Quality control and assurance are some of the most important aspects to consider when managing a successful operation. They ensure that products and services meet and quality standards required by the industry. This also helps ensure that brand reputation, legal requirements, and customer satisfaction are all met. Defects are minimized, and operational efficiency and process streamlining are improved. All of these factors contribute to the overall growth and success of an organization's.
This article will discuss quality control and assurance, why they are essential, how they work, and the difference between quality control (QC) and assurance (QA).
What is Quality Control?
Quality control refers to the process businesses follow to maintain and improve their product quality. Quality control, or QC, requires organizations to create environments where employees and management consistently strive for perfection. This may be achieved through implementing Quality Management Software (QMS), rigorous employee training, making the necessary benchmarks for product quality, and regularly testing products to look for variations.
One of the significant aspects of quality control is the ability to define and establish specific controls throughout the organization. These controls help standardize production and protocols for dealing with quality issues, and determining which production activities will be carried out by which personnel is also essential. This ensures that employees only complete tasks they have been well-trained for, reducing the risk of errors.
Why Is Quality Control Important?
Designing and manufacturing products takes time, capital, and resources. This is a time-consuming process. When companies develop products, they must meet regulatory, health and safety guidelines. Additionally, manufacturing processes need specific regulations and rules to ensure employee safety.
Delivering defective pieces and products with quality issues can damage a brand's reputation and leave organizations open to legal action. This could be caused by any injuries, illnesses, reactions, or other problems arising from the product. To prevent these problems, organizations employ quality control management systems and inspectors to identify and rectify defects in products or manufacturing processes.
How is Quality Control Maintained?
In most cases, quality control and testing must be done at every manufacturing process step. This begins with testing raw materials, checking samples during production, and testing the final products. Testing is required at every stage to identify problems early on and allows the business to take action to prevent mistakes in the future.
Quality control usually involves audits and inspections for businesses that do not require manufacturing. It could also affect customer feedback surveys and questionnaires, customer service evaluations, and more. This helps organizations understand how their client base has received the product, what they dislike about it, and what they can change to meet customer expectations. The two most significant requirements for quality control are that the end product follows legal regulations and safety standards.
It is also important to note that quality control methods and standards can vary widely, depending on the industry. For example, quality control ensures that users can consume products in the food and drug industry. Several chemical and biological tests are conducted during production to ensure that these do not make consumers ill.
What is Quality Assurance?
Quality assurance, or QA, refers to businesses processes to establish standards, guidelines, and procedures to reduce the risk of quality-related problems. It also helps maintain the integrity of the product through all stages of development. Often, quality assurance and quality control are confused. However, quality assurance vs. quality control are distinct processes.
The International Organization for Standards, commonly called the ISO, leads global quality assurance practices. This organization is responsible for determining and mapping businesses processes to implement quality assurance. ISO began in the manufacturing industry and now encompasses almost all others, including software.
For example, many businesses use ISO 9000 certification to ensure the effectiveness of quality assurance systems. ISO 9000 can help organizations meet regulatory requirements and improve customer experiences.
Why is Quality Assurance Important?
Quality assurance is an integral part of a business. It allows companies to produce high-quality products that build customer trust and brand image. Quality assurance programs define clear-cut standards and procedures to prevent defective manufacturing before they arise.
How is Quality Assurance Maintained?
Quality assurance involves establishing pre-defined objectives and standards. This is done by identifying the goals of a product or service, regulations that will help maintain customer satisfaction and regulatory requirements. After these quality benchmarks have been established, manufacturing processes and final products can be assessed. Quality assurance involves planning, quality assurance process design, and quality assurance testing.
QA vs QC: What is the Difference?
Quality control and quality assurance are sometimes used interchangeably. However, the two processes are distinct and refer to different aspects of quality management. The differences between the two can be broken down into the following:
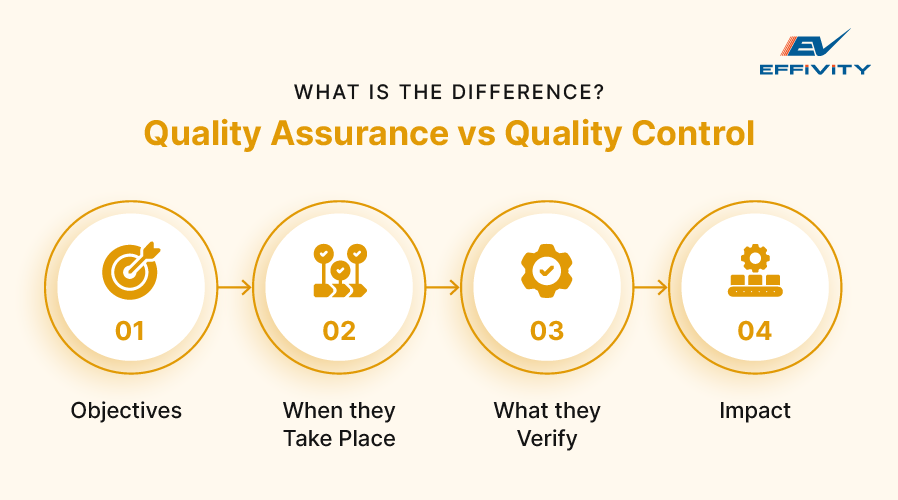
1. Objectives
Quality control is focused on detecting and correcting defects in the final product before it goes to the consumer. On the other hand, quality assurance aims to prevent these defects by defining and maintaining specific regulations and standards.
2. When They Take Place
Quality assurance is a continuous process that takes place from planning until execution. It ensures that all procedures are followed correctly. Quality control usually occurs at the end of production, when final products are ready for inspection.
3. What They Verify
Quality assurance aims to verify that all procedures and standards are adhered to. It aims for reliability and consistency in production and product quality. Quality control aims to confirm that the final product meets safety requirements and other standards before it reaches the final consumer.
4. Impact
Quality assurance focuses on the long-term. It impacts the entire production process, from planning to manufacturing to final sale, and establishes procedures for every stage to prevent defects. Quality control has a more immediate effect and mainly relates to the specific batch or product being inspected. It ensures any defects are remedied before they reach the final consumer.
In the End
Quality assurance and quality control are distinct yet key pillars of delivering exceptional products or services. While QA focuses on processes to prevent defects, QC identifies and resolves issues in the final output. Together, they ensure reliability, efficiency, and customer satisfaction in your business offerings.
With the integration of these aspects, you can uphold high standards, minimize risks, and consistently exceed expectations, fostering trust and long-term success in competitive markets.