brand perception and customer trust, you can implement strategies to meet customer expectations, increase retention, and enhance your reputation.
6. Continuous Improvement
Quality audits are necessary to establish a culture of continuous improvement. So that an organization strives to lead with innovation and adaption at the core.
With key performance metrics, benchmarking, and management review meetings, you can evaluate the effectiveness of the QMS. These strategies are crucial for ongoing enhancement and embracing change as a business expands.
Meet All the Objectives of a Quality Audit with Effivity
Running manual quality audits is super cumbersome. They consume a lot of time and are highly prone to human error, bias, and negligence.
Effivity’s QMS software brings a one-step solution to implementing an auditing process that covers all objectives of a quality audit. Our modules are ISO 9001 certified, including “Internal Audit”, where you can:
- Create a master internal audit schedule to track each audit
- Define specific plans for every single audit separately
- Receive automated alerts
- Create internal audit reports to document audit findings
- Record non-conformance, identify the root cause, and take the necessary corrective action
And that is just the tip of the iceberg. With our QMS software, you can manage risks, control purchases, create quality policies, and manage design and development.
Book a free trial today to get started!