Inventory management is the process businesses follow to order, store, sell or use their inventory. This inventory could be raw materials, finished products or components of products. There are countless inventory management methods, each with its advantages and disadvantages.
In this article, we will delve into what inventory management is, its benefits and the 7 types of inventory management.
What is Inventory Management?
Inventory management system is one of the crucial components of business and allows companies to identify which stock to order and when. It encompasses the order and purchase of stock, its storage, use and sale to final customers. Inventory could refer to raw materials, finished products or components.
Inventory management ensures that organizations do not have a shortage of stock or an excess of products building up. This ensures that customer orders are always fulfilled and that proper warning is always given before major shortages occur. An excess of stock can lead to a reduction in cash flow and difficulty storing the products.
Why Is Inventory Management Necessary?
Inventory management comes with several benefits for organizations. These include:
1. Being Able to Fulfil Orders
Failing to stock up your inventory might mean fulfilling customer requests and orders won't be possible when they come in. This can lead to a reduction in customer satisfaction and a loss in profits.
2. Saving Money and Resources
Inventory management allows businesses to study trends to help them better use their stocks. Additionally, warehouse inventory management can be optimized to decrease the amount of unusable stock before sale.
3. Improving Cash Flow and Satisfied Customers
Proper inventory management also leads to better cash flows and increased customer satisfaction. Customers can obtain their desired products without going through long wait times.
7 Types of Inventory Models and Management Strategies
Businesses can employ several inventory management models to meet their targets. Each one has pros and cons. Choosing the model that best suits your business's requirements is important. Some of the most popular methods include:
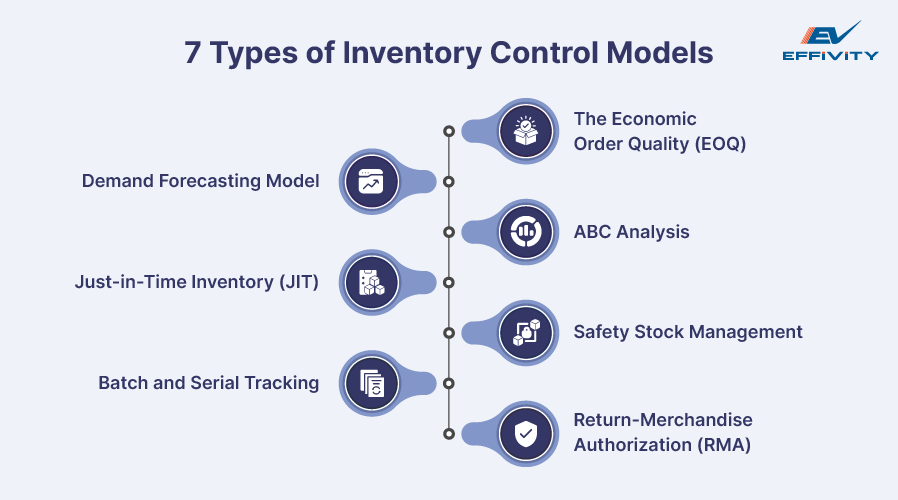
The Economic Order Quality (EOQ)
The economic order quantity management model or EOQ, is one of the most popular inventory strategies. It informs businesses of the inventory units they should order to reduce costs. These insights are based on the company's holding costs, ordering costs and demand rate.
However, the EOQ model does have drawbacks. For starters, it assumes the rate of demand ordering costs and unit price are always constant. This means that the EOQ will no longer be applicable in fluctuating demand.
Demand Forecasting Model
Demand forecasting can be an important tool for organizations. It uses historical data, market trends and other factors to predict the demand for a product. It can allow companies to maintain optimal inventory levels, reduce holding costs and storage expenses and provide insights to help businesses plan and schedule resource allocation.
ABC Analysis
The ABC analysis model is also a fundamental inventory management technique. Organizations categorize their products based on their significance to overall business operations. It allows organizations to classify products into 3 categories (A, B or C). Group A includes all high-value items that drive revenue, while Group B includes moderately valuable items. Group C consists of any low-value, less essential items. Time, resources and control efforts can then be allocated based on the importance of the category.
This model also continuously assesses and updates categorizations influenced by demand, strategic shifts or market conditions.
Just-in-Time Inventory (JIT)
JIT is a leading, strategy-focused inventory management method. This model works by only receiving goods as and when needed (hence, the name), which minimizes the holding costs and streamlined production processes. JIT's primary focus is on reducing waste, responding to changes in demand and streamlining production.
It has several benefits. These include on-demand ordering, meaning goods are purchased in quantities that satisfy the immediate customer (or production) requirements. It tries to minimize the need for extra or extensive storage facilities, which saves costs and manages strict coordination schedules with suppliers to ensure timely delivery. JIT also involves coming up with strategies for continuous improvement in delivery and production processes while reducing lead times.
Safety Stock Management
In this method, companies decide to implement a buffer in the form of excess stocks to safeguard themselves from any unexpected delays in the supply chain, growth in demand or other factors. It involves building and maintaining an inventory of this buffer stock on top of the expected demand. This inventory management technique ensures continuity in a product's availability, increasing customer satisfaction.
Its main benefits include robust risk assessment capabilities- this management system can identify potential risks related to sudden fluctuations in demand, unforeseen disruptions, supply chain problems and more. Additionally, it regularly assesses inventory levels and demand patterns to adjust buffer stock levels. Similarly, when the actual stock starts to deplete and reach the threshold for buffer stock, the Safety Stock Management system automatically triggers order replenishment.
Batch and Serial Tracking
This method is specifically designed to monitor individuals or groups of products, improving businesses' traceability and control over their stock. It is essential for industries that require strict accountability measures. Some of its significant benefits are that batches are divided and assigned unique identifiers, which facilitate tracking through the whole facility. It also records the movements of products from planning, production and sales.
Return-Merchandise Authorization (RMA)
The RMA is a process through which organizations can handle their product returns. It manages the return of items, facilitates clear communication with customers and ensures the proper accounting of returned items in the inventory. It includes getting a detailed reason for the return, documenting the conditions of the items upon return and creating updates in the inventory management system to reflect the change in products.
To Conclude
Effective inventory control is vital for optimizing resources, minimizing costs and meeting customer demands. From Just-in-Time (JIT) to Economic Order Quantity (EOQ) and ABC analysis, each inventory control model addresses specific business needs. Implementing the right strategy ensures smooth operations, reduces waste and improves decision-making.
A robust inventory management software like Effivity makes inventory control a breeze. The simple, easy-to-use platform ensures your organization can manage its stock, supply and customer satisfaction seamlessly.
Explore the website to know more about Effivity’s comprehensive solutions.