Italy-based precision engineering organization successfully fine-tuned their ISO 9001 implementation with Effivity's bespoke quality management software solution. The precision engineering distribution and support industry is highly competitive and crowded. The field has many players as it caters to various sectors like automotive, aerospace, and general manufacturing. The products distributed by the organization have diverse applications and, by extension, a global supply chain.
To remain competitive, companies in this industry must maintain high standards in quality, efficiency, and productivity. However, owing to the market's high precision requirements and stringent regulations, without a proper quality management system in place, this can be quite challenging. The Italy-based organization approached Effivity for assistance with deploying a digital quality management system to meet internal and ISO 9001 standards.
Effivity's quality management system software solutions tailored to specific business and industrial requirements helped the organization achieve ISO 9001 implementation and certification and set new benchmarks for quality management. Read along to learn more about this success story.
About the Organization
Founded in 1981, this company is a leading provider of deburring, finishing, and superfinishing tools and equipment, serving precision engineering, automotive, and aeronautics sectors. They go beyond distribution and offer solutions to production and mechanical processing challenges.
Their dedication to providing superior quality shines through in their top-notch products, specialized technical assistance, and bespoke solutions crafted to optimize manufacturing processes. With deep industry expertise, a dedication to innovation, and a customer-centric approach, they empower businesses to optimize operations, maintain high standards, and achieve superior product quality.
Challenges Faced
The Italy-based precision engineering organization faced several challenges in relation to quality management and ISO implementation and compliance. Below are the key issues they encountered:
Stringent Industry Standards
The precision engineering, automotive, and aeronautics sectors have very high precision requirements. Meeting these standards consistently without an efficient quality management system proved difficult. Stringent regulations required meticulous documentation and adherence to quality benchmarks, which was challenging without digital tools.
Complex Supply Chain
The organization deals with a diverse range of products and applications in various sectors. Managing a global supply chain added complexity to ensuring consistent quality across all products and regions. Keeping track of compliance across different countries with varying regulations required significant effort and resources.
Manual Processes and Human Errors
Manual quality management processes were prone to errors and inconsistencies. This impacted the ability to maintain high standards and led to delays in detecting and addressing issues. The lack of standardized processes made it hard to ensure that all employees followed the same procedures, leading to variability in product quality.
Internal Audit Challenges
Planning and conducting internal audits manually was time-consuming and prone to oversight. It was difficult to ensure that all necessary processes were audited regularly and thoroughly. Generating audit reports and tracking the status of corrective actions manually was inefficient and led to delays in addressing non-conformities.
Compliance Tracking
Tracking compliance with ISO 9001:2015 standards and other regulatory requirements was challenging without a centralized system. The absence of real-time visibility into compliance status made it hard to identify and rectify gaps promptly.
Data Management
Managing vast amounts of data related to quality control, audits, and compliance manually was cumbersome. It was difficult to maintain accurate records and retrieve information when needed.
Management Reviews
Conducting management reviews involved coordinating schedules, preparing documents, and ensuring attendance from relevant stakeholders. Documenting and tracking action items from management reviews was challenging without a digital system, leading to delays in implementing improvements.
Effivity's Solutions for ISO 9001 Implementation
Effivity provided a comprehensive suite of solutions that addressed the organization's quality management and ISO compliance challenges. Here are the key features and benefits of Effivity's quality management system software:
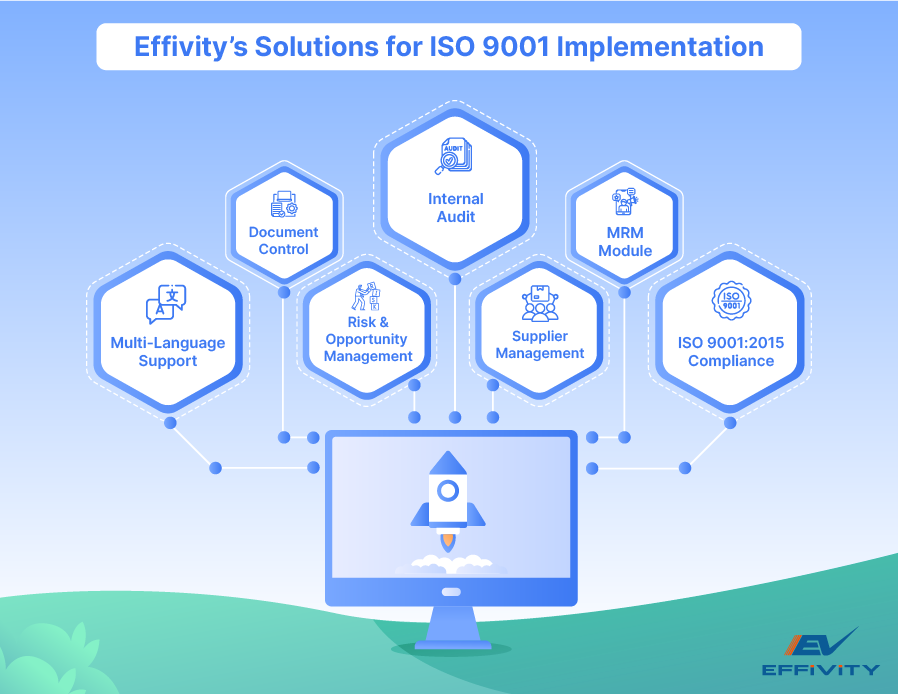
1. Internal Audit Module
Effivity's internal audit module made planning and conducting audits simple. Automated scheduling ensured audits were planned in advance and notifications were sent to relevant stakeholders. Pre-defined checklists covered all quality management system (QMS) requirements, ensuring thorough audits. Real-time tracking of audit status allowed easy monitoring and follow-up on corrective actions. Effivity generated detailed audit reports automatically, saving time and reducing errors.
2. Multi-Language Quality Management System
Effivity's software supports 7 languages, including the organization's native language. This feature made it easy for employees across different regions to use the system without language barriers. The user-friendly interface ensured that employees could navigate and utilize the software efficiently. Multi-language support facilitated better communication and understanding of quality processes.
3. Management Review Module (MRM)
The MRM module streamlined the entire management review process. Scheduling reviews, identifying attendees, and preparing documents were all handled within the module. Automated notifications reminded attendees about upcoming reviews, ensuring full participation. The module allowed for easy documentation of meeting agendas and minutes. Post-review, action items were tracked to ensure timely implementation of decisions.
4. Document Control
Effivity's document control feature centralized the management of all QMS-related documents. It ensured that all documents were up-to-date, accessible, and version-controlled. Employees could quickly find the latest versions of documents, reducing the risk of using outdated information. The system tracked document revisions and approvals, ensuring compliance with ISO 9001:2015 requirements.
5. Risk and Opportunity Management
Effivity's software included tools for identifying and managing risks and opportunities. The system facilitated proactive risk assessment, helping the organization anticipate and mitigate potential issues. It also identified opportunities for improvement, driving continuous enhancement of quality processes. Real-time tracking and reporting enabled quick responses to emerging risks and opportunities.
6. Supplier Management
Effivity's supplier management module helped the organization maintain high standards across its supply chain. It tracked supplier performance, ensuring that all suppliers met the required quality standards. The system facilitated regular evaluations and audits of suppliers. Supplier-related data was centralized, making it easy to monitor and manage supplier relationships.
7. Meeting ISO 9001:2015 Requirements
Effivity's solutions were designed to help organizations meet and maintain ISO 9001:2015 certification. The software ensured that all QMS processes were documented, controlled, and monitored. It provided tools for continuous improvement, aligning with ISO 9001:2015's focus on quality enhancement. Regular updates ensured that the system stayed compliant with the latest standards and regulations.
Effivity's quality management software provided the Italy-based precision engineering organization with the tools needed to overcome its challenges. If you wish to experience similar results in your organization, visit the Effivity website to learn more and set up a call with our team!
Frequently Asked Questions
What is the process involved in implementing ISO 9001 standards?
As a first step, assess your current practices to pinpoint areas that require enhancement or alignment with the standard. Next, develop and document quality management processes that meet ISO 9001:2015 standards. Finally, train your staff, implement the processes, and conduct internal audits before undergoing an external certification audit.
What are the benefits of using a digital quality management system over traditional manual process?
A digital quality management system automates documentation and tracking, reducing errors and saving time. It provides real-time visibility into quality metrics, making managing compliance and improving processes easier. Centralized data storage also simplifies audits and ensures consistency.
Can Effivity's software be customized to meet different industries and business requirements?
Yes, Effivity's software is highly customizable to meet the specific needs of various industries. You can tailor its features to match your unique business processes and regulatory requirements, ensuring a perfect fit for your organization.