Perfume manufacturing is a precise science and an art. It takes time and laborious processes to manufacture a bottle of perfume, and each bottle needs to meet precise standards every time. Perfume manufacturers need to have a comprehensive quality management system in place to deliver consistent results each time.
However, manually managing quality processes is an error-prone and resource intensive task. It often leads to inconsistent quality and delays in production. Additionally, keeping up with industry specific and quality related ISO standards can be challenging and failing to comply leads to failed audits and potential legal issues.
The Saudi Arabian perfume manufacturer decided to address quality management issues proactively by approaching Effivity for a solution. After detailed consultation calls, the Effivity team suggested the adoption of an Integrated QHSE Management Software. Here's how the Saudi-based perfume company benefited from this.
About the Organization
The Saudi Arabian perfume manufacturer is a leading producer of exquisite fragrances, blending traditional Arabian perfumery with modern innovations. Their products appeal to perfume connoisseurs in Saudi Arabia and internationally. The focus of the organization is on quality and authenticity and they have established themselves as a premium brand in the global perfume industry.
Challenges Faced by the Saudi Arabian Perfume Manufacturer
- The organization struggled to keep up with technological advancements and emerging ISO requirements.
- Implementing and maintaining their quality management system felt overwhelming and daunting.
- Manually entering data and tracking changes consumed a lot of time.
- Following up with colleagues, sending reminders, and sorting documents was inefficient.
- They were unsure if they had everything covered when it was time for audits.
- Controlling processes and product quality to meet industry norms was challenging.
- Language barriers across their global operations made communication difficult.
- They lacked the tools to move to an integrated management systems audit model efficiently.
Effivity's Solutions
To tackle the challenges they faced, we provided the Saudi Arabian perfume manufacturer with our comprehensive Quality Management Software. Our integrated solution automated their ISO compliance processes and streamlined their operations.
Key Features Offered
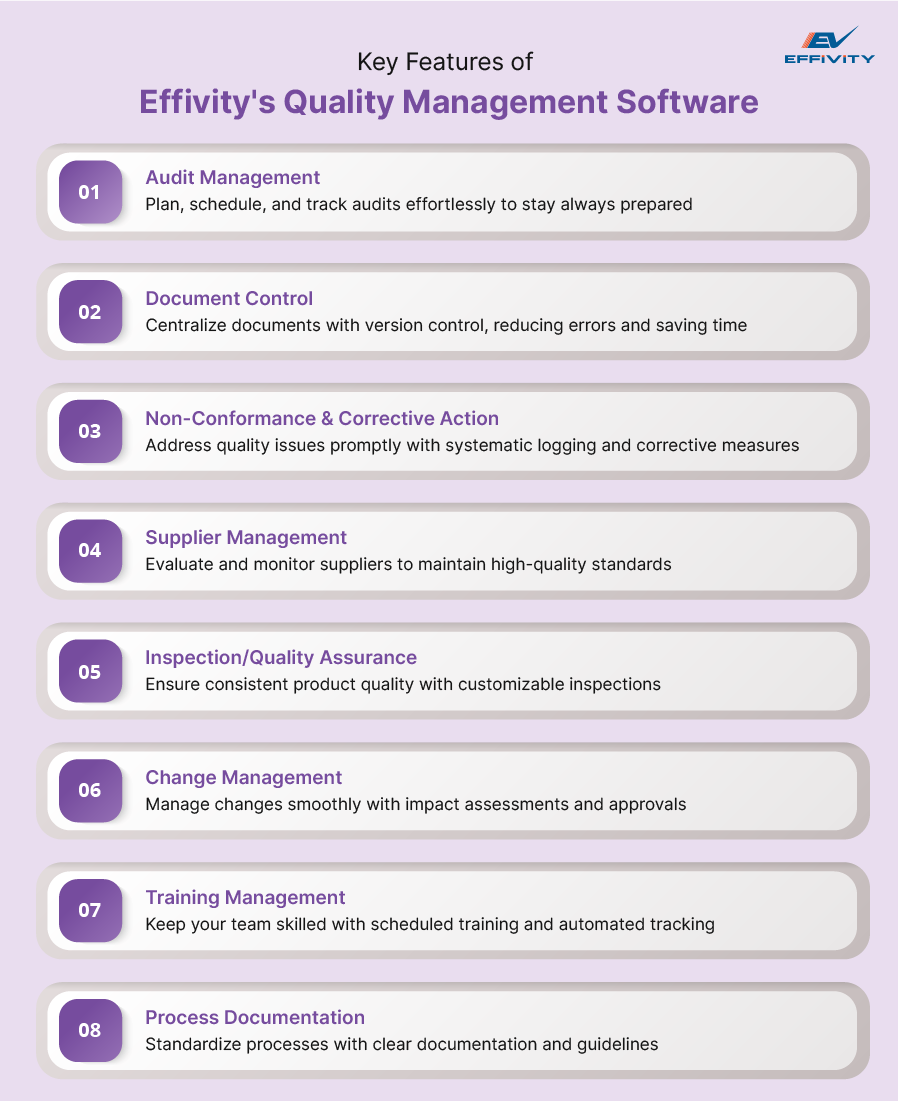
1. Audit Management
Our Audit Management module transformed how the perfumer handled audits. Instead of feeling uncertain, the organization could now plan, schedule, and execute audits with ease. The module allowed the company to track findings, assign corrective actions, and monitor progress in real time.
2. Document Control
With Document Control, the company moved away from manually stacking and sorting documents. All critical files were centralized in a secure digital repository. Version control and automated workflows meant everyone in the organization had access to the latest documents. This reduced confusion and errors.
3. Non-conformance and Corrective Action
Quality issues were addressed more effectively using our Non-Conformance and Corrective Action module. The perfumer could easily log non-conformances, identify root causes, and implement corrective measures.
This helped them prevent recurring problems and improve overall product quality.
4. Supplier Management
Our Supplier Management module gave the organization better control over its supply chain. The company could evaluate and monitor supplier performance from a centralized platform. Tracking certifications and managing approvals became easier and ensured that suppliers met the perfumer's quality expectations.
5. Inspection/Quality Assurance
With the Inspection/Quality Assurance module, the perfumer could plan and record inspections at various production stages using customizable checklists. Real-time data capture allowed the company to quickly identify and resolve any issues.
6. Change Management
Effivity's Change Management module helped the organization manage changes to processes, products, or documents seamlessly. The company could assess the impact, obtain necessary approvals, and communicate updates effectively.
7. Training Management
Keeping the staff trained and competent was made easier with our Training Management module. The perfumer could schedule, track, and document all training activities. Automated reminders ensured that employees completed required training on time.
8. Process Documentation
Standardizing processes was essential for consistency and quality. Our Process Documentation module enabled the organization to map out and document all critical procedures. Clear guidelines were provided for the team, reducing variability and ensuring adherence to best practices.
Final thoughts
By adopting Effivity's Quality Management Software, the Saudi Arabian perfume manufacturer overcame compliance challenges and streamlined its operations. They automated processes, reduced manual workload, and gained confidence in their ISO compliance, ensuring they were always audit-ready.
Effivity's comprehensive and configurable Quality Management Software solution is the ideal partner for all organizations seeking to automate and streamline ISO compliance processes. With powerful features like task workflows, alerts, effective reporting, and multilingual support, Effivity helps businesses achieve high levels of process excellence.
If you're looking to transform your quality management and ensure compliance with ease, contact the Effivity team for a consultation call today.
Frequently Asked Questions
1. What is the goal of ISO certification?
The goal of ISO certification is to help your organization consistently meet customer and regulatory requirements by following internationally recognized quality management standards. By achieving ISO certification, you demonstrate your commitment to quality and continuous improvement, which brings new business opportunities and builds trust with clients.
2. How do you implement a quality management system in a company?
Implementing a quality management system (QMS) starts with understanding the relevant ISO standards for your industry. You'll want to assess your current processes and identify areas for improvement.
Engage your team in documenting procedures, setting quality objectives, and establishing clear roles and responsibilities. Training is crucial to ensure everyone is on board. Using QMS software like Effivity can streamline this process by automating tasks and keeping everything organized.
3. Who is responsible for QMS in the organization?
While there might be a designated Quality Manager or compliance officer, the truth is that everyone in your company has a role in the QMS. Top management sets the direction and goals and provides resources, but each team member contributes by following procedures and striving for excellence in their daily tasks.
A successful QMS relies on collective responsibility, where collaboration and commitment to quality must be achieved at every level of the company.