Workplace safety isn’t something you leave to chance. You must keep your employees safe while ensuring your practices are compliant.
Hazard Identification and Risk Assessment (or HIRA) is a process that keeps potential dangers in check before they escalate into big disasters. It’s the ultimate safety net that helps businesses foresee and assess risks, as well as take the necessary actions to mitigate them.
But how do you actually put this into action? Answer: HIRA Sheets.
In this post, we’ll break down the concept of HIRA sheets—definitions, key components, and benefits. Later on, we’ll take a look at some common mistakes to avoid when filling out these sheets.
What Is a HIRA Sheet?
In simple words, a HIRA sheet helps you document and assess all the risks associated with your business in a structured manner.
You can capture details like potential hazards for each task, current conditions, risk to personnel, legal requirements, and current controls (engineering, administrative).
As a result, a HIRA sheet gives you a comprehensive view of all the threats and vulnerabilities at your workplace. This helps you stay on top of all the ISO 45001 hazards and risks so that you can implement necessary controls in time (or even before).
Key Components of a HIRA Sheet
A well-structured HIRA sheet is made up of several key components. Let’s understand them one by one:
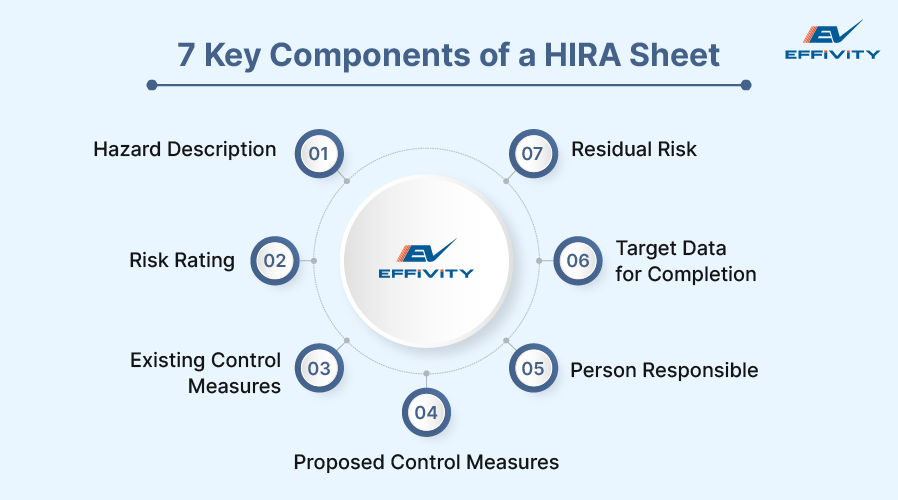
1. Hazard Description
The hazard description is the first thing that you’ll see in the HIRA sheet. These are potential sources of harm that could affect your workplace safety.
Hazards are mainly categorized as chemical (exposure to toxic substances), biological (exposure to infections or disease), physical (electrical or vehicle hazards), and environmental (extreme temperatures).
2. Risk Rating
Next, each hazard is assigned a risk rating in the HIRA sheet. This rating mainly consists of two elements: the severity of the hazard and the likelihood of it happening.
These ratings are often scored on a scale from low to high so that the overall risk level can be clearly understood at just a glance.
3. Existing Control Measures
This section of the HIRA sheet outlines what’s already in place to manage or mitigate the risk. It includes safety protocols, protective equipment, signage, and engineering solutions like ventilation systems or machine guarding.
4. Proposed Control Measures
Sometimes, existing controls aren’t enough, and that’s where the proposed control measures section comes in. Here, you list additional actions or precautions needed to reduce the risk further.
5. Person Responsible
Every HIRA sheet contains the names of the individuals or teams responsible for implementing the control measures and ensuring that hazards are properly addressed.
6. Target Date for Completion
This component specifies when each control measure should be implemented. This is useful for creating and managing the timeline for addressing hazards in an organized manner.
7. Residual Risk
Even after controls are in place, some risks may still remain. These are called residual risks.
An ideal HIRA risk assessment template has a section for documenting residual risks so that you get a realistic view of the remaining risk levels.
Benefits of Using HIRA Sheets
So, why do HIRA sheets matter and how can they help improve workplace risk management? Let’s find out:
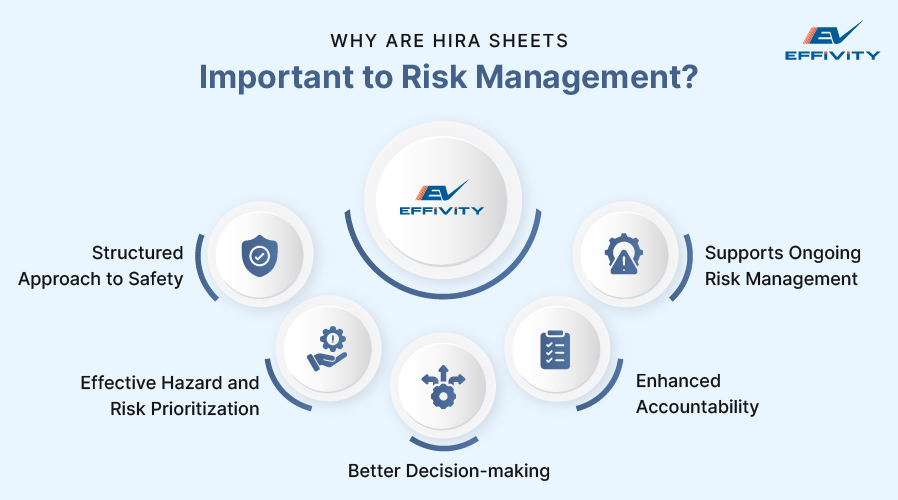
1. Systematic Hazard Identification
The biggest benefit of using a HIRA sheet is its structured approach to hazard identification. With a clear format that covers every angle (hazards, risks, control measures, etc.), these sheets ensure that no potential danger is overlooked.
2. Enhanced Risk Prioritization
Risk ratings assigned to each hazard help visualize risks in a way that allows for more efficient resource allocation. Businesses can address the most critical hazards first.
3. Accountability and Clear Action Plans
HIRA sheets create transparency by clearly assigning responsibility for implementing control measures. When tasks are documented with the person responsible and a target date, it becomes easier to track progress and ensure accountability.
4 Common Mistakes to Avoid When Using HIRA Sheets
Even though HIRA sheet formats are designed to simplify risk management, there are a few common pitfalls that can reduce their effectiveness:
1. Being Too Vague
Phrases like “electrical issues” or “chemical exposure” don’t provide enough detail for anyone reading the sheet to fully understand the risk. Therefore, always aim to provide clear, detailed descriptions.
2. Not Covering All HIRA Sheet Components
Some people rush through the process and skip assigning detailed risk ratings. While others may forget to mention the safety measures already in place.
Neglecting these key components creates an incomplete picture of workplace safety.
3. Not Updating the Sheet Regularly
A HIRA sheet isn’t a one-time task. Failing to update it on a regular basis can leave the company vulnerable to new risks.
4. Ignoring Residual Risk
There’s always some level of residual risk left even after putting control measures in place. Neglecting to document this means you might be unaware of the ongoing risks that need further attention.
Conclusion
While HIRA sheets form an indispensable part of the health and safety management system, handling them manually can be a real challenge. Tracking every hazard, updating risk ratings, and ensuring all control measures are documented correctly takes time and effort.
This is where Health and Safety software comes in. With built-in HIRA tools and sheet templates, the software automates the entire process. As a result, you can fill out, update, and track HIRA sheets seamlessly.
Plus, with this software, there’s no need to consult long-winded HIRA PPTs or manuals to figure out how to prepare or manage these sheets. Everything you need is already built-in (think customizable HIRA risk assessment templates).
So, if you’re ready to simplify your HIRA sheet management, our HSE software is the perfect solution. Start a free 15-day trial today to see how our HIRA sheets work and take your workplace safety to the next level!